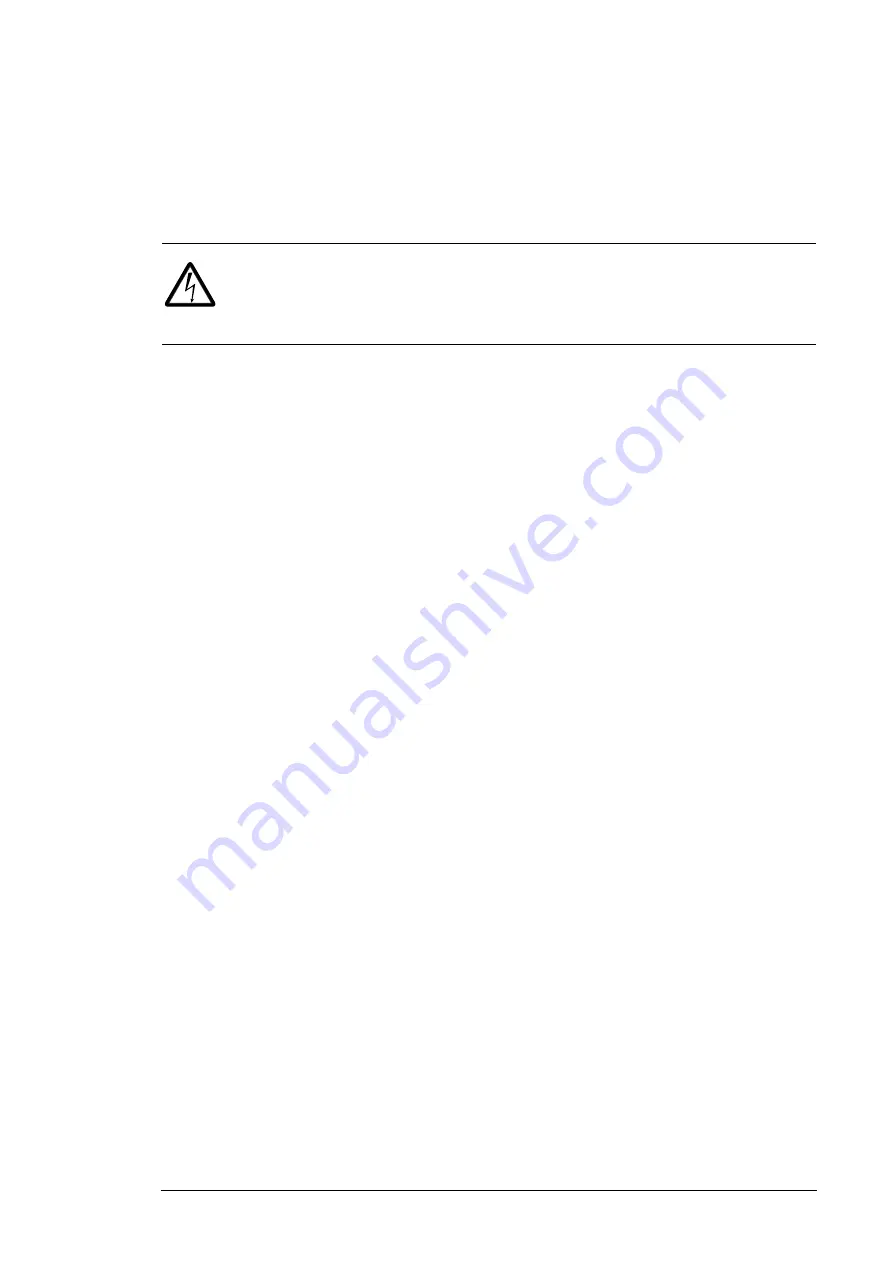
Guidelines for planning the electrical installation 69
Protecting the drive and the input power and motor cables against
thermal overload
The drive protects itself and the input and motor cables against thermal overload when the
cables are dimensioned according to the nominal current of the drive. No additional
thermal protection devices are needed.
WARNING!
If the drive is connected to multiple motors, use a separate circuit
breaker or fuses for protecting each motor cable and motor against overload. The
drive overload protection is tuned for the total motor load. It may not trip due to an
overload in one motor circuit only.
Protecting the motor against thermal overload
According to regulations, the motor must be protected against thermal overload and the
current must be switched off when overload is detected. The drive includes a motor
thermal protection function that protects the motor and switches off the current when
necessary. Depending on a drive parameter value, the function either monitors a
calculated temperature value (based on a motor thermal model) or an actual temperature
indication given by motor temperature sensors. The user can tune the thermal model
further by feeding in additional motor and load data.
The most common temperature sensors are:
•
motor sizes IEC 180…225: thermal switch, eg, Klixon
•
motor sizes IEC 200…250 and larger: PTC or Pt100.
See the firmware manual for more information on the motor thermal protection, and the
connection and use of the temperature sensors.
Protecting the drive against ground faults
The drive is equipped with an internal ground fault protective function to protect the drive
against ground faults in the motor and motor cable in TN (grounded) networks. This is not
a personal safety or a fire protection feature. The ground fault protective function can be
disabled with a parameter, refer to the firmware manual.
Measures for protection in case of direct or indirect contact, such as separation from the
environment by double or reinforced insulation or isolation from the supply system by a
transformer, can be applied.
Residual current device compatibility
The drive is suitable to be used with residual current devices of Type B.
Note:
The EMC filter of the drive includes capacitors connected between the main circuit
and the frame. These capacitors and long motor cables increase the ground leakage
current and can cause fault current circuit breakers to function.
Connecting drive modules to a common DC system
See
ACS880-01 drives and ACS880-04 drive modules common DC systems application
guide
(3AUA0000127818 [English]).
Summary of Contents for ACS880-04F
Page 1: ...ABB industrial drives Hardware manual ACS880 04F drive modules ...
Page 4: ......
Page 24: ...24 Introduction to the manual ...
Page 46: ...46 Guidelines for planning the mechanical installation ...
Page 102: ...102 Installation checklist ...
Page 106: ...106 Fault tracing ...
Page 135: ...Technical data 135 Declaration of Conformity ...
Page 136: ...136 Technical data ...
Page 140: ...140 Technical data ...
Page 142: ...142 Dimension drawings Standard configuration IP20 UL Open Type ...
Page 143: ...Dimension drawings 143 Drive module with options E208 and H370 IP20 UL Open Type ...
Page 144: ...144 Dimension drawings Drive module with options 0B051 E208 0H371 IP00 UL Open Type ...
Page 145: ...Dimension drawings 145 Drive module with options 0B051 E208 0H371 C217 IP00 UL Open Type ...
Page 146: ...146 Dimension drawings Drive module with options 0B051 0H371 IP00 UL Open Type ...
Page 147: ...Dimension drawings 147 Mounting plate 3AXD50000038119 ...
Page 148: ...148 Dimension drawings 3AXD50000038119 ...
Page 149: ...Dimension drawings 149 External control unit 3axd50000011687 ...
Page 150: ...150 Dimension drawings ...
Page 164: ...164 Safe torque off function ...