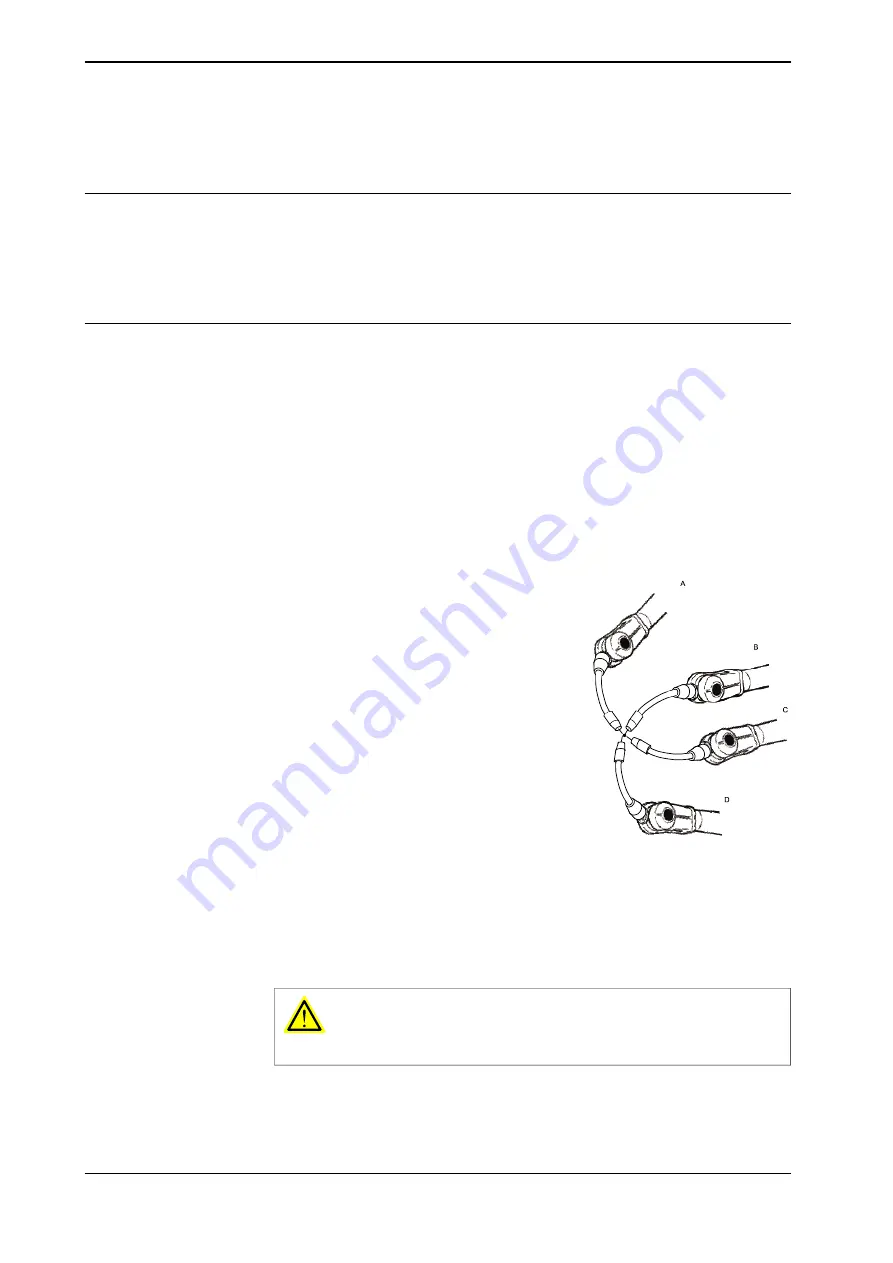
5.5 Calibrating with Wrist Optimization method
When to run Wrist Optimization
Wrist Optimization
routine is run to improve TCP reorientation performance.
Calibrating the robot with standard calibration method overwrites the optimized
positions of axes 4, 5. Re-run the
Wrist Optimization
routine after standard
calibration to re-achieve the optimized positions of the wrist axes.
Overview of the calibration procedure on the FlexPendant
The actual instructions of how to perform the calibration procedure and what to
do at each step is given on the FlexPendant. You will be guided through the
calibration procedure, step by step.
Use the following list to learn about the calibration procedure before running the
RobotWare program on the FlexPendant. It gives you a brief overview of the
calibration procedure sequence.
After the calibration method has been called for on the FlexPendant, the following
sequence will be run.
1 Choose calibration routine Wrist Optimization.
2 Modify targets for 4-point tool frame definition, in Wrist Optimization routine.
en0400000906
a
Jog the robot to an appropriate position,
A, for the first approach point.
Use small increments to accurately posi-
tion the tool tip as close to the reference
point as possible.
b Tap
Modify Position
to define the point.
c
Repeat for each approach point to be
defined, positions B, C, and D.
Jog away from the fixed world point to
achieve the best result. Just changing the
tool orientation will not give as good a
result.
3 Improved calibration data to the wrist axes is identified and presented.
4 Optimized positions for the wrist axes are presented.
5 The robot moves to the optimized positions for the wrist axes and
automatically overwrites previous calibration data.
WARNING
Robot moves automatically when pressing
Calibrate
.
6 Wrist optimization is finished.
7 Redefine / verify TCP for all tools.
696
Product manual - IRB 6700Inv
3HAC058254-001 Revision: L
© Copyright 2017 - 2020 ABB. All rights reserved.
5 Calibration
5.5 Calibrating with Wrist Optimization method
Summary of Contents for IRB 6700I
Page 1: ...ROBOTICS Product manual IRB 6700Inv ...
Page 16: ...This page is intentionally left blank ...
Page 40: ...This page is intentionally left blank ...
Page 182: ...This page is intentionally left blank ...
Page 672: ...This page is intentionally left blank ...
Page 704: ...This page is intentionally left blank ...
Page 720: ...This page is intentionally left blank ...
Page 722: ...This page is intentionally left blank ...
Page 729: ......