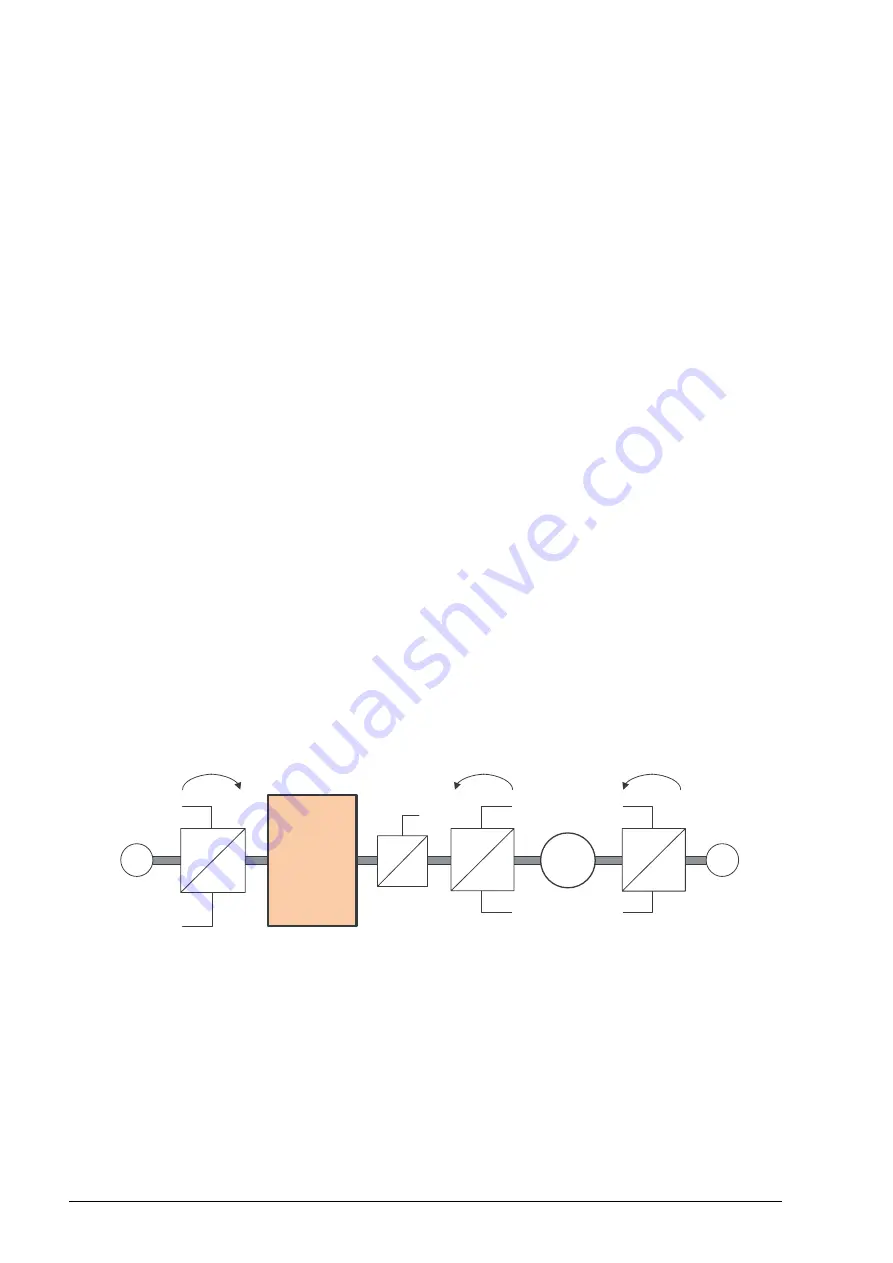
50 Program features
Encoder echo and emulation
Both encoder echo and emulation are supported by the above-mentioned FEN-xx
interfaces.
Encoder echo is available with TTL, TTL+ and HTL encoders. The signal received
from the encoder is relayed to the TTL output unchanged. This enables the
connection of one encoder to several drives.
Encoder emulation also relays the encoder signal to the output, but the signal is
either scaled, or position data converted to pulses. Emulation can be used when
absolute encoder or resolver position needs to be converted to TTL pulses, or when
the signal must be converted to a different pulse number than the original.
Load and motor feedback
Three different sources can be used as speed and position feedback: encoder 1,
encoder 2, or motor position estimate. Any of these can be used for load position
calculation or motor control. The load position calculation makes it possible, for
example, to determine the position of a conveyor belt or the height of the load on a
crane. The feedback sources are selected by parameters
For detailed parameter connections of the motor and load feedback functions, see
the block diagrams on pages
and
. For more information on load position
calculation, see section
).
Any mechanical gear ratios between the components (motor, motor encoder, load,
load encoder) are specified using the gear parameters shown in the diagram below.
Any gear ratio between the load encoder and the load is defined by
and
. Similarly, any gear ratio between the
motor encoder and the motor is defined by
and
. In case the internal estimated position is chosen as
load feedback, the gear ratio between the motor and load can be defined by
. By default, all of the ratios
mentioned above are 1:1. The ratios can only be changed with the drive stopped;
new settings require validation by
.
X
Y
X
Y
X
Y
X
Y
X
Y
1
Load encoder to load
scaling
Load encoder
Load
M
Motor
encoder
Motor to load
scaling
Motor encoder to motor
scaling
e
e
Summary of Contents for ACS880-x04
Page 1: ... ABB INDUSTRIAL DRIVES ACS880 primary control program Firmware manual ...
Page 4: ......
Page 18: ...18 Using the control panel ...
Page 24: ...24 Control locations and operating modes ...
Page 112: ...112 Application macros ...
Page 496: ...496 Additional parameter data ...
Page 544: ...544 Fault tracing ...
Page 602: ...602 Control chain diagrams ...