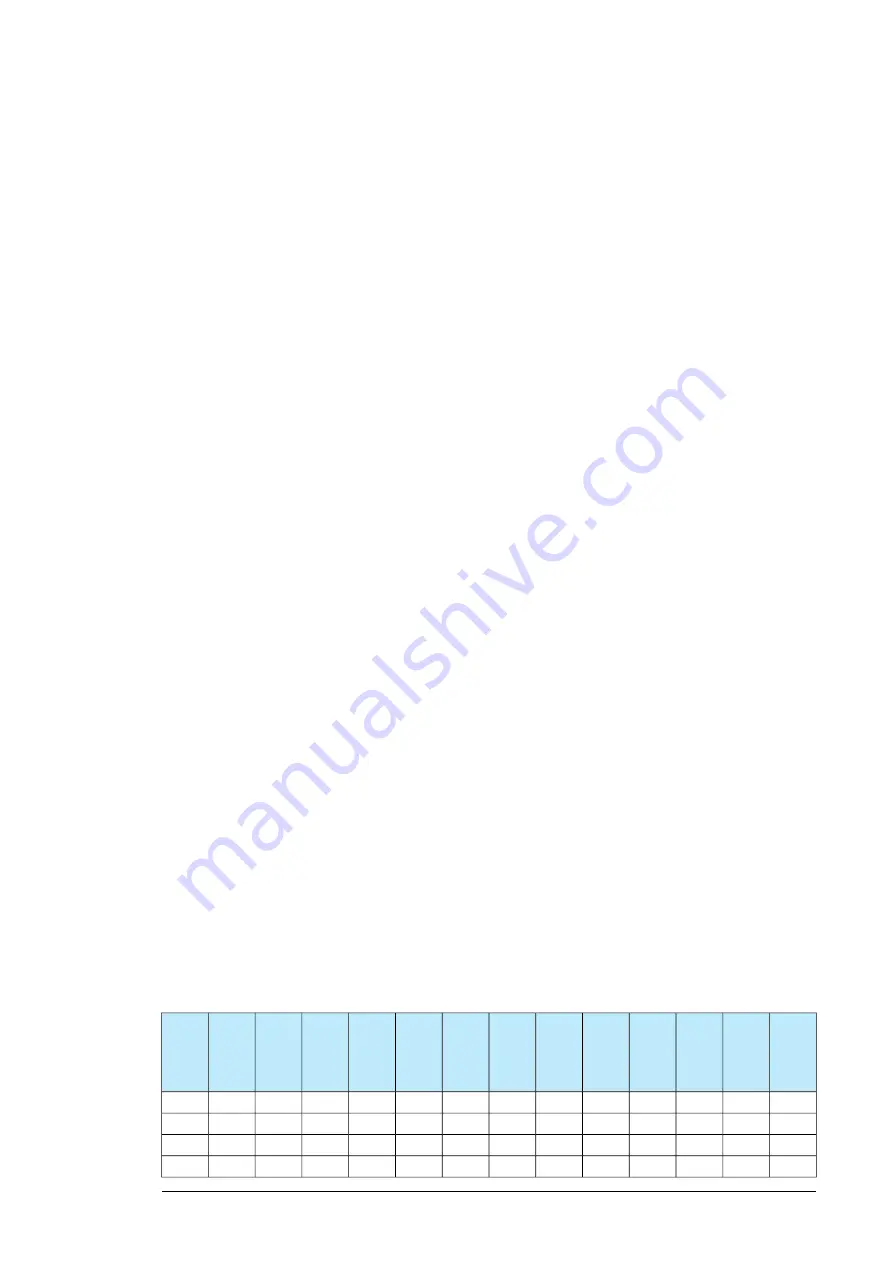
•
When the safety integrity requirement for the safety function is SIL 2 (HFT = 1) or PL d
(cat. 3), the proof test for the function must be performed at least every 12 months.
The STO function of the drive does not contain any electromechanical components.
In addition to proof testing, it is a good practice to check the operation of the function when
other maintenance procedures are carried out on the machinery.
Include the Safe torque off operation test described above in the routine maintenance
program of the machinery that the inverter runs.
If any wiring or component change is needed after start up, or the parameters are restored,
follow the test given in section
Acceptance test procedure (page 258)
Use only ABB approved spare parts.
Record all maintenance and proof test activities in the machine logbook.
■
Competence
The maintenance and proof test activities of the safety function must be carried out by a
competent person with adequate expertise and knowledge of the safety function as well as
functional safety, as required by IEC 61508-1 clause 6.
Fault tracing
The indications given during the normal operation of the Safe torque off function are selected
by inverter control program parameter
31.22
.
The diagnostics of the Safe torque off function cross-compare the status of the two STO
channels. In case the channels are not in the same state, a fault reaction function is
performed and the inverter trips on an “STO hardware failure” fault. An attempt to use the
STO in a non-redundant manner, for example activating only one channel, will trigger the
same reaction.
See the firmware manual of the inverter control program for the indications generated by
the inverter, and for details on directing fault and warning indications to an output on the
control unit for external diagnostics.
Any failures of the Safe torque off function must be reported to ABB.
Safety data
The safety data for the Safe torque off function is given below.
Note:
The safety data is calculated for redundant use, and does not apply if both STO channels
are not used.
Life-
time
(a)
CCF
HFT
Cat.
