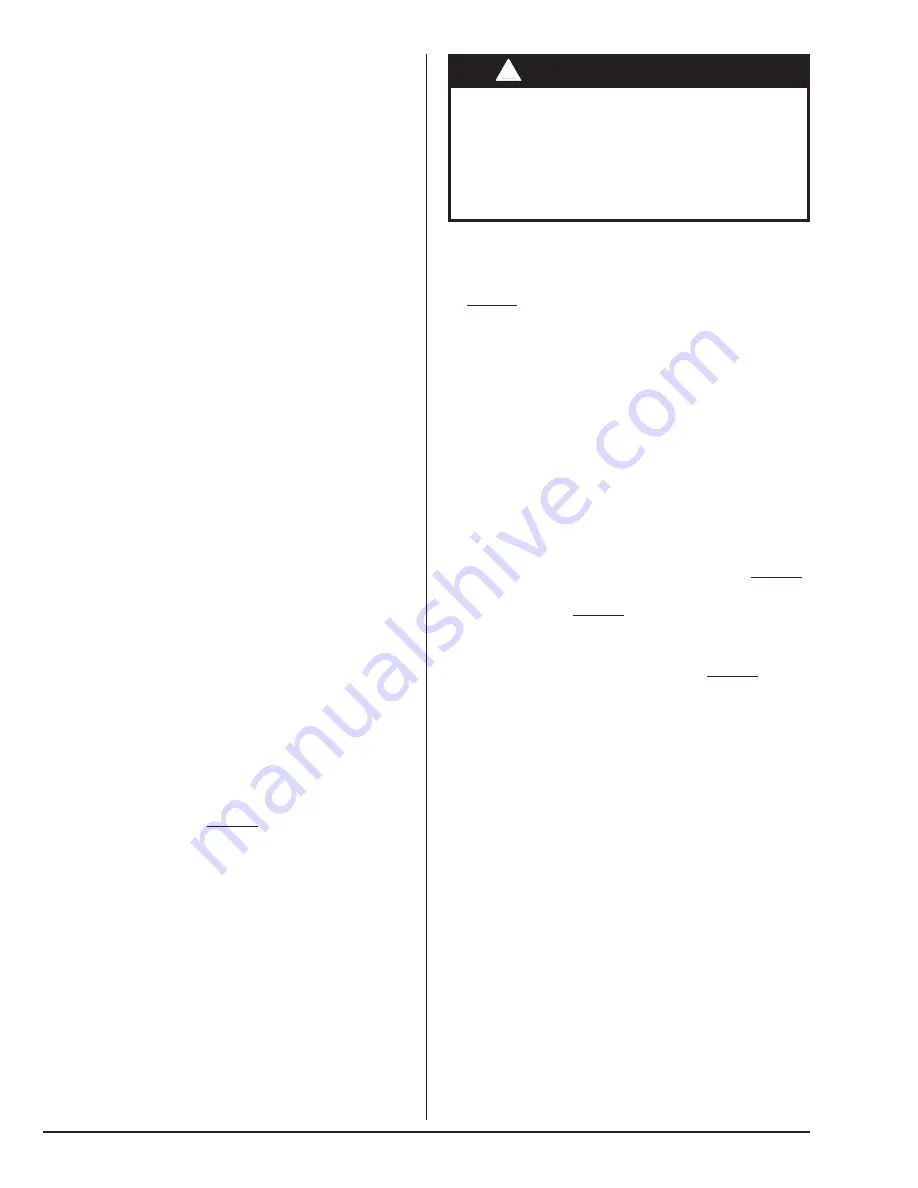
16
American Dryer Corp.
113279 - 9
!
WARNING
(CE Dryers)
This appliance must only be operated with the gas
type indicated on the dryer’s data plate. If the
appliance is converted (gas type changed), a data
plate amendment must be obtained from American
Dryer Corporation.
Conversions done improperly can result in a fire or
explosion!
Gas Pressure Testing
For proper operation, the gas pressure must be correct,
consistent and maintained at the gas pressure rates shown
on page 14. Provisions are made at the gas valve for taking
gas pressure readings.
There are two types of devices used to measure gas pressure.
