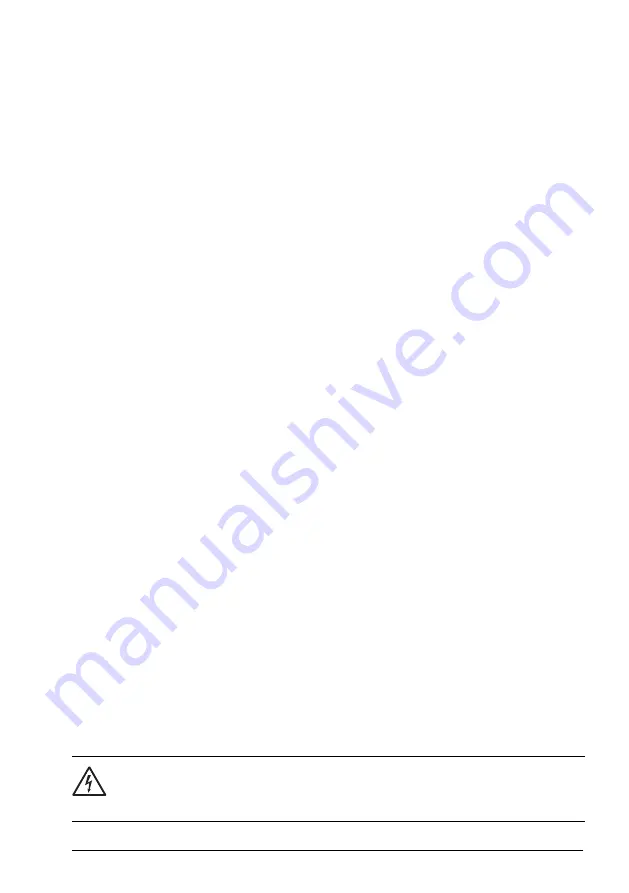
Note:
As standard, the drive contains capacitors connected between the main circuit
and the frame. These capacitors and long motor cables increase the ground leakage
current and may cause nuisance faults in residual current devices.
Implementing the emergency stop function
For safety reasons, install the emergency stop devices at each operator control station
and at other operating stations where emergency stop may be needed. Implement the
emergency stop according to relevant standards.
Note:
You can use the Safe torque off function of the drive to implement the Emergency
stop function.
Implementing the Safe torque off function
See
The Safe torque off function (page 209)
.
Implementing the power loss ride-through function
If the incoming supply voltage is cut off, the drive will continue to operate by utilizing
the kinetic energy of the rotating motor. The drive will be fully operational as long as the
motor rotates and generates energy to the drive.
If you equip the drive with a main contactor or breaker, make sure that it restores the
drive input power after a short break. The contactor must either re-connect after the
break automatically, or remain closed over the break. Depending on the contactor control
circuit design, this can require an additional hold circuit, uninterruptible auxiliary power
supply or auxiliary power supply buffering.
Note that if the power loss lasts so long that the drive trips on undervoltage, a fault reset
and a fresh start command is required to continue operation.
Implement the power-loss ride-through function as follows:
1. Enable the power-loss ride-through function of the drive (parameter
30.31
).
2. If the installation is equipped with a main contactor, prevent its tripping at the input
power break. For example, use a time delay relay (hold) in the contactor control
circuit.
3. Enable the automatic restart of the motor after a short power supply break:
• Set the start mode to automatic (parameter
21.01
or
21.19
, depending on the
motor control mode being used).
• Define the automatic restart time (parameter
21.18
).
WARNING!
Make sure that a flying restart of the motor will not cause any danger. If you are
in doubt, do not implement the power loss ride-through function.
Guidelines for planning the electrical installation 77
Summary of Contents for ACS880-11
Page 1: ... ABB INDUSTRIAL DRIVES ACS880 11 drives Hardware manual ...
Page 2: ......
Page 4: ......
Page 26: ...26 ...
Page 52: ...52 ...
Page 82: ...82 ...
Page 95: ...R6 R8 IP21 R6 R8 IP55 Electrical installation IEC 95 ...
Page 103: ...R6 1 5 N m 0 5 N m Electrical installation IEC 103 ...
Page 104: ...R8 1 5 N m 0 5 0 6 N m 104 Electrical installation IEC ...
Page 116: ...R6 R8 UL Type 1 R6 R8 UL Type 12 116 Electrical installation North America NEC ...
Page 142: ...142 ...
Page 154: ... Fan arrow must point up 154 Maintenance ...
Page 160: ...160 ...
Page 181: ... Package dimensions R6 R3 R8 Technical data 181 ...
Page 202: ...R3 IP21 UL Type 1 3AXD50000045323 202 Dimension drawings ...
Page 203: ...R3 Option B056 IP55 UL Type 12 3AXD50000045322 Dimension drawings 203 ...
Page 204: ...R6 IP21 UL Type 1 3AXD50000045353 204 Dimension drawings ...
Page 205: ...R6 Option B056 IP55 UL Type 12 3AXD50000045352 Dimension drawings 205 ...
Page 206: ...R8 IP21 UL Type 1 3AXD50000047667 206 Dimension drawings ...
Page 207: ...R8 Option B056 IP55 UL Type 12 3AXD50000047667 Dimension drawings 207 ...
Page 208: ...208 ...
Page 225: ... Declarations of conformity The Safe torque off function 225 ...