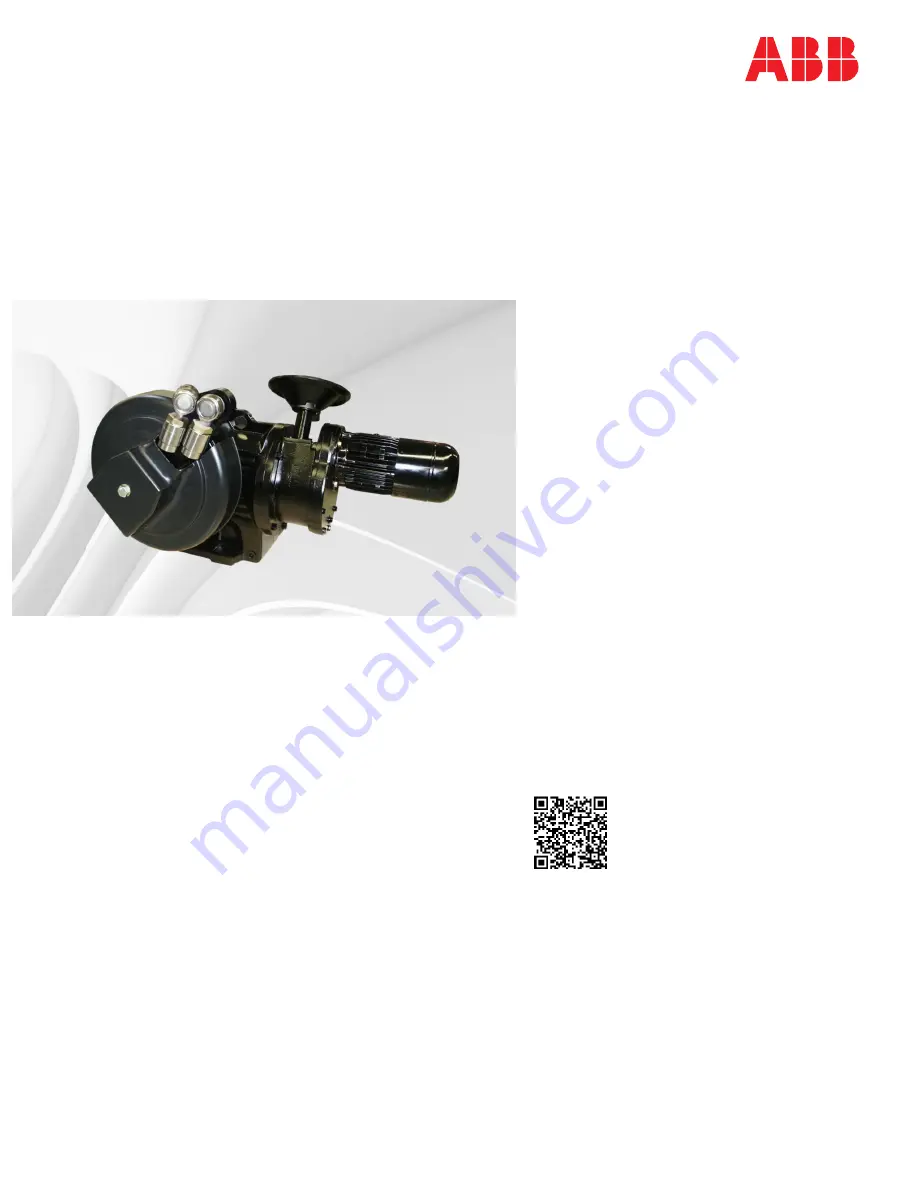
—
A B B M E A S U RE M E N T & A NA L Y T IC S | OPE R A TI NG I N ST R U CT I ON
RHD8000 / RHD16000 (Contrac)
Electrical rotary actuator
—
ABB Limited
Measurement & Analytics
Howard Road, St. Neots
Cambridgeshire, PE19 8EU
UK
Tel: +44 (0)870 600 6122
Fax: +44 (0)1480 213 339
Email: [email protected]
ABB Automation Products GmbH
Measurement & Analytics
Schillerstr. 72
32425 Minden
Germany
Tel: +49 571 830-0
Fax: +49 571 830-1806
abb.com/actuators
ABB Inc.
Measurement & Analytics
125 E. County Line Road
Warminster, PA 18974
USA
Tel: +1 215 674 6000
Fax: +1 215 674 7183
Electrical rotary actuator for the
operation of final control elements
OI
/RHD8
000/160
00-
EN
Re
v. D
08
.2
018
Or
iginal
instr
uc
tion
—
RHD8000
RHD16000
Introduction
Compact actuator for the operation of final control
elements with preferably 90° rotary movement such
as valve flaps, ball valves, etc.
The nominal torque is transferred through a lever
actuator. A special electronic unit controls the
actuator. The special electronic unit serves as the
interface between actuator and control system.
Additional Information
Additional documentation on RHD8000 / RHD16000
(Contrac) is available for download free of charge at
www.abb.com/actuators.
Alternatively simply scan this code:
—
We reserve the right to make technical changes or modify the contents of this document
without prior notice. With regard to purchase orders, the agreed particulars shall prevail.
ABB does not accept any responsibility whatsoever for potential errors or possible lack of
information in this document.
We reserve all rights in this document and in the subject matter and illustrations contained
therein. Any reproduction, disclosure to third parties or utilization of its contents – in
whole or in parts – is forbidden without prior written consent of ABB.
Copyright© 2018 ABB
All rights reserved 3KXE111015R4201