They are the spring/mechanical type gauge and the
manometer. The use of the spring/mechanical type gauge is
not recommended because they are very easily damaged
and are not always accurate. The preferred type of gauge is
the manometer because it is a simple device to use and is
highly accurate. A manometer is simply a glass or transparent
plastic tube with a scale graduated in inches or millibar. When
it is filled with water and pressure is applied, the water in the
tube rises, showing the exact gas pressure.
Gas Pressure Test Procedure
Turn gas cock in gas supply line to “OFF” position.
50 Hz dryers: Back out miniature screw inside pressure tap
and attach manometer (refer to the illustration on page 15).
60 Hz dryers: Install pressure tap and attach manometer (refer
to the illustration on page 15).
Turn gas cock to “ON” position.
Start the dryer in Heat Mode and wait for ignition. Gas
manifold pressure should be as shown on page 14.
If the gas pressure needs to be adjusted, refer to “Gas
Pressure Adjustment” on this page.
Once test is complete, turn gas cock to “OFF” position.
Remove manometer. Tighten screw inside the pressure tap
or install plug.
Turn gas cock to “ON” position and check for leaks with soap
solution with main burner “ON.”
Preparation for Operation / Start-Up _
The following items should be checked before attempting to
operate the dryer:
• Read all “CAUTION,” “WARNING,” and “DIRECTION”
labels attached to the dryer.
• Check incoming supply voltage to be sure that it is the
same as indicated on the data label. In the case of 208
VAC or 240 VAC, the supply voltage must match the
electric service exactly.
• GAS MODELS – Check to ensure that the dryer is
connected to the type of heat/gas indicated on the dryer
data label.
• GAS MODELS – Be sure that all gas shutoff valves are
in the open position.
Instructions
Disconnect electrical power to the dryer.
Close all shutoff valves in dryer’s gas supply line.
Open the panel located just below the loading door.
Locate the gas train and disconnect the union, three electrical
plugs, and the gas train mounting screws from the burner.
Carefully slide the gas train out of the gas train enclosure.
(The carbon ignitor located at the far end of the gas train is
very fragile.)
Remove two burner tube mounting screws and remove burner
tube in order to gain access to the orifice.
Using a 3/8” wrench or socket, remove the existing orifice
and replace it with an orifice from the kit.
IMPORTANT: Use extreme care when removing and
replacing orifice (injector). This orifice (injector) is made of
brass, which is easily damaged.
Reinstall the burner tube onto the burner base.
Select from the following three options, the conversion to be
performed:
• Converting from unregulated propane to regulated
natural gas: use a flat screwdriver to remove the cap
with blocking pin and install the regulator vent cap from
the kit (ADC P/N 140415).
• Converting from unregulated propane to unregulated
natural gas: no change to the regulator is required.
• Converting from regulated propane to regulated
natural gas: remove the white plastic regulator
adjustment screw (under vent cap). Remove spring
under screw and replace with spring from kit (ADC P/N
140415). Replace regulator adjustment screw.
Install the gas train back into the dryer gas train enclosure.
Be sure the tab at the rear of the gas train engages into the
mounting slot.
Connect the union and the three electrical plugs.
Open all shutoff valves, reconnect electrical power to the
dryer, and test for leaks.
Operate the dryer through one complete cycle to ensure
proper operation.
With dryer operating, check the manifold (burner) pressure
at the tap on the gas valve to ensure proper operating
pressure (refer to chart on page 14).
Gas Pressure Adjustment
Disconnect electrical power to the dryer.
To adjust gas valve’s internal regulator, remove the regulator
vent cap. Once vent cap is removed, turn the plastic
adjustment screw in the valve. Turn the screw clockwise to
raise pressure and counterclockwise to lower pressure.
Gas (burner) pressures are measured with the burner in
operation for all burner adjustment conditions. Therefore
once the necessary adjustments have been made, the dryer
must be operated in a heating cycle to verify that the pressure
is correct. If it is not correct, you must discontinue the power
to the unit and make further adjustments. Repeat these steps
as many times as necessary to achieve the correct burner
pressure. Once the adjustment of the valve is complete, the
vent cap must be replaced and sealed with, for example,
paint to prevent maladjustment by the user.
Summary of Contents for AD22
Page 22: ...ADC Part No 113279 9 06 16 22 ...