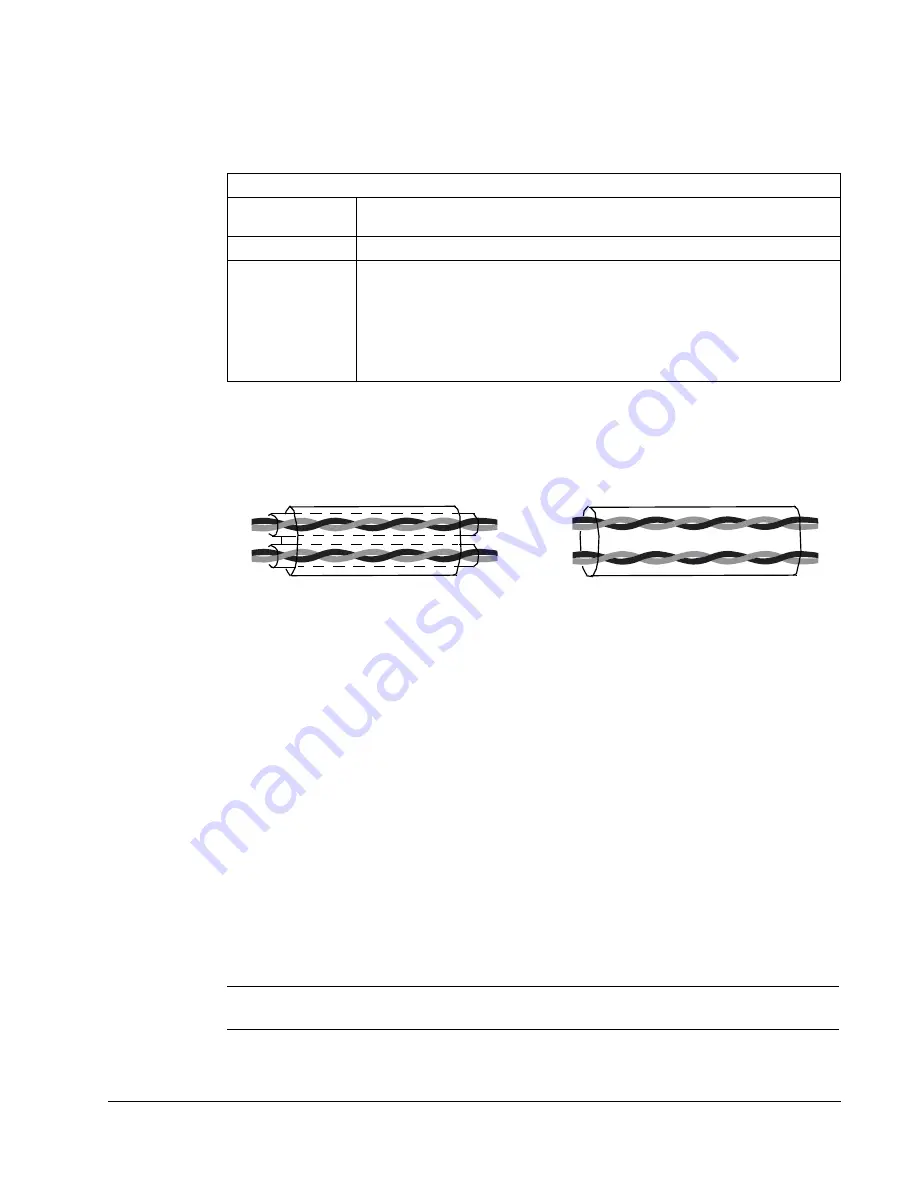
ACH550-UH User’s Manual
237
Technical Data
Control Connections
Control Connection Specifications
Control Cables
General Recommendations
Use multi-core cables with a braided copper wire screen, temperature rated at 60 °C
(140 °F) or above:
At the drive end, twist the screen together into a bundle not longer than five times its
width and connected to terminal X1-1 (for digital and analog I/O cables) or to either
X1-28 or X1-32 (for RS485 cables).
Route control cables to minimize radiation to the cable:
•
Route as far away as possible from the input power and motor cables (at least
20 cm (8 in)).
•
Where control cables must cross power cables make sure they are at an angle as
near 90° as possible.
•
Stay at least 20 cm (8 in) from the sides of the drive.
Use care in mixing signal types on the same cable:
•
Do not mix analog and digital input signals on the same cable.
•
Run relay-controlled signals as twisted pairs (especially if voltage > 48 V). Relay-
controlled signals using less than 48 V can be run in the same cables as digital
input signals.
Note!
Never mix 24 VDC and 115/230 VAC signals in the same cable.
Control Connection Specifications
Analog Inputs
and Outputs
See table heading "Drive Control Terminal Description" on page 239.
Digital Inputs
Digital input impedance 1.5 k
Ω
. Maximum voltage for digital inputs is 30 V.
Relays
(Digital Outputs)
• Max. contact voltage: 30 V DC, 250 V AC
• Max. contact current / power: 6 A, 30 V DC; 1500 VA, 250 V AC
• Max. continuous current: 2 A rms (cos
ϕ
= 1), 1 A rms (cos
ϕ
= 0.4)
• Minimum load: 500 mW (12 V, 10 mA)
• Contact material: Silver-nickel (AgN)
• Isolation between relay digital outputs, test voltage: 2.5 kV rms, 1 minute
Double Shielded
Single Shielded
Example: JAMAK by Draka NK Cables
Example: NOMAK by Draka NK Cables