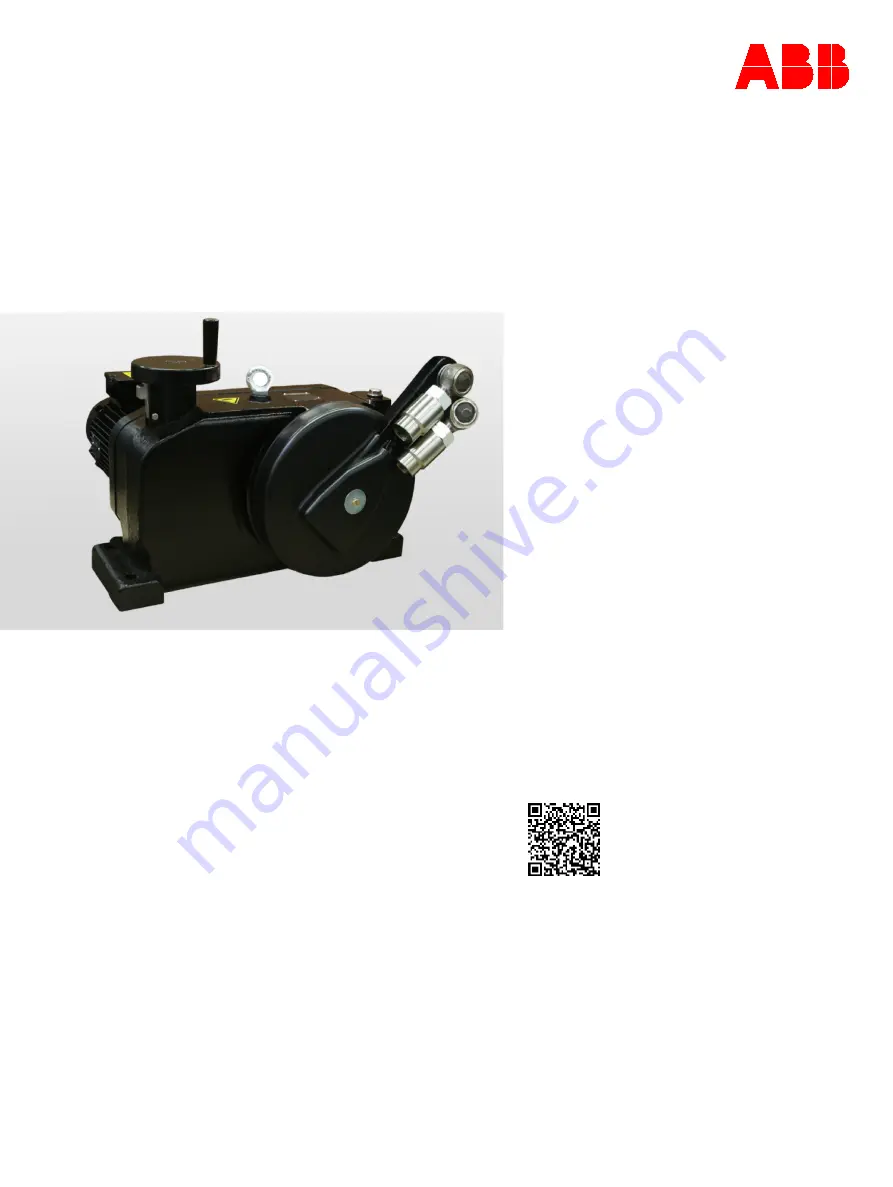
—
A B B M E A S U R E M E N T & A N A L Y T I C S | S ER V I C E I N ST R U C T I O N | S EI / R H D 25 0 / 4 00 0 - E N R E V . A
RHD250 to 4000 (Contrac)
Electrical rotary actuator
—
ABB Measurement & Analytics
For your local ABB contact, visit:
www.abb.com/contacts
For more product information, visit:
www.abb.com/actuators
Electrical rotary actuator for the
operation of final control elements.
SE
I/
R
H
D
25
0/
4000
-EN
Re
v.
A
0
5.
20
20
—
RHDE250
RHDE500
RHDE800
RHDE1250
RHDE2500
RHDE4000
Introduction
Compact actuator for the operation of final
control elements with preferably 90° rotary
movement such as valve flaps, ball valves, etc.
The nominal torque is transferred through a lever
actuator. A special electronic unit controls the
actuator. The special electronic unit serves as the
interface between actuator and control system.
Additional Information
Additional documentation on RHD250 to 4000
(Contrac) is available for download free of charge at
www.abb.com/actuators.
Alternatively simply scan this code:
—
We reserve the right to make technical changes or modify the contents of this document
without prior notice. With regard to purchase orders, the agreed particulars shall prevail.
ABB does not accept any responsibility whatsoever for potential errors or possible lack of
information in this document.
We reserve all rights in this document and in the subject matter and illustrations contained
therein. Any reproduction, disclosure to third parties or utilization of its contents – in whole
or in parts – is forbidden without prior written consent of ABB.
© ABB 2020
3KXE111019R4301