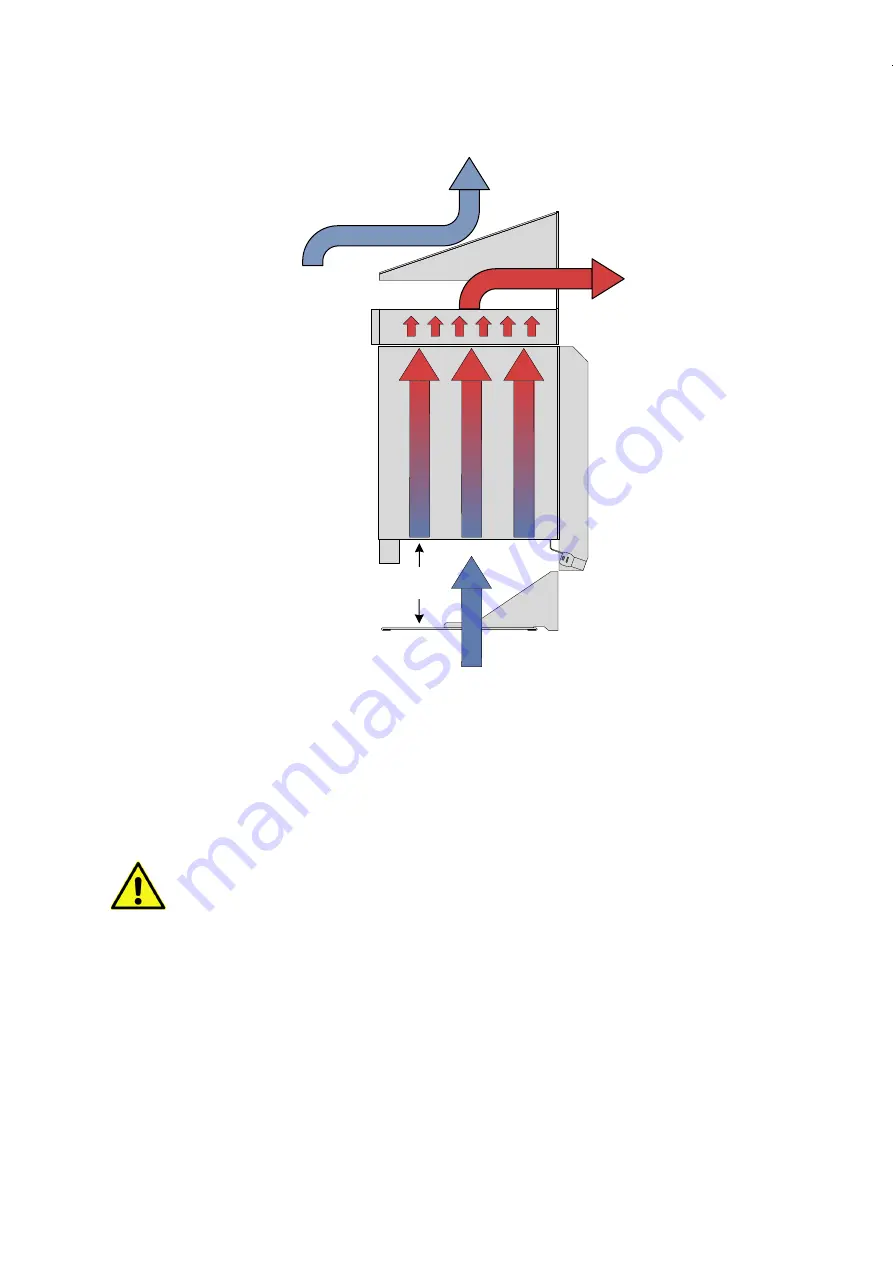
P R E P A R I N G F O R I N S T A L L A T I O N
18
FOX615
Installation
Figure 3:
Evacuation of heated air to the front (recommended for 19-
inch installation at the top of a cabinet)
The FAMO1 is a fan unit designed for the FOX615 and installed between the
subrack and the heat deflection shield R7AI on top.
With passive cooling operation of the FOX subrack the FAMO1 is replaced
by the alarm unit FAMO1-F. If no external alarm interfaces are required the
alarm unit can be omitted. Also in this case the heat deflection shield R7AI
should be placed with a 1 HU distance above the FOX615 subrack.
CAUTION
Attention to temperature range!
Attention to temperature range. Risk of equipment damage!
It is essential to preserve the system specifications and to prevent the sys-
tem from overheating.
→
The site of installation must provide an ambient temperature within the
specified range at any time.
For illustration of the implementation of this basic arrangement of the FOX
subrack, FAMO1 or FAMO1-F
and heat deflection shield R7AI in the rack,
.
Rear
Front
Cable tray
Subrack with units
Cold air
Heated air
Cold air
2
H
U
Heat deflection shield R7AI
FAMO1 or FAMO1-F
Summary of Contents for FOX615
Page 1: ...ABB Power Systems FOX615 Installation User Manual ...
Page 6: ...4 FOX615 Installation ...
Page 10: ...8 FOX615 Installation ...
Page 96: ...A N N E X 94 FOX615 Installation ...
Page 97: ......