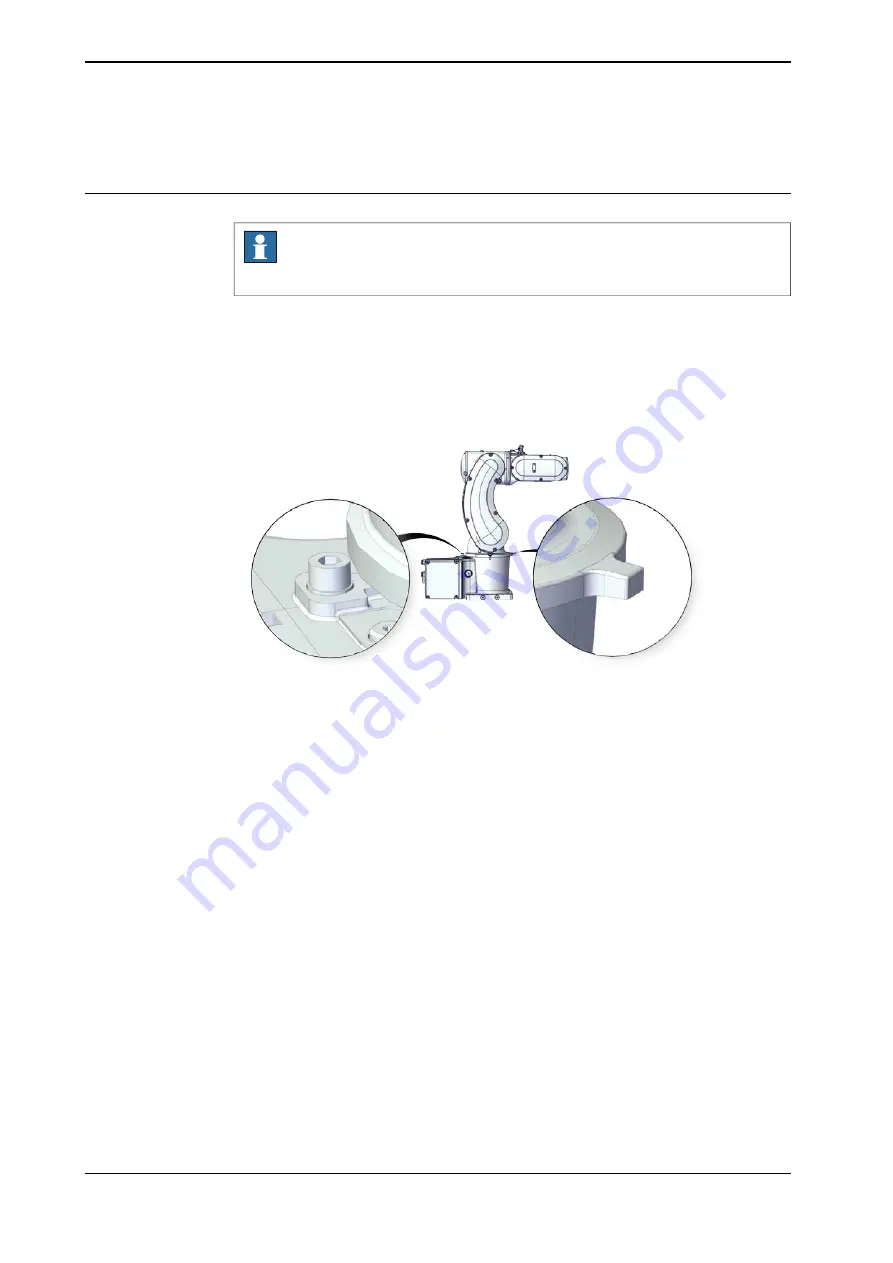
4.4.4 Inspecting mechanical stops
Location of mechanical stops
Note
Only axis-1 and axis-3 are visible for inspection and available for replacement.
Axis 1
xx2200000198
Continues on next page
92
Product manual - IRB 1010
3HAC081964-001 Revision: B
© Copyright 2022 ABB. All rights reserved.
4 Maintenance
4.4.4 Inspecting mechanical stops
Summary of Contents for IRB 1010
Page 1: ...ROBOTICS Product manual IRB 1010 ...
Page 8: ...This page is intentionally left blank ...
Page 14: ...This page is intentionally left blank ...
Page 36: ...This page is intentionally left blank ...
Page 46: ...This page is intentionally left blank ...
Page 80: ...This page is intentionally left blank ...
Page 306: ...This page is intentionally left blank ...
Page 312: ...This page is intentionally left blank ...
Page 326: ...This page is intentionally left blank ...
Page 328: ...This page is intentionally left blank ...
Page 332: ......
Page 333: ......