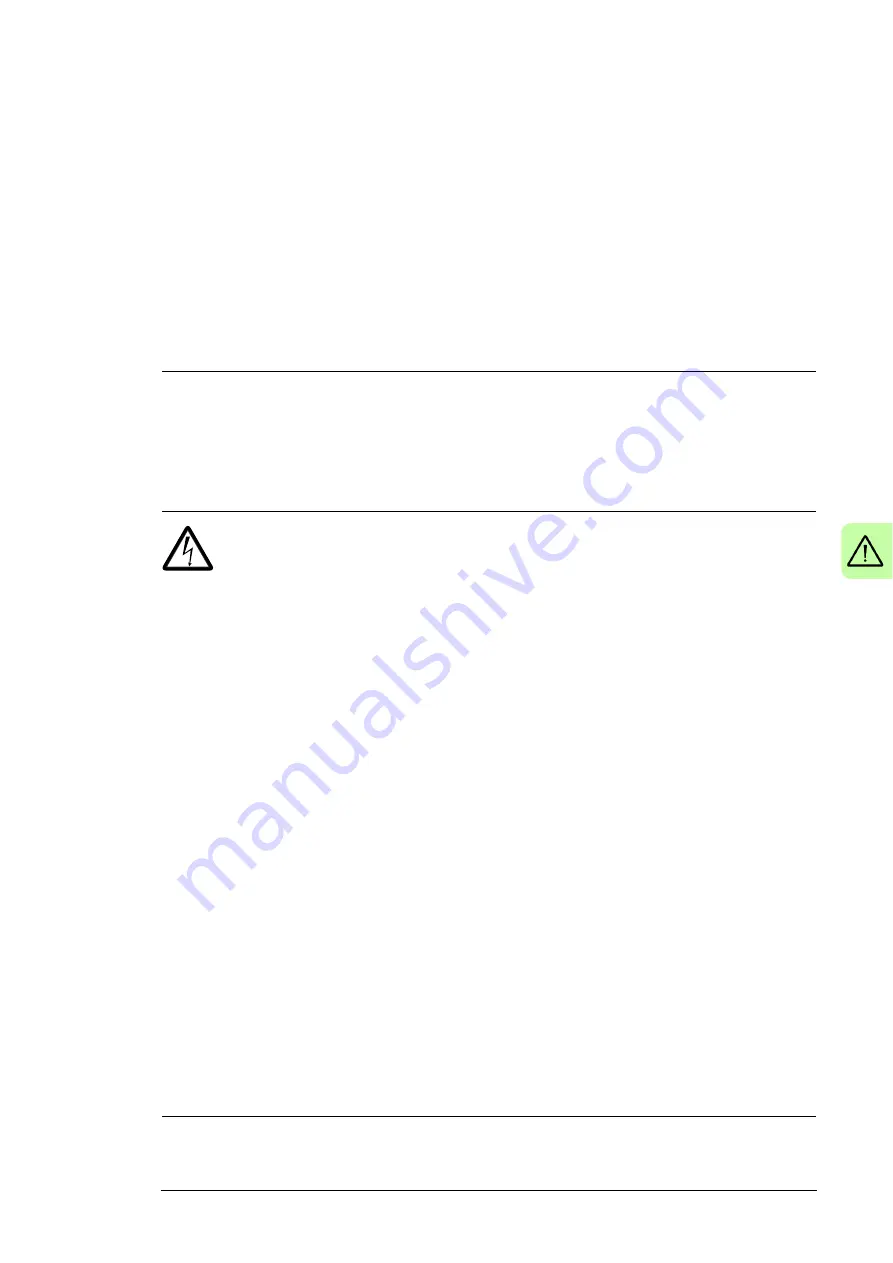
Safety instructions 15
•
The maximum number of drive power-ups is five in ten minutes. Too frequent power-
ups can damage the charging circuit of the DC capacitors.
•
Make sure that any safety circuits (for example, emergency stop and Safe torque off)
are validated in start-up. See chapter
for reference of the validation
instructions.
Note:
•
If you select an external source for start command and it is on, the drive will start
immediately after fault reset unