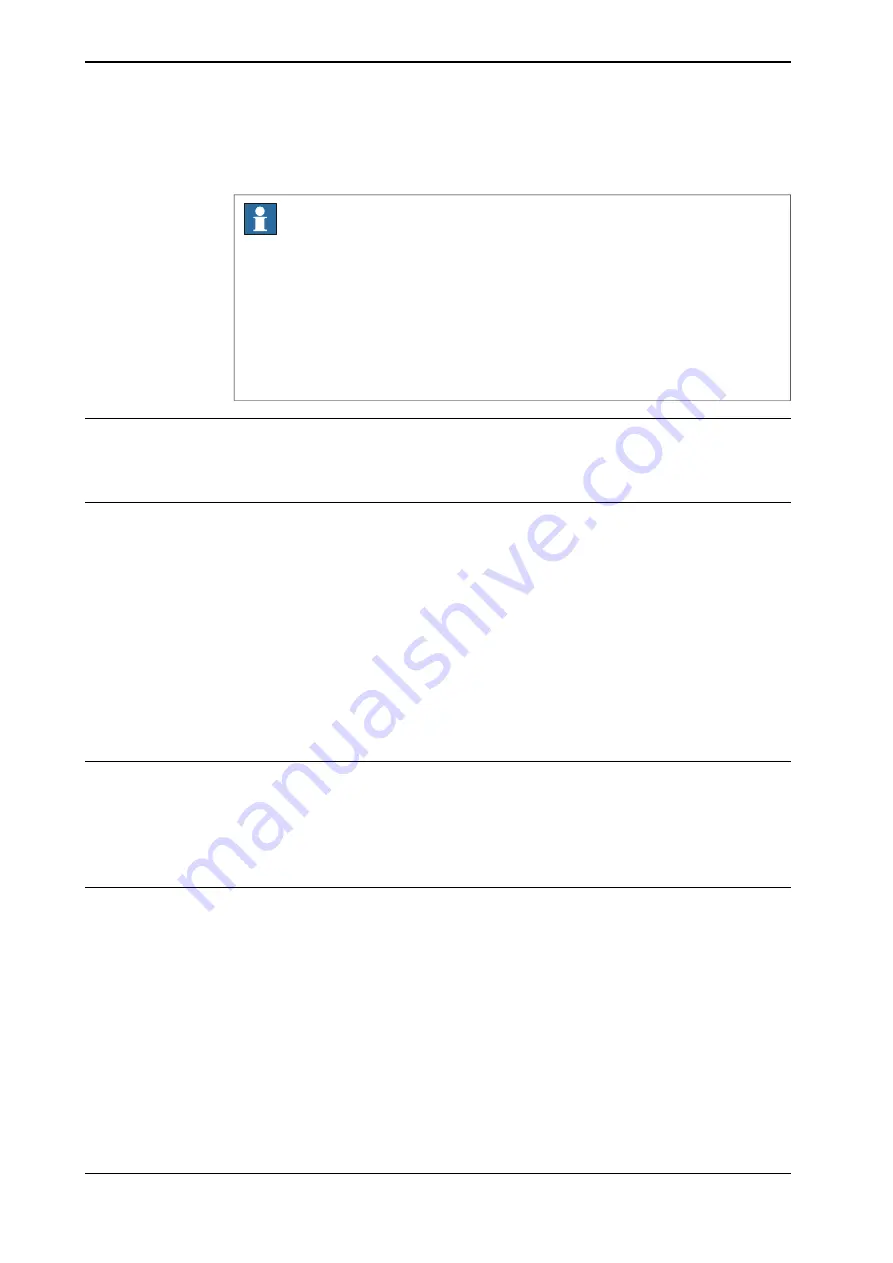
Note that the manual full speed mode is optional and therefore not available in all
robots.
Note
As per the updated standard, ISO 10218-1:2011
Robots and robotic devices –
Safety requirements for industrial robots – Part 1 Robots
, the following adaptations
are made to the manual full speed mode.
•
Resetting the speed to 250 mm/s every time the three-position enabling
device is re-initiated by placing the switch in the center-enabled position
after either having been released or fully compressed.
•
Editing RAPID programs and jogging the manipulator are disabled.
Bypassed safeguard mechanisms
Automatic mode
safeguarded stop (AS) mechanisms are bypassed while operating
in manual mode.
The three-position enabling device
In
manual mode
the motors of the manipulator are activated by the three-position
enabling device on the FlexPendant. This way the manipulator can only move as
long as the device is pressed.
In order to run a program in manual full speed mode it is necessary, for safety
reasons, to keep pressing both the three-position enabling device and the Start
button. This hold-to-run function also applies when stepping through a program
in manual full speed mode.
The three-position enabling device is designed so that its push-button must be
pressed just half-way to activate the motors of the manipulator. Both in its all-out
and full-in positions the manipulator will not move.
The hold-to-run function
The hold-to-run function allows stepping or running a program in manual full speed
mode. Note that jogging does not require the hold-to-run function, regardless of
operating mode. The hold-to-run function can also be activated for manual reduced
speed mode.
Tasks normally performed in manual reduced speed mode
The following tasks are normally performed in manual reduced speed mode.
•
Jogging the manipulator back on its path when returning to operation after
an emergency stop
•
Correcting the value of I/O signals after error conditions
•
Creating and editing RAPID programs
•
Starting, stepping, and stopping program execution, for example while testing
a program
•
Tuning programmed positions
Continues on next page
30
Operating manual - IRC5 with FlexPendant
3HAC050941-001 Revision: G
© Copyright 2018 ABB. All rights reserved.
1 Safety
1.4.4 About the manual mode
Continued
Summary of Contents for IRC5 with FlexPendant
Page 1: ...ROBOTICS Operating manual IRC5 with FlexPendant ...
Page 14: ...This page is intentionally left blank ...
Page 120: ...This page is intentionally left blank ...
Page 146: ...This page is intentionally left blank ...
Page 240: ...This page is intentionally left blank ...
Page 286: ...This page is intentionally left blank ...
Page 294: ...This page is intentionally left blank ...
Page 298: ...This page is intentionally left blank ...
Page 304: ......
Page 305: ......