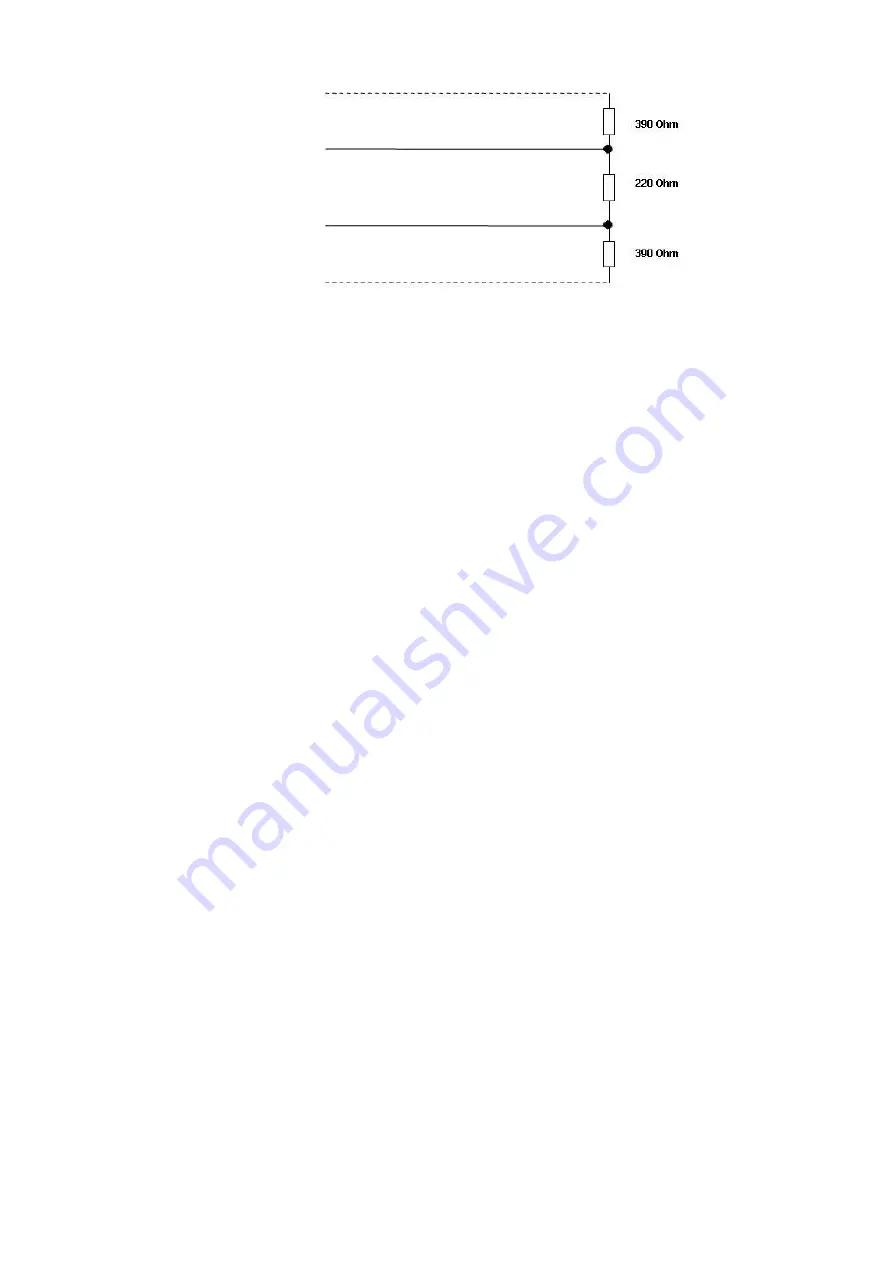
79
Figure 2 PROFIBUSCable terminator for cable (pin number of 9-pin D-type connector)
Profibus's bus terminator consists of a pull-up resistor and a pull-down resistor. When there is no station
transmitting data on the bus (ie idle time), these two resistors force different state voltages to a certain value, thus
ensuring that there is on the bus. A certain idle potential. The station designated as the terminating bus (common with
the bus terminator) needs to be added to the "terminator", also known as the active terminal. To achieve impedance
matching and enhance anti-interference ability. For the A-type cable, connect 220Ω active termination resistor.
The above information is for reference only. Due to the high content of Profibus-DP, please refer to the
PROFIBUS installation related specifications for details.
10.2 Profibus Communication function configuration
10.2.1 Profibus Communication variable table
When communicating with the Profibus protocol, the APM series programmable smart meter needs to use the
communication variables of this document. Chapter 8 Communication Description Section is invalid.
APM series multi-function electrical measuring instrument, its communication protocol is developed according
to DPV0. DPV0 is a periodic data exchange, that is, in each DP cycle, the exchanged data is periodic data.
The input data is: the response data fed back to the DP master by the multi-function electrical measuring
instrument (APM series meter
→
DP master station).
The output data is: the DP master sends to the multi-function electrical measuring instrument (DP master
→
APM series instrument), the instrument without switching output function (ie no DO function), no output data.
The processing of the cyclic data is done in the PLC by programming the input data and the output data. The
length of the input and output exchange data depends on the hardware configuration GSD file type.
(1) Profibus input data address table, as shown in Table 3. Its high byte is first and the low byte is after. For
example, [2][3], [2] is the high byte (high 8 bits), [3] is the low byte (lower 8 bits), and so on.
(2) If you want to set the APM series instrumentation parameters, you need to refer to Chapter 7 for manual
setting, or refer to Chapter 8 for setting by modbus-rtu protocol. You can not use Profibus remote operation setting.
(3) After the instrument is powered on, if the instrument slave address is changed (address setting value range
1~126), the instrument needs to be powered on again, and the changed slave address can be valid (this function
follows the PROFIBUS-DP protocol).
(4) After Profibus communication, the baud rate is adaptive from 9.6 kbit/s to 12000 kbit/s, and no baud rate is
required.
APM_Profibus Communication variable table
VP(Pin 6)
B-line(Pin 3)
DGND(Pin 5)
A-line(Pin 8)