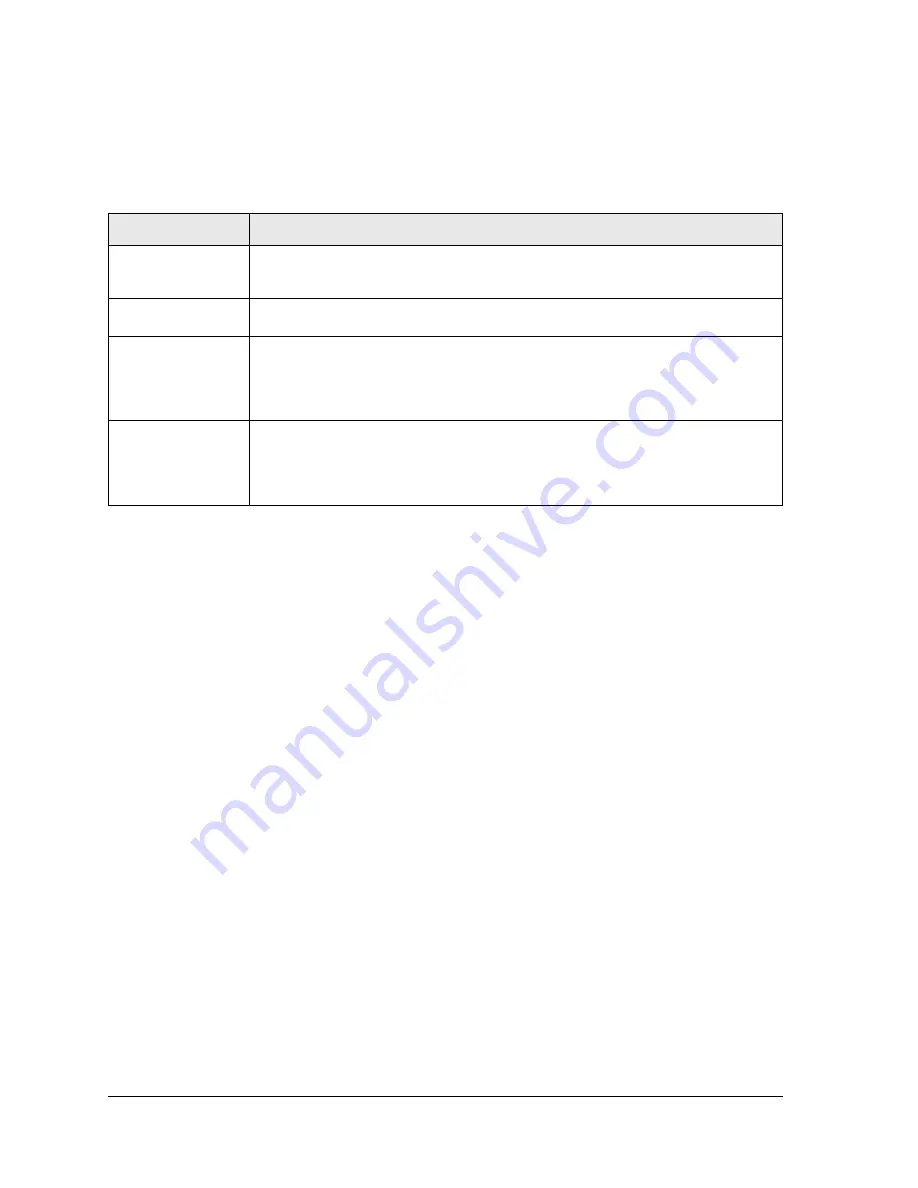
Page 6–8
2101510 Rev. AG
•
Plus = In addition to
•
Minus = Not Included or subtract from
6.3.2
Alarm Severity
Table 6–2 Alarm Severity
Type
Definition
General
Indicates that an alarm exists, but that it is not critical to the operation of the unit. Use
general when testing for some condition that may occur from time to time and want to
know when it happens.
Warning
Indicates that an alarm exists, typically is not critical but may indicate or provide
unexpected results.
Fault
Indicates that a malfunction exists that may affect the operation of the unit and most
likely will provide unexpected results. The fault will keep any affected streams from
having their data updated. However, a fault would not stop a scheduled or manually
initiated calibration from occurring, and, if the calibration corrects the alarm condition,
the alarm will be cleared.
System Fault
This typically indicates that a maintenance problem exists. Analysis processing will still
occur depending on the problem; however, results will not be updated for any stream
while this condition exists. Default system faults are already defined, and, unless the
user has a situation in which he/she wants to stop all stream data from being updated,
should not use this category of alarm.
6.3.3
Pressure Regulator 1 or 2 Alarm
If the pressure regulator 1 or pressure regulator 2 alarm is in fault status, the
following procedure will step the user through the troubleshooting process. On
occasion, these instructions may detour to other procedures, and, when complete,
the user should return to these procedures to continue.
6.3.3.1
Description
These alarms are indicative of low or restricted carrier pressure. The causes
range from an empty or low carrier bottle, restricted pressure or to a blockage
inside the GC module.
6.3.3.2
Instructions
1)
If the carrier bottle regulator includes an installed low pressure switch, investigate
if the low carrier gas bottle warning is also present; otherwise, continue to next
step.
If the low carrier gas bottle warning is present, replace the carrier gas
bottle; otherwise, continue to the next step.
2)
Verify the carrier gas bottle pressure is above 90 PSIG. If the pressure is below
90 PSIG, replace the carrier gas bottle. Otherwise, continue to the next step.
3)
Verify the carrier gas bottle pressure regulator set point is 90 PSIG. If not, correct
the set point to 90 PSIG. Otherwise, continue to the next step.
4)
Verify the column vent 1 (CV1) and 2 (CV2), sample vent (SV) and gauge port
vent (GPV) are open and unobstructed.
5)
Check the sampling system for leaks and tubing restrictions. Repair the leak or
restriction, if found. Otherwise, continue to the next step.
6)
Perform start-up diagnostics.
7)
If the carrier pressure regulator 1 and 2 tests both pass, continue to the next
step.