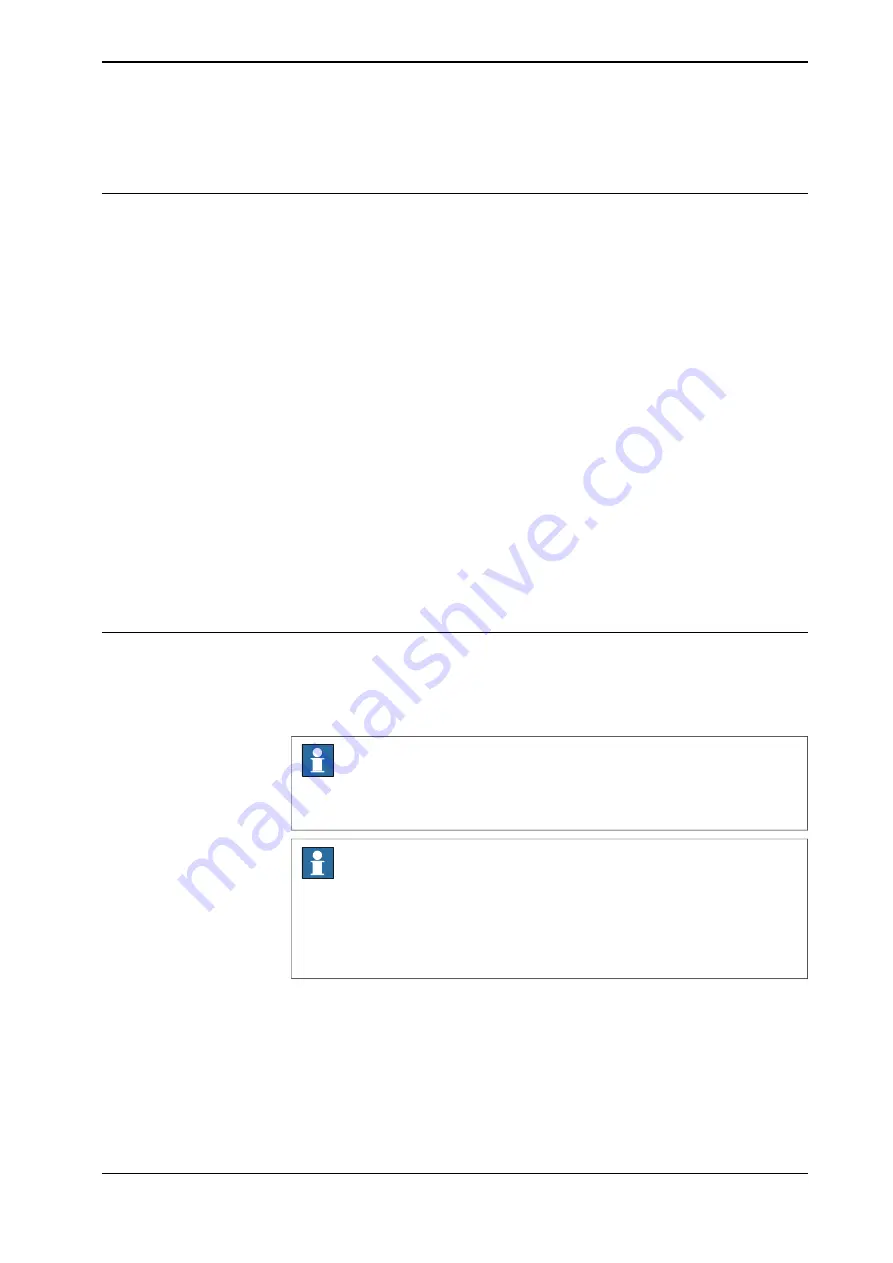
4.2.11 Calibration
Overview
This section describes how to calibrate the created solution.
The calibration in PickMaster PowerPac is a prerequisite for running the simulation.
The calibration is different with the calibration of the actual hardware (camera,
conveyor, IO sensor, etc.). Running this calibration does not mean that the actual
hardware calibration has been completed.
The calibration in PickMaster PowerPac is used to establish the relative relationship
between the conveyor base frame and the robot base coordinate system in the
virtual controller.
If a camera is used for a linear conveyor in the solution, the base frame of the
conveyor is directly below the camera after calibration (x is the forward direction).
If an IO sensor is used for a linear conveyor, the base frame of the conveyor is
located at the IO sensor. If a pre-defined point is not used for a linear conveyor,
the base frame of the conveyor overlaps the hot spot.
Indexed work area calibration is consistent with linear conveyor's calibration.
The calibrated base coordinate system of the circular conveyor belt is located at
the center of the conveyor belt, and the x-direction points directly below the camera
or along the IO sensor. If the circular conveyor uses a predefined point, the x
direction points to a predefined coordinate point.
Calibration
On the PickMaster PowerPac ribbon-tab, click
Simulation
.
Use this procedure to calibrate:
1 Click to select the recipe that need to calibrate.
Note
If the layout in the solution changes, such as changing the camera position
or robot position, redo the calibration.
Note
Each recipe in a solution needs to be individually calibrated.
If different recipes use different layouts, after running a simulation of recipe
A, you need to use another recipe B for simulation, then you must calibrate
recipe B first.
Continues on next page
Application manual - PickMaster® Twin - PowerPac
157
3HAC064218-001 Revision: B
© Copyright 2021 ABB. All rights reserved.
4 Working with PickMaster PowerPac
4.2.11 Calibration
Summary of Contents for PickMaster Twin - PowerPac
Page 1: ...ROBOTICS Application manual PickMaster Twin PowerPac ...
Page 8: ...This page is intentionally left blank ...
Page 12: ...This page is intentionally left blank ...
Page 16: ...This page is intentionally left blank ...
Page 420: ...This page is intentionally left blank ...
Page 444: ...This page is intentionally left blank ...
Page 446: ...This page is intentionally left blank ...
Page 448: ...This page is intentionally left blank ...
Page 452: ......
Page 453: ......