DC
(%)
MTTF
D
(a)
PFD
avg
(T
1
= 5
a)
PFD
avg
(T
1
= 2
a)
PFH
�
(T
1
=
20 a)
(1/h)
SFF
(%)
PL
SC
SIL/SIL-
CL
Frame
size
20
80
1
3
≥90
16330
1.3E-06
5.5E-07
6.2E-11
>99
e
3
3
2×R8i
20
80
1
3
≥90
12390
1.6E-06
6.5E-07
7.3E-11
>99
e
3
3
3×R8i
20
80
1
3
≥90
9980
1.9E-06
7.6E-07
8.4E-11
>99
e
3
3
4×R8i
20
80
1
3
≥90
8360
2.1E-06
8.6E-07
9.5E-11
>99
e
3
3
5×R8i
The Safe torque off function 261
Summary of Contents for ACS880-07
Page 1: ...ABB industrial drives Hardware manual ACS880 07 drives 560 to 2800 kW ...
Page 2: ......
Page 4: ......
Page 22: ...22 ...
Page 28: ...28 ...
Page 94: ...94 ...
Page 112: ...Electrical installation 109 5 6 4 3 112 Electrical installation ...
Page 113: ...110 Electrical installation 7 8 8 Electrical installation 113 ...
Page 114: ...Electrical installation 111 9 10 114 Electrical installation ...
Page 116: ...Electrical installation 113 4 5 3 6 7 116 Electrical installation ...
Page 118: ...2 11 b PE 10 7 5 6 8 a 360 grounding detail 118 Electrical installation ...
Page 128: ...128 ...
Page 146: ...146 ...
Page 148: ...148 ...
Page 159: ...12 Install and tighten the two M4 12 T20 screws 10 11 12 Maintenance 159 ...
Page 162: ...6 6a 6a 6b 7a 7b 7 8 8a 8b 162 Maintenance ...
Page 166: ...166 Maintenance 6 6 7 8 7 166 Maintenance ...
Page 173: ...6 Reinstall the cover removed earlier and close the cubicle door 4 4 D7T D8T Maintenance 173 ...
Page 213: ... Dimension drawing examples Frame 2 D7T 2 R8i 12 pulse A004 Dimensions 213 ...
Page 214: ...Frame 1 D8T 2 R8i IP22 214 Dimensions ...
Page 215: ...Frame 1 D8T 2 R8i IP54 B055 Dimensions 215 ...
Page 216: ...Frame 1 D8T 2 R8i with common motor terminal cubicle H359 1 2 216 Dimensions ...
Page 217: ...Frame 1 D8T 2 R8i with common motor terminal cubicle H359 2 2 Dimensions 217 ...
Page 218: ...Frame 1 D8T 2 R8i with brake choppers and resistors D150 D151 1 2 218 Dimensions ...
Page 219: ...Frame 1 D8T 2 R8i with brake choppers and resistors D150 D151 2 2 Dimensions 219 ...
Page 220: ...Frame 1 D8T 2 R8i with sine output filter E206 1 2 220 Dimensions ...
Page 221: ...Frame 1 D8T 2 R8i with sine output filter E206 2 2 Dimensions 221 ...
Page 222: ...Frame 2 D8T 2 R8i 12 pulse A004 with grounding switch F259 222 Dimensions ...
Page 223: ...Frame 2 D8T 3 R8i 1 2 Dimensions 223 ...
Page 224: ...Frame 2 D8T 3 R8i 2 2 224 Dimensions ...
Page 225: ...Frame 2 D8T 3 R8i with common motor terminal cubicle H359 1 2 Dimensions 225 ...
Page 226: ...Frame 2 D8T 3 R8i with common motor terminal cubicle H359 2 2 226 Dimensions ...
Page 227: ...Frame 2 D8T 3 R8i with top entry top exit H351 H353 1 2 Dimensions 227 ...
Page 228: ...Frame 2 D8T 3 R8i with top entry top exit 2 2 228 Dimensions ...
Page 229: ...Frame 3 D8T 4 R8i 1 2 Dimensions 229 ...
Page 230: ...Frame 3 D8T 4 R8i 2 2 230 Dimensions ...
Page 231: ...Frame 3 D8T 4 R8i with common motor terminal cubicle H359 1 2 Dimensions 231 ...
Page 232: ...Frame 3 D8T 4 R8i with common motor terminal cubicle H359 2 2 232 Dimensions ...
Page 233: ...Frame 3 D8T 4 R8i with top entry top exit H351 H353 1 2 Dimensions 233 ...
Page 234: ...Frame 3 D8T 4 R8i with top entry top exit H351 H353 2 2 234 Dimensions ...
Page 235: ...Frame 4 D8T 5 R8i 6 pulse with top entry exit UL Listed C129 1 2 Dimensions 235 ...
Page 236: ...Frame 4 D8T 5 R8i 6 pulse with top entry exit UL Listed C129 2 2 236 Dimensions ...
Page 237: ... Dimensions of empty cubicles options C199 C200 C201 IP22 IP42 Dimensions 237 ...
Page 238: ...IP54 238 Dimensions ...
Page 243: ... 1000 mm UL CSA top cable entry Dimensions 243 ...
Page 244: ... 1000 mm UL CSA bottom cable entry 244 Dimensions ...
Page 264: ...264 ...
Page 272: ... 272 ...