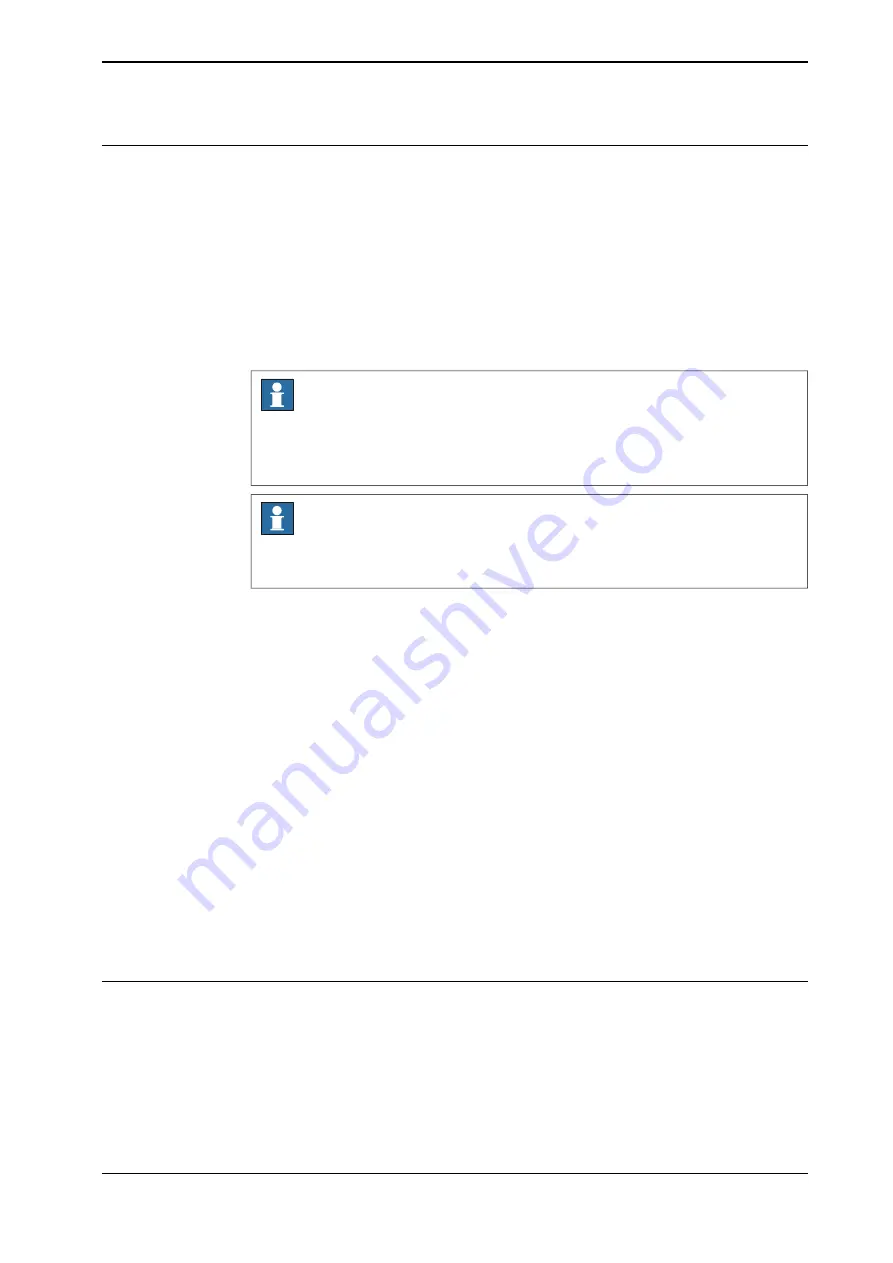
Routines in the calibration procedure
The following routines are available in the Axis Calibration procedure, given at the
beginning of the procedure on the FlexPendant.
Fine calibration routine
Choose this routine to calibrate the robot when there are no tools, process cabling
or equipment fitted to the robot.
Reference calibration routine
Choose this routine to create reference values and to calibrate the robot when the
robot is dressed with tools, process cabling or other equipment.
Note
When calibrating the robot with the reference calibration routine, the robot must
be dressed with the same tools, process cabling and any other equipment as
when the reference values were created.
Note
When using reference calibration with some tools, typically large or flexible tools,
oscillations in the robot can cause issues leading to failure of the calibration.
If calibrating the robot with reference calibration there must be reference values
created before repair is made to the robot, if values are not already available.
Creating new values requires possibility to move the robot. The reference values
contain positions of all axes, torque of axes and technical data about the tool
installed. A benefit with reference calibration is that the current state of the robot
is stored and not the state when the robot left the ABB factory. The reference value
will be named according to tool name, date etc.
Follow the instructions given in the reference calibration routine on the FlexPendant
to create reference values.
When reference calibration is performed, the robot is restored to the status given
by the reference values.
Update revolution counters
Choose this routine to make a rough calibration of each manipulator axis by
updating the revolution counter for each axis, using the FlexPendant.
Validation
In the mentioned routines, it is also possible to validate the calibration data.
Position of robot axes
The robot axes should be positioned close to 0 degrees before commencing the
calibration program. The axis chosen for calibration is then automatically run by
the calibration program to its exact calibration position during the calibration
procedure.
It is possible to position some of the other axes in positions different from 0 degrees.
Information about which axes are allowed to be jogged is given on the FlexPendant.
Continues on next page
Product manual - IRB 6710
595
3HAC085695-001 Revision: A
© Copyright 2023 ABB. All rights reserved.
6 Calibration
6.4.1 Description of Axis Calibration
Continued
Summary of Contents for IRB 6710
Page 1: ...ROBOTICS Product manual IRB 6710 ...
Page 8: ...This page is intentionally left blank ...
Page 14: ...This page is intentionally left blank ...
Page 36: ...This page is intentionally left blank ...
Page 584: ...This page is intentionally left blank ...
Page 614: ...This page is intentionally left blank ...
Page 634: ...This page is intentionally left blank ...
Page 639: ......