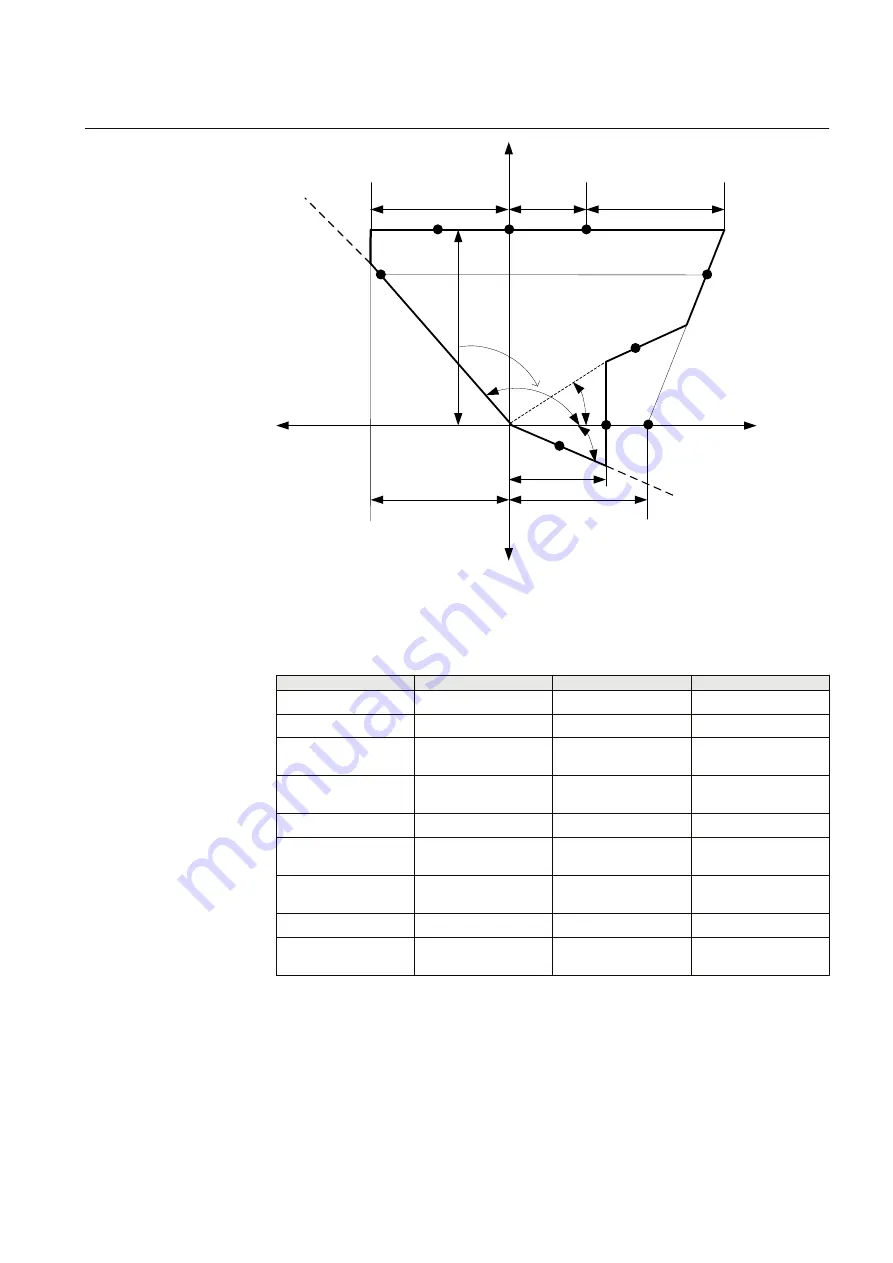
IEC15000436-1-en.vsdx
R
jX
RFPPFwZx
R1Fw
RFPPRvZx
X1Fw
RFPPFwZx
RFPPRvZx
RLd
80%
P1
P2
P3
P4
P5
P6
P7
P8
P9
ArgLd
ArgDir
ArgNegRes
( )
( )
IEC15000436 V1 EN-US
Figure 20:
Proposed test points for phase-to-phase loop of measuring
element
Table 22:
Test points for phase-to-phase loop measuring element
Test point
R
X
Comment
P1
0
X1Fw
P2
R1Fw
X1Fw
P3
(0.8 ∗
R1Fw) +
RFPPFwZx
0.8 ∗
X1Fw
P4
0.8 ∗
RFPPFwZx
0.8 ∗
RFPPFwZx ∗ tan
(
ArgLd)
P5
RLd
0
P6
RFPPFwZx
0
If
LEModeZx = Off and
OpLoadEnch = Off
P7
0.5 ∗
RLd
0.5 ∗
RLd ∗ tan
(
ArgDir)
P8
0.5 ∗
RFPPRvZx
X1Fw
P9
0.8 ∗
X1Fw ∗ tan
(
ArgNegRes)
0.8 ∗
X1Fw
1MRK 506 377-UEN C
Section 10
Testing functionality by secondary injection
Railway application RER670 2.2 IEC
97
Commissioning manual
Summary of Contents for RELION RER670
Page 1: ...RELION 670 SERIES Railway application RER670 Version 2 2 IEC Commissioning manual...
Page 2: ......
Page 26: ...20...
Page 54: ...48...
Page 58: ...52...
Page 62: ...56...
Page 80: ...74...
Page 188: ...182...
Page 194: ...188...
Page 204: ...198...
Page 214: ...208...
Page 215: ...209...