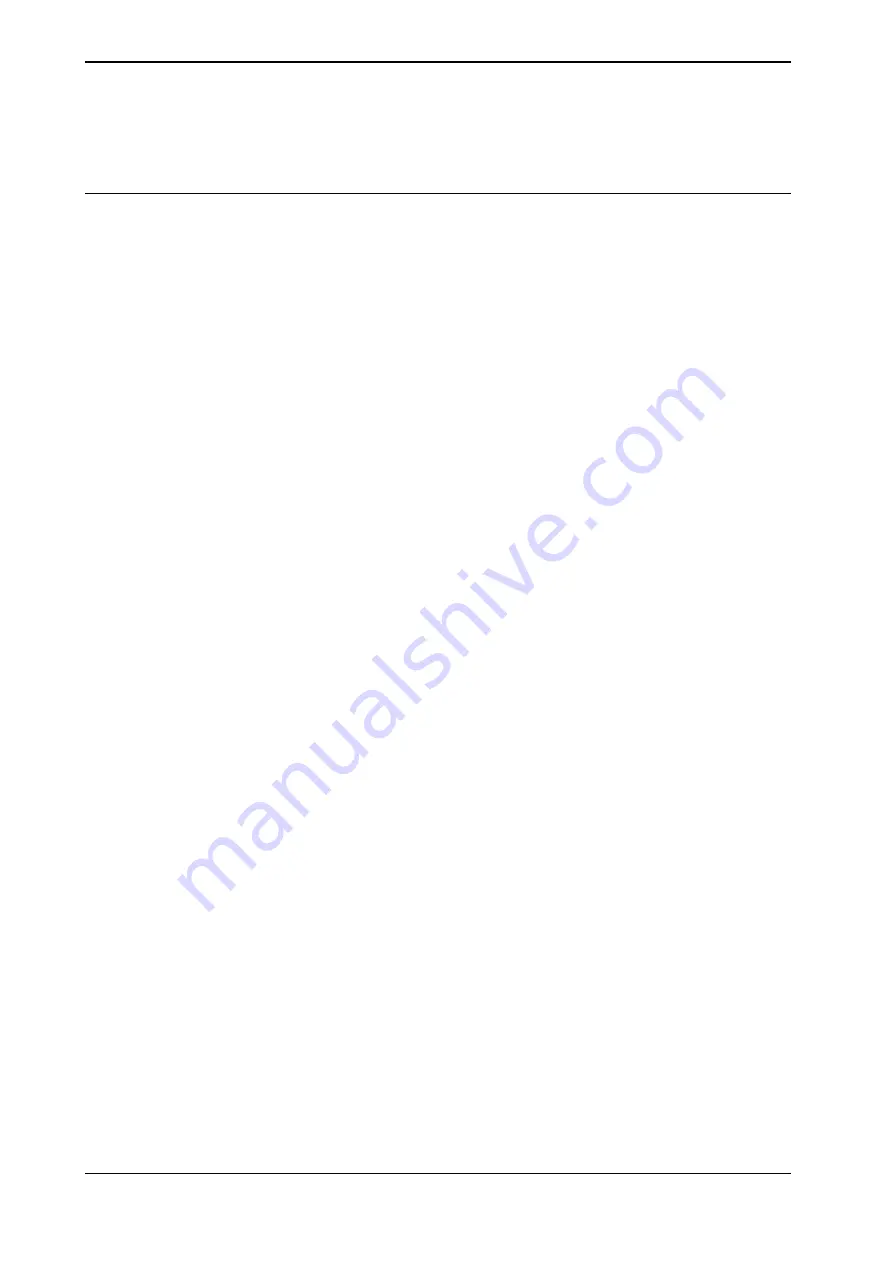
2.5.1 Installing RobotStudio
Instruction
For the detailed RobotStudio installation procedure, see
Operating manual - RobotStudio
,
3HAC032104-001
.
30
Application manual - PickMaster® Twin - PowerPac
3HAC064218-001 Revision: B
© Copyright 2021 ABB. All rights reserved.
2 Installation
2.5.1 Installing RobotStudio
Summary of Contents for PickMaster Twin - PowerPac
Page 1: ...ROBOTICS Application manual PickMaster Twin PowerPac ...
Page 8: ...This page is intentionally left blank ...
Page 12: ...This page is intentionally left blank ...
Page 16: ...This page is intentionally left blank ...
Page 420: ...This page is intentionally left blank ...
Page 444: ...This page is intentionally left blank ...
Page 446: ...This page is intentionally left blank ...
Page 448: ...This page is intentionally left blank ...
Page 452: ......
Page 453: ......