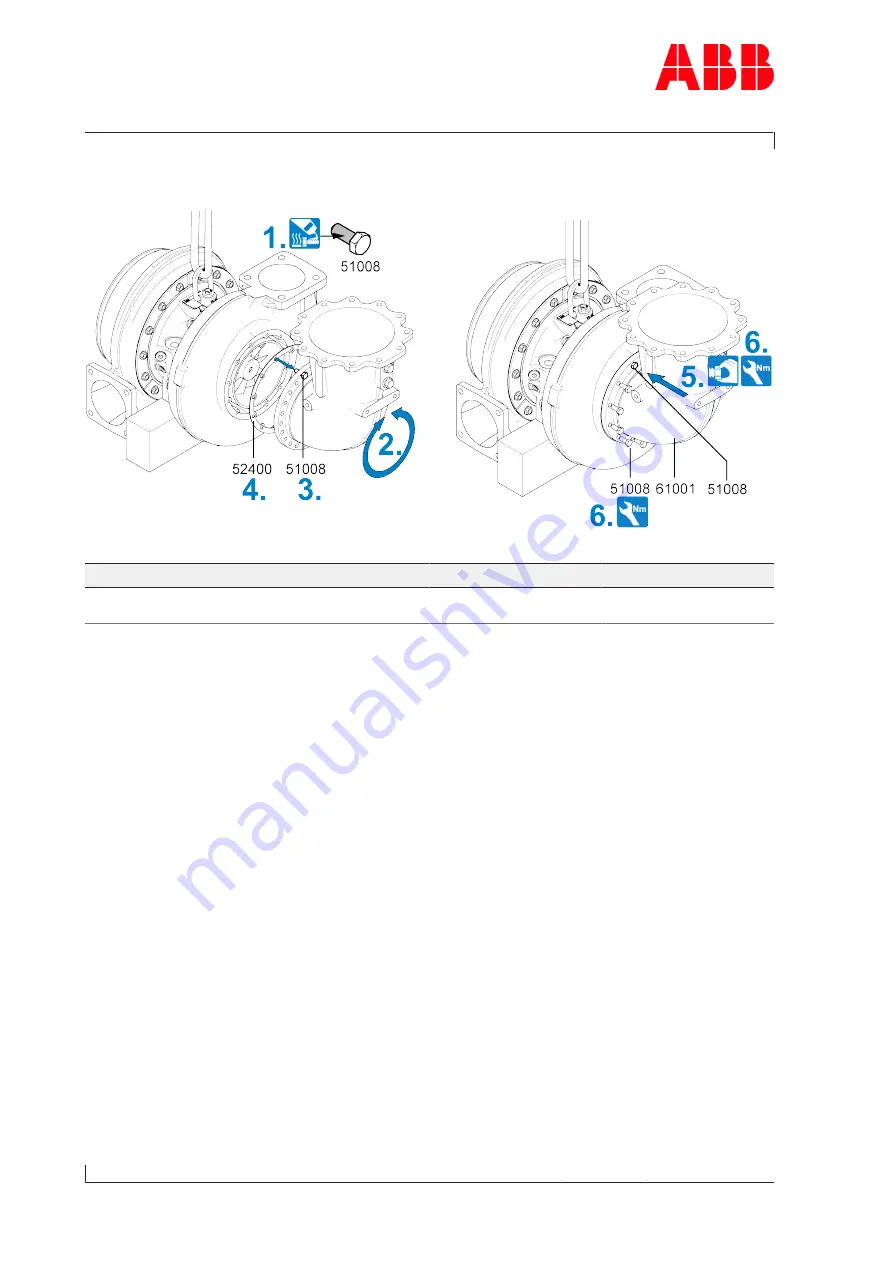
Operation Manual / 4 Product description / TPS44-H.. - TPS52-H..
9 Dismantling and fitting / 9.16 Installing the gas outlet casing
© Copyright 2017 ABB. All rights reserved.
HZTL4037_EN
Revision E
July 2017
9.16
Installing the gas outlet casing
Fig. 36: Fitting the gas outlet casing
Part number
TPS44
TPS48
TPS52
51008
M8
25 Nm
M8
25 Nm
M10
50 Nm
Table 39: Tightening torque (51101)
1. Coat the threads of the hexagon-head screws or studs (51008) with high-temperature
grease.
2. Align the casing position of the gas outlet casing (61001) to the marking.
3. Fit two hexagon-head screws (51008) in the upper area of the gas outlet casing.
4. Position the gasket (52400) on the threads of the hexagon-head screws (51008).
5. Install the gas outlet casing (61001) on the turbine casing with the two screws.
6. Fit the remaining screws (51008), then tighten all the screws.
Page
68
/
77