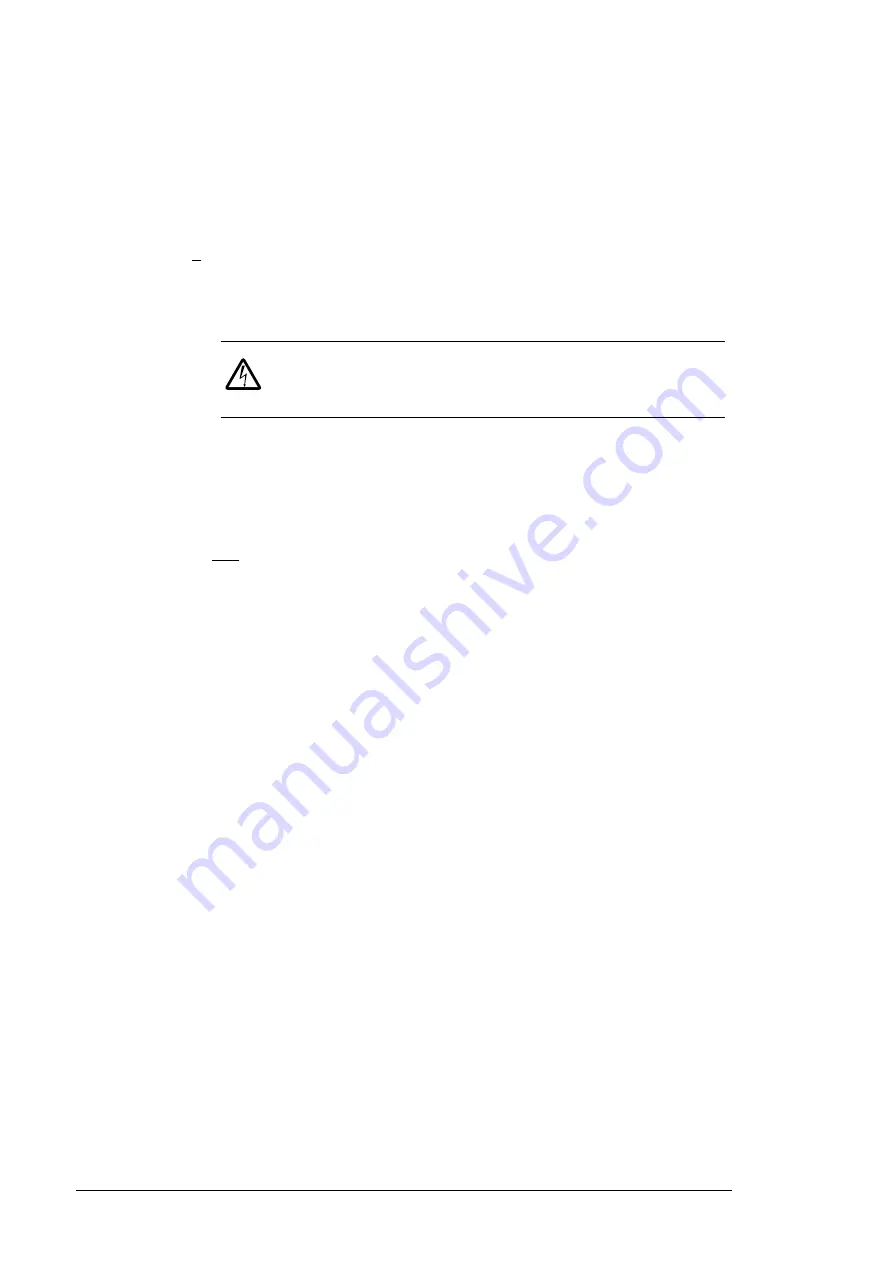
162 Resistor braking
Selecting a custom resistor
If you use a resistor other than the default resistor, make sure that:
1. The resistance of the custom resistor is greater or equal than the resistance of the
default resistor in the rating table:
where
2. The load capacity of the custom resistor is higher than the instantaneous maximum
power consumption of the resistor when it is connected to the drive DC link voltage by
the chopper:
where
Selecting and routing the external brake resistor cables
Use the same cable type for the resistor cabling as for the drive input cabling to ensure
that the input fuses also protect the resistor cable. Alternatively, a two conductor shielded
cable with the same cross-sectional area can be used.
Minimizing electromagnetic interference
Obey these rules in order to minimize electromagnetic interference caused by the rapid
current changes in the resistor cables:
•
Shield the braking power line completely, either by using shielded cable or a metallic
enclosure. Unshielded single-core cable can only be used if it is routed inside a
cabinet that efficiently suppresses the radiated emissions.
•
Install the cables away from other cable routes.
•
Avoid long parallel runs with other cables. The minimum parallel cabling separation
distance should be 0.3 meters.
•
Cross the other cables at right angles.
•
Keep the cable as short as possible in order to minimize the radiated emissions and
stress on chopper IGBTs. The longer the cable the higher the radiated emissions,
inductive load and voltage peaks over the IGBT semiconductors of the brake chopper.
R
Resistance of the custom resistor.
WARNING
! Never use a brake resistor with a resistance smaller than
R
min
.
The drive and the chopper are not able to handle the overcurrent caused by
the low resistance.
R
min
Resistance of the default resistor
P
r
Load capacity of the custom resistor
U
DC
Drive DC link voltage.
1.35 · 1.25 · 415 V DC (when supply voltage is 380 to 415 V AC)
1.35 · 1.25 · 500 V DC (when supply voltage is 440 to 500 V AC) or
1.35 · 1.25 · 690 V DC (when supply voltage is 525 to 690 AC)
R
Resistance of the custom resistor
R
>
R
min
P
r
>
U
DC
R
2
Summary of Contents for ACS880-07XT Series
Page 1: ...ABB industrial drives Hardware manual ACS880 07XT drives 400 to 1200 kW ...
Page 4: ......
Page 12: ...12 ...
Page 20: ...20 Safety instructions ...
Page 26: ...26 Introduction to the manual ...
Page 54: ...54 Mechanical installation ...
Page 89: ...Electrical installation 89 PE 11 8 4 9 11 ...
Page 94: ...94 Electrical installation ...
Page 112: ...112 Fault tracing ...
Page 123: ...Maintenance 123 5 6 7 ...
Page 124: ...124 Maintenance 8 10 9 ...
Page 126: ...126 Maintenance 6 5 4 ...
Page 127: ...Maintenance 127 9 8 7 ...
Page 128: ...128 Maintenance 12 11 10 ...
Page 149: ...Dimensions 149 Dimension drawing examples Frame 2 R11 R10 with brake chopper ...
Page 150: ...150 Dimensions Frame 2 R11 R10 without brake chopper ...
Page 153: ...Dimensions 153 Location of input terminals ACS880 07XT 12 pulse ...
Page 154: ...154 Dimensions Location of output terminals ACS880 07XT R10 with du dt ...
Page 155: ...Dimensions 155 Location of output terminals ACS880 07XT R10 without du dt ...
Page 156: ...156 Dimensions Location of output terminals ACS880 07XT R11 with du dt ...
Page 157: ...Dimensions 157 Location of output terminals ACS880 07XT R11 without du dt ...
Page 158: ...158 Dimensions Location of PE terminals ACS880 07XT ...
Page 159: ...Dimensions 159 Location of resistor terminals ACS880 07XT R10 ...
Page 160: ...160 Dimensions Location of resistor terminals ACS880 07XT R11 ...
Page 168: ...www abb com drives www abb com drivespartners 3ABD00043579 Rev C EN 2018 01 01 Contact us ...