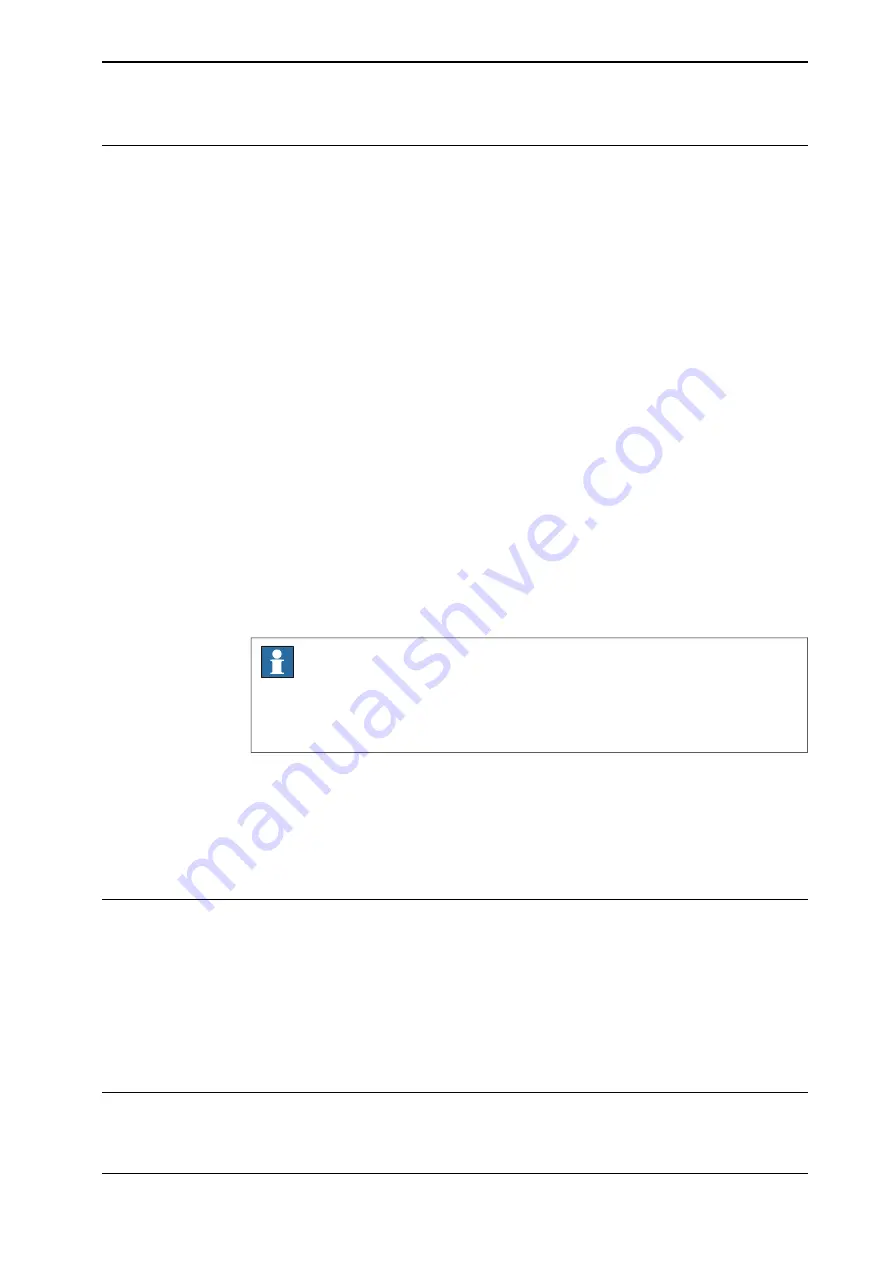
Routines in the calibration procedure
The following routines are available in the Axis Calibration procedure, given at the
beginning of the procedure on the FlexPendant.
Fine calibration routine
Choose this routine to calibrate the robot when there are no tools, process cabling
or equipment fitted to the robot.
Reference calibration routine
Choose this routine to create reference values and to calibrate the robot when the
robot is dressed with tools, process cabling or other equipment.
Also choose this routine if the robot is suspended.
If calibrating the robot with reference calibration there must be reference values
created before repair is made to the robot, if values are not already available.
Creating new values requires possibility to move the robot. The reference values
contain positions of all axes, torque of axes and technical data about the tool
installed. A benefit with reference calibration is that the current state of the robot
is stored and not the state when the robot left the ABB factory. The reference value
will be named according to tool name, date etc.
Follow the instructions given in the reference calibration routine on the FlexPendant
to create reference values.
When reference calibration is performed, the robot is restored to the status given
by the reference values.
Note
When calibrating the robot with the reference calibration routine, the robot must
be dressed with the same tools, process cabling and any other equipment as
when the reference values were created.
Update revolution counters
Choose this routine to make a rough calibration of each manipulator axis by
updating the revolution counter for each axis, using the FlexPendant.
Validation
In the mentioned routines, it is also possible to validate the calibration data.
Position of robot axes
The axis chosen for calibration is automatically run by the calibration program to
its calibration position during the calibration procedure.
In order for the axis to be able to be moved to calibration position, or in order for
getting proper access to the calibration bushing, other axes might need to be
jogged to positions different from 0 degrees. Information about which axes are
allowed to be jogged will be given on the FlexPendant. These axes are marked
with
Unrestricted
in the FlexPendant window.
How to calibrate a suspended robot
The IRB 4600 Foundry Prime is calibrated floor standing in factory, prior to shipping.
Continues on next page
Product manual - IRB 4600 Foundry Prime
365
3HAC040585-001 Revision: M
© Copyright 2013-2018 ABB. All rights reserved.
5 Calibration
5.4.1 Description of Axis Calibration
Continued
Summary of Contents for IRB 4600 Foundry Prime
Page 1: ...ROBOTICS Product manual IRB 4600 Foundry Prime ...
Page 106: ...This page is intentionally left blank ...
Page 194: ...This page is intentionally left blank ...
Page 398: ...This page is intentionally left blank ...
Page 400: ...This page is intentionally left blank ...
Page 406: ......
Page 407: ......