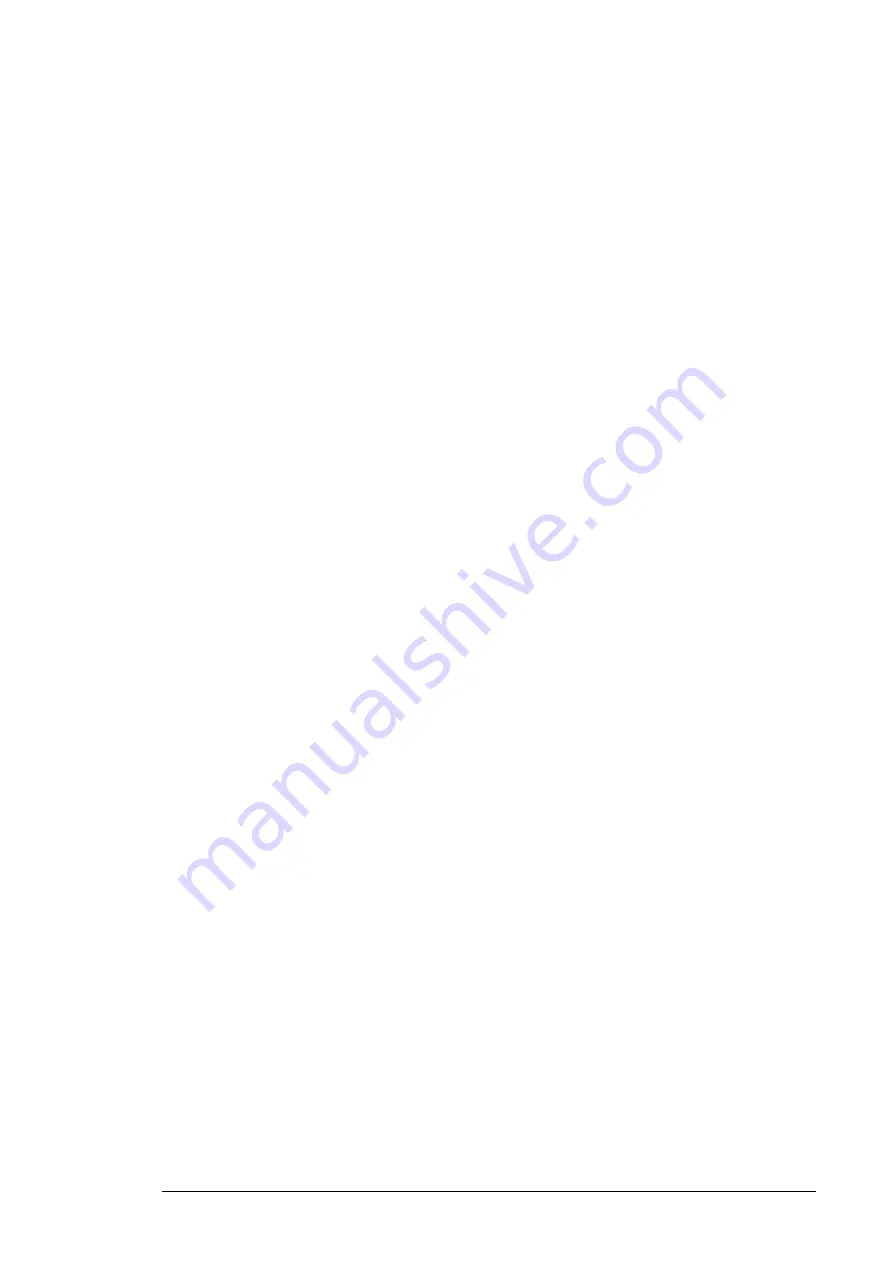
Maintenance
After the operation of the circuit is validated at start-up, the STO function shall be maintained
by periodic proof testing. In high demand mode of operation, the maximum proof test interval
is 20 years. In low demand mode of operation, the maximum proof test interval is 5 or 2
years; see section
. It is assumed that all dangerous failures of the
STO circuit are detected by the proof test. To perform the proof test, do the
.
Note:
See also the Recommendation of Use CNB/M/11.050 (published by the European
co-ordination of Notified Bodies) concerning dual-channel safety-related systems with
electromechanical outputs:
•
When the safety integrity requirement for the safety function is SIL 3 or PL e (cat. 3 or
4), the proof test for the function must be performed at least every month.
•
When the safety integrity requirement for the safety function is SIL 2 (HFT = 1) or PL
d (cat. 3), the proof test for the function must be performed at least every 12 months.
The STO function of the drive does not contain any electromechanical components.
In addition to proof testing, it is a good practice to check the operation of the function when
other maintenance procedures are carried out on the machinery.
Include the Safe torque off operation test described above in the routine maintenance
program of the machinery that the drive runs.
If any wiring or component change is needed after start-up, or the parameters are restored,
do the test given in section
Validation test procedure (page 225)
Use only spare parts approved by ABB.
Record all maintenance and proof test activities in the machine logbook.
■
Competence
The maintenance and proof test activities of the safety function must be carried out by a
competent person with adequate expertise and knowledge of the safety function as well as
functional safety, as required by IEC 61508-1 clause 6.
The Safe torque off function 229
Summary of Contents for ACS880-37LC-0390A-7
Page 1: ... ABB INDUSTRIAL DRIVES ACS880 37LC drives Hardware manual ...
Page 2: ......
Page 4: ......
Page 13: ...16 Resistor braking Further information Table of contents 13 ...
Page 14: ...14 ...
Page 24: ...24 ...
Page 28: ...28 ...
Page 50: ...50 ...
Page 70: ...70 Mechanical installation ...
Page 110: ...10 110 Electrical installation ...
Page 113: ...With FDPI 02 modules OPEN TERMINATED 1 1 2 2 OPEN TERMINATED 3 Electrical installation 113 11 ...
Page 134: ...134 ...
Page 140: ...140 ...
Page 148: ...a b c 148 Maintenance ...
Page 151: ...4 5 6 Maintenance 151 ...
Page 164: ...164 ...
Page 174: ...174 ...
Page 196: ...196 ...
Page 199: ... Dimension drawing examples ACS880 37LC 0390A 7 with main contactor Dimensions 199 ...
Page 201: ...ACS880 37LC 1270A 7 with common motor terminal cubicle Dimensions 201 ...
Page 202: ...ACS880 37LC 1940A 7 with common motor terminal cubicle 202 Dimensions ...
Page 205: ...Location and size of input terminals Contact ABB for details Dimensions 205 ...
Page 206: ... 100 kA input cubicle option F274 206 Dimensions ...
Page 208: ...Inverter module cubicle with two R8i modules bottom cable exit 208 Dimensions ...
Page 209: ...Inverter module cubicle with three R8i modules bottom cable exit Dimensions 209 ...
Page 210: ...Brake chopper cubicle 210 Dimensions ...
Page 212: ...Cubicle width 300 mm top cable exit 212 Dimensions ...
Page 213: ...Cubicle width 400 mm bottom cable exit Dimensions 213 ...
Page 214: ...Cubicle width 400 mm top cable exit 214 Dimensions ...
Page 215: ...Cubicle width 600 mm bottom cable exit Dimensions 215 ...
Page 216: ...Cubicle width 600 mm top cable exit 216 Dimensions ...
Page 238: ...238 ...
Page 240: ...240 ...