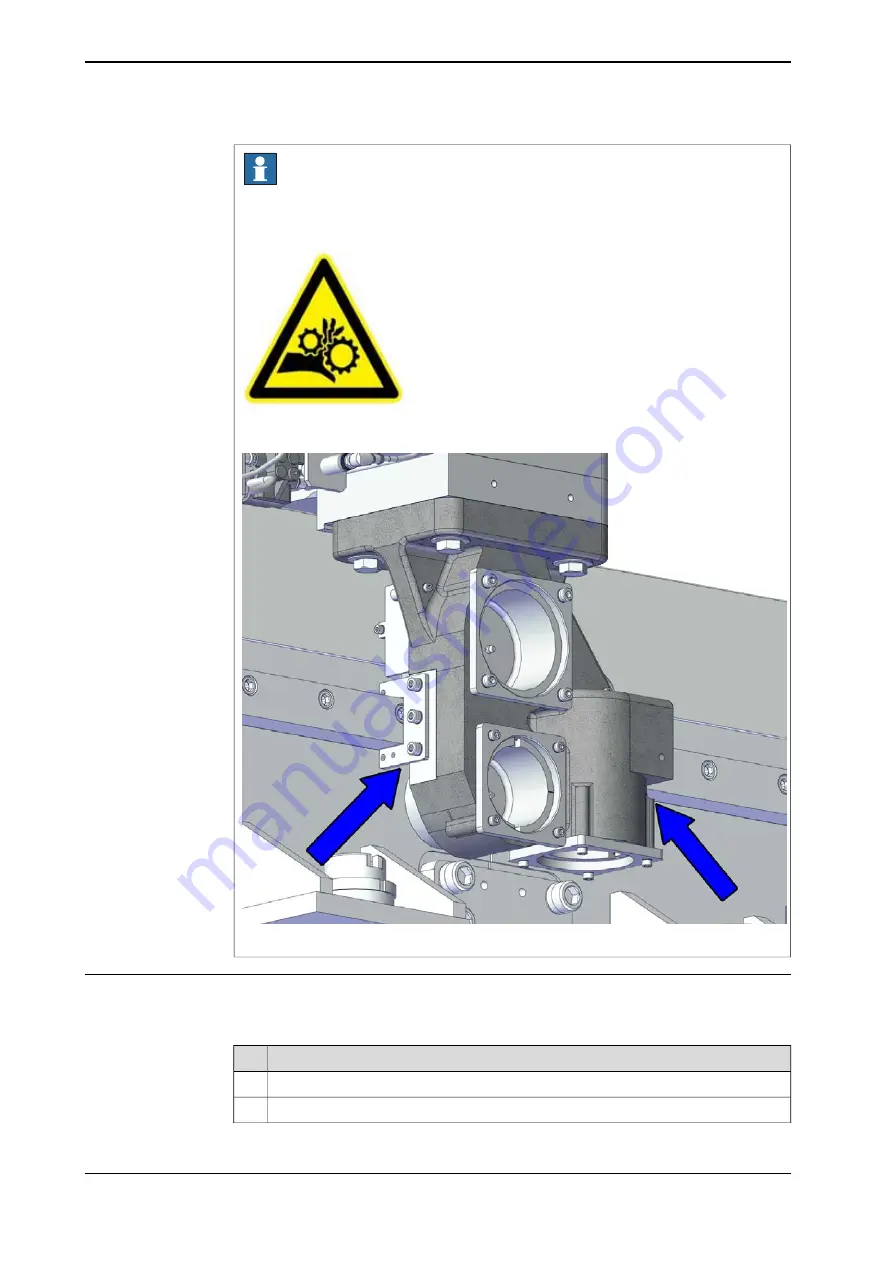
Note
Care should be taken when moving the track manually.
Users should remain clear of these locations when moving the track.
xx1800001868
xx2200000666
Release the brake (external 24V DC)
If there is no voltage to the motor, 24V DC can be connected direct to the SMB
box.
Action
Unplug the Motor power cable from the SMB box that runs to the IRT 710 motor.
1
Using pins, connect the +24VCC to the G pin (see figure).
2
Continues on next page
118
Product manual - IRT 710
3HKA00000186299-001 Revision: B
© Copyright 2023 ABB. All rights reserved.
3 Installation and commissioning
3.4.6 Moving the carriage manually
Continued
Summary of Contents for IRT 710
Page 1: ...ROBOTICS Product manual IRT 710 ...
Page 14: ...This page is intentionally left blank ...
Page 58: ...This page is intentionally left blank ...
Page 84: ...This page is intentionally left blank ...
Page 360: ...This page is intentionally left blank ...
Page 364: ...This page is intentionally left blank ...
Page 378: ...This page is intentionally left blank ...
Page 380: ...This page is intentionally left blank ...
Page 383: ......