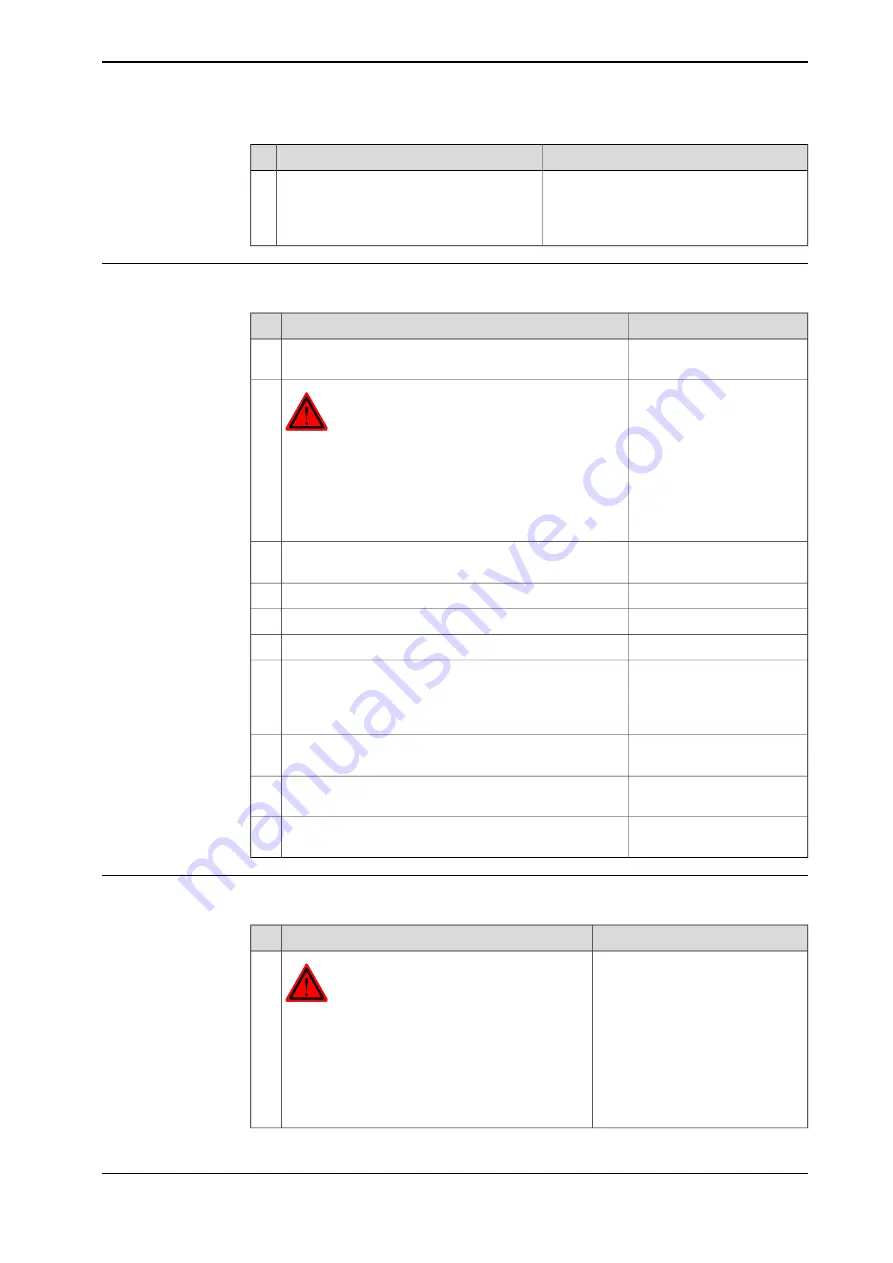
Note
Action
If the robot is to be calibrated with fine
calibration:
Remove all external cable packages
(DressPack) and tools from the robot.
Removing the motor axis 1
Use this procedure to remove the motor, axis 1.
Note
Action
Decide which calibration routine to use, and take actions
accordingly prior to beginning the repair procedure.
1
DANGER
Turn off all:
•
electric power supply
•
hydraulic pressure supply
•
air pressure supply
to the robot, before entering the robot working area.
2
Shown in the figure
.
Remove the
cover, frame
.
3
Disconnect the connectors for the motor.
4
Loosen the
connector plate
from the frame.
5
Pull out the motor cabling carefully.
6
Connect to connector
R3.MP1:
•
+: pin 7
•
-: pin 8
In order to release the brakes, connect the 24 VDC power
supply to the motor.
7
Shown in the figure
.
Unscrew the
attachment screws
securing the motor.
8
Remove the motor by gently lifting it straight up, making
sure the motor pinion is not damaged against the gear.
9
Disconnect the brake release voltage from the motor
connector.
10
Refitting the motor axis 1
Use this procedure to refit the motor, axis 1.
Note
Action
DANGER
Turn off all:
•
electric power supply
•
hydraulic pressure supply
•
air pressure supply
to the robot, before entering the robot working
area.
1
Continues on next page
Product manual - IRB 1600/1660
259
3HAC026660-001 Revision: W
© Copyright 2006-2018 ABB. All rights reserved.
4 Repair
4.6.1 Replacement of motor, axis 1
Continued
Summary of Contents for IRB 1660
Page 1: ...ROBOTICS Product manual IRB 1600 1660 ...
Page 8: ...This page is intentionally left blank ...
Page 18: ...This page is intentionally left blank ...
Page 48: ...This page is intentionally left blank ...
Page 152: ...This page is intentionally left blank ...
Page 336: ...This page is intentionally left blank ...
Page 372: ...This page is intentionally left blank ...
Page 388: ...This page is intentionally left blank ...
Page 396: ......
Page 397: ......