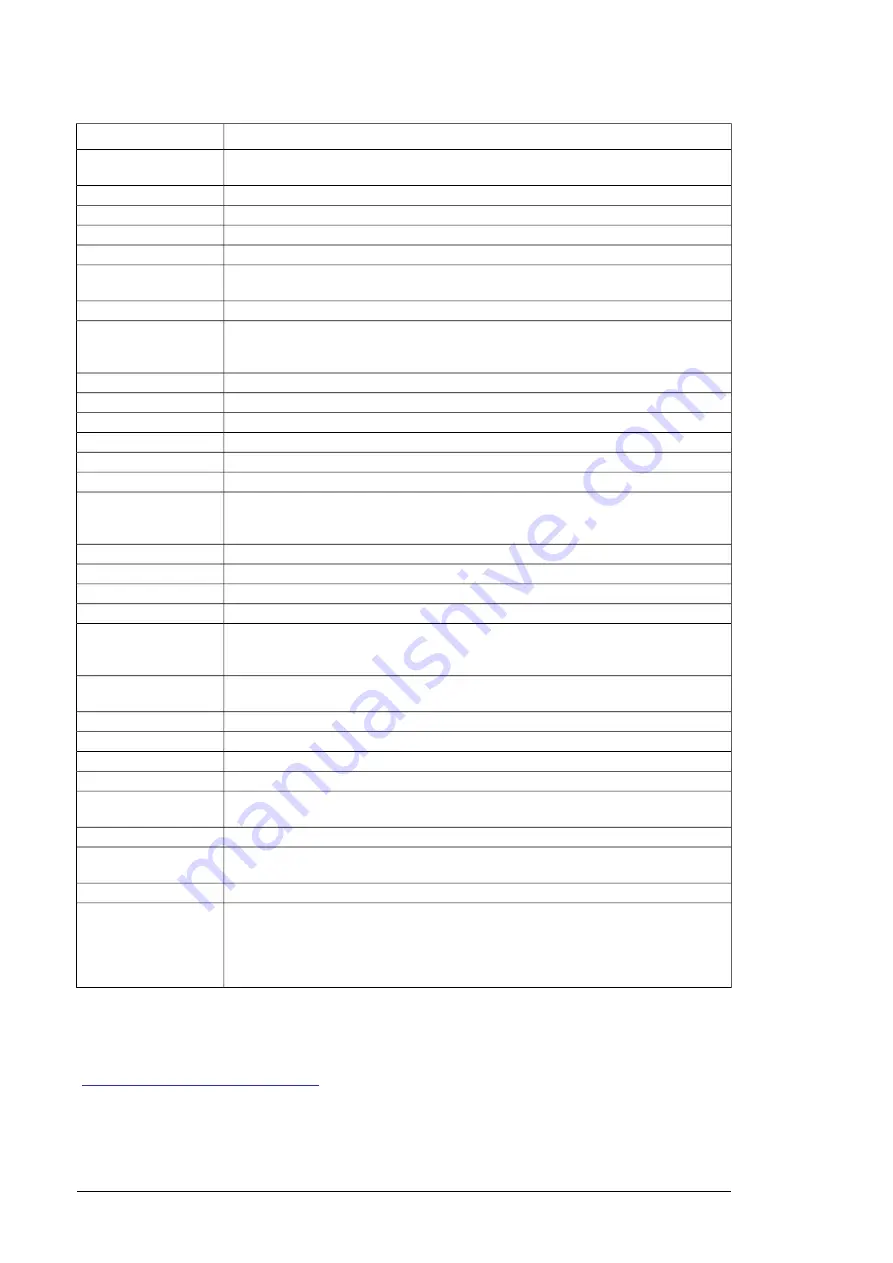
Description
Term
Discovery Control Protocol. A protocol that allows the master controller to find every
PROFINET IO device on a subnet.
DCP
Digital input
DI
Frequency converter for controlling AC motors
Drive
Electromagnetic compatibility
EMC
Emergency stop
E-stop
Function that is initiated when a fault within the safety component is detected by the
component's diagnostic function. (62061-3.2.18, modified)
Fault reaction function
Failure in time: 1E-9 hours (IEC 61508)
FIT
General Station Description file, an ASCII-format device description file in a specified
form. Each different slave type on the PROFINET IO network needs to have its own
GSD file. GSD files in PROFINET IO are written in GSDML.
GSD file
Insulated gate bipolar transistor
IGBT
Least significant bit
LSB
Media Access Control address
MAC address
Media redundancy manager
MRM
Media redundancy protocol
MRP
Most significant bit
MSB
Mean time to dangerous failure: (Total number of life units) / (Number of dangerous,
undetected failures) during a particular measurement interval under stated conditions
(EN ISO 13849-1)
MTTF
D
Average probability of dangerous failure on demand (IEC 61508)
PFD
avg
Average frequency of dangerous failures per hour (IEC 61508)
PFH
Performance level. Levels a...e correspond to SIL (EN ISO 13849-1)
PL
Programmable logic controller
PLC
Adjustable speed electrical power drive system suitable for use in safety-related ap-
plications
Power drive systems
(Safety-related), PDS
(SR)
Adaptation of a communication protocol for a certain application field (for example
drives)
Profile
PD, Process data
PZD
Systematic capability (IEC 61508)
SC
Safe failure fraction (%) (IEC 61508)
SFF
Safety integrity level (1...3) (IEC 61508)
SIL
Maximum SIL (level 1...3) that can be claimed for a safety function or subsystem
(IEC/EN 62061)
SILCL
Safe stop 1 (IEC/EN 61800-5-2)
SS1
16-bit or 32-bit word from a controlled device to the controller with bit-coded status
signals
Status word
Safe torque off (IEC/EN 61800-5-2)
STO
Proof test interval. Defines the probabilistic failure rate (PFH or PFD) for the safety
function or subsystem. Performing a proof test at a maximum interval of T1 is required
to keep the SIL capability valid. The same interval must be followed to keep the PL
capability (EN ISO 13849) valid. Note that any T1 values given cannot be regarded
as a guarantee or warranty.
T1
Certificates
The valid TÜV and PROFIsafe certificates can be found at the ABB library
(
18 Introduction to the manual
Summary of Contents for FSPS-21
Page 1: ... OPTIONS FOR ABB DRIVES FSPS 21 safety functions fieldbus module User s manual ...
Page 2: ......
Page 4: ......
Page 11: ...Further information Table of contents 11 ...
Page 12: ...12 ...
Page 26: ...26 ...
Page 38: ...38 ...
Page 42: ...42 ...
Page 46: ...46 ...
Page 72: ...Switch or router ABB drive ABB drive ABB drive PLC Safety PLC 72 PROFINET IO Start up ...
Page 86: ...86 ...
Page 144: ...19 In ABB_Drive FB add blocks DPRD_DAT and DPWR_DAT 20 Insert values to blocks 144 PROFIsafe ...
Page 147: ...26 In device configuration right click FSPS icon and select Assign device name PROFIsafe 147 ...
Page 155: ...Select Addresses tab to see the correct IO addresses PROFIsafe 155 ...
Page 169: ...6 To check the Device number of the FSPS 21 module select the General tab PROFIsafe 169 ...
Page 178: ... starting the system does not cause any danger 178 Start up ...
Page 186: ...186 ...
Page 192: ...192 ...
Page 200: ...200 ...
Page 208: ...208 ...
Page 212: ......