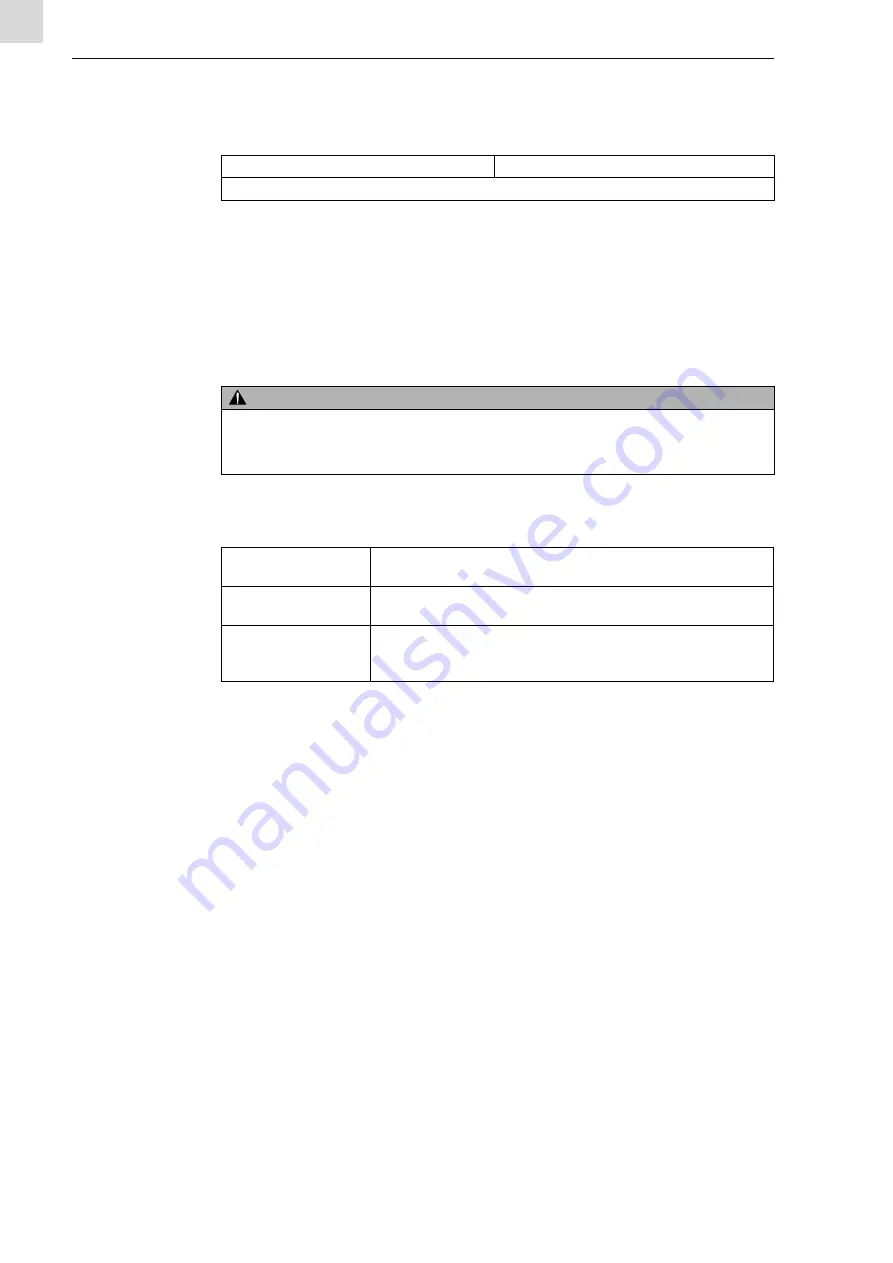
EN - 6
4 Scope of delivery
ABIMIG
®
SpinArc
®
4.1 Optional accessories:
The cable assemblies for the
ABIMIG
®
SpinArc
®
welding torch system are available in standard lengths
of 3 m, 4 m and 5 m as well as customer-specific lengths.
The equipment and wear parts must be ordered separately.
The order data and ID numbers for the equipment parts and wear parts can be found in the current
catalogue. Contact details for advice and orders can be found online at
4.2 Transport
Although the items delivered are carefully checked and packaged, it is not possible to fully exclude the risk
of transport damage.
4.3 Storage
Physical storage conditions in a closed environment:
Tab. 2 Ambient conditions, transport and storage on page EN-4
• Assembly kit for control device
• WS3 wire straightener
• Torch mount
Tab. 6
Optional accessories
WARNING
Risk of injury during transport of the device
There is a risk of injury when transporting and handling the device.
• Always wear your protective equipment and always comply with work safety regulations.
Goods-in inspection
Use the delivery note to check that everything has been delivered.
Check the delivery for damage (visual inspection).
In case of complaints
If the delivery has been damaged during transportation, contact the last
carrier immediately. Keep the packaging for possible checks by the carrier.
Packaging for returns
Where possible, use the original packaging and the original packaging
material. If you have any questions concerning the packaging and/or how
to secure an item during shipment, please consult your supplier.
Tab. 7
Transport