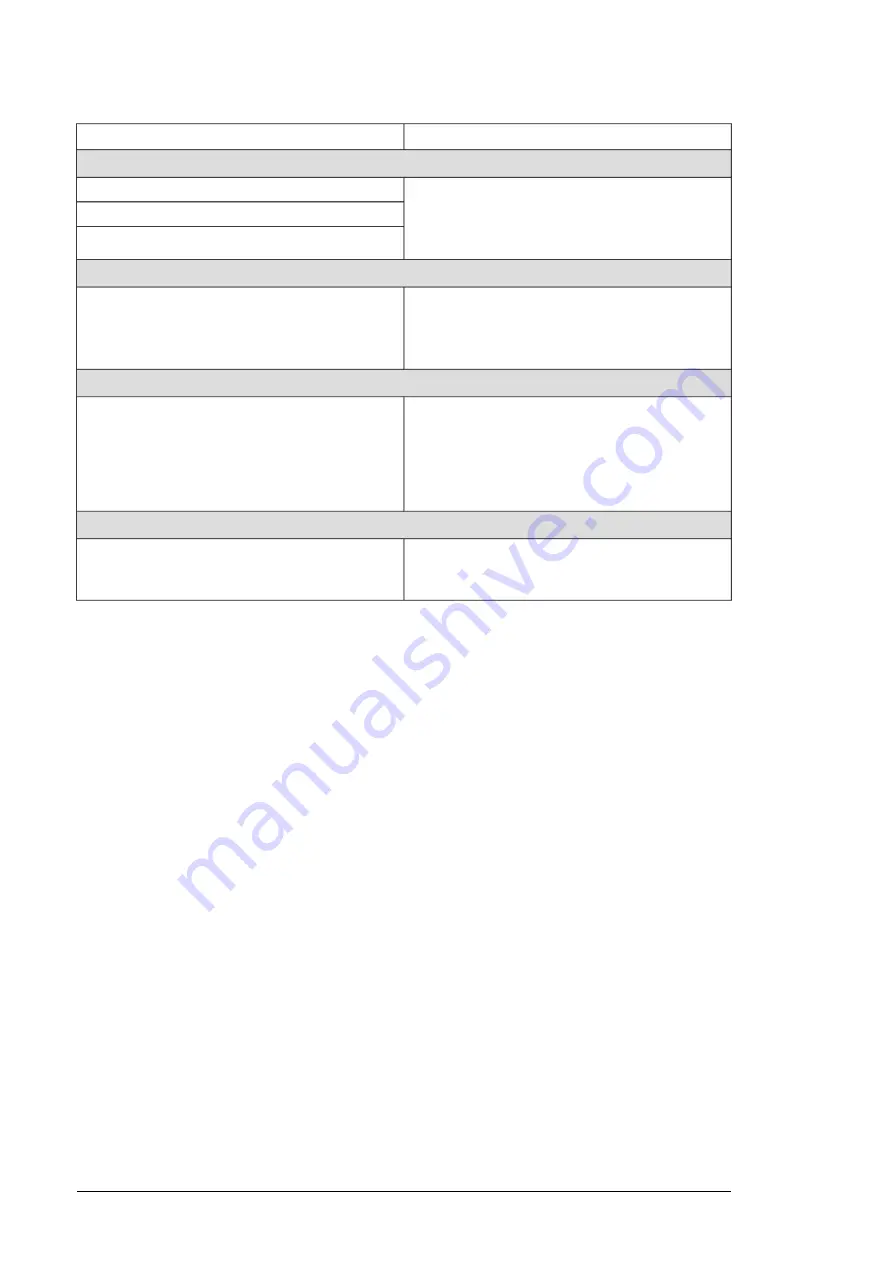
Notes
Wiring method
Conduit - Metallic
1) 2)
Prefer symmetrical shielded VFD cable.
Electrical metallic tubing: Type EMT
Use separate conduit run for each motor.
Rigid metal conduit: Type RMC
Do not run input power wiring and motor wiring in the
same conduit.
Liquid-tight flexible metal electrical conduit: Type LFMC
Conduit - Non-metallic
2)
3)
Prefer symmetrical shielded VFD cable.
Liquid-tight flexible non-metallic conduit: Type LFNC
Use separate conduit run for each motor.
Do not run input power wiring and motor wiring in the
same conduit.
Wireways
2)
Prefer symmetrical shielded VFD cable.
Metallic
Separate motor wiring from input power wiring and
other low voltage wiring.
Do not run outputs of multiple drives parallel. Bundle
each cable (wiring) together and use separators where
possible.
Free air
2)
Prefer symmetrical shielded VFD cable.
Enclosures, air handlers, etc.
Allowed internally in enclosures when in accordance
with UL.
1) Metallic conduit may be used as an additional ground path, provided this path is a solid path capable of handling ground
currents.
2) See NFPA NEC 70, UL, and local codes for your application.
3) Non-metallic conduit use underground is allowed; however, these installations inherently have an increased chance for
nuisance problems due to the potential for water/moisture in the conduit. Water/moisture in the conduit increases the
likelihood of VFD faults or warnings. Proper installation is required to make sure there is no intrusion of water/moisture.
Metal conduit
Couple separate parts of a metal conduit together: bridge the joints with a ground conductor
bonded to the conduit on each side of the joint. Also bond the conduits to the drive enclosure
and motor frame. Use separate conduits for input power, motor, brake resistor, and control
wiring. Do not run motor wiring from more than one drive in the same conduit.
■
Power cable shield
If the cable shield is used as the sole protective earth (PE) conductor, make sure that its
conductivity agrees with the PE conductor requirements.
To effectively suppress radiated and conducted radio-frequency emissions, the cable shield
conductivity must be at least 1/10 of the phase conductor conductivity. The requirements
are easily met with a copper or aluminum shield. The minimum requirement of the motor
cable shield of the drive is shown below. It consists of a concentric layer of copper wires
with an open helix of copper tape or copper wire. The better and tighter the shield, the lower
the emission level and bearing currents.
86 Guidelines for planning the electrical installation
Summary of Contents for ACS880-14
Page 1: ...ABB INDUSTRIAL DRIVES ACS880 14 drive modules 132 400 kW 200 400 hp Hardware manual...
Page 2: ......
Page 4: ......
Page 14: ...14...
Page 24: ...24...
Page 30: ...30...
Page 54: ...54...
Page 64: ...64...
Page 98: ...98...
Page 114: ...With twin connectors in the control panel holder 1 2 3 1 114 Electrical installation...
Page 115: ...With FDPI 02 modules OPEN TERMIN ATED 1 1 2 2 OPEN TERMINATED 3 Electrical installation 115 11...
Page 142: ...4 5 6 3 3 1 1 1 1 2 142 Installation example with full cabling panels option H381...
Page 150: ...150 Installation example with full cabling panels option H381...
Page 156: ...156...
Page 204: ...Standard configuration 204 Dimension drawings...
Page 206: ...Drive module with options 0B051 H356 0H371 206 Dimension drawings...
Page 207: ...Configuration with option H381 3AXD50000323210 Dimension drawings 207...
Page 208: ...LCL filter module 208 Dimension drawings...
Page 212: ...External control unit 3AXD50000011687 212 Dimension drawings...
Page 230: ...Declaration of conformity 230 The Safe torque off function...
Page 241: ...241...
Page 246: ...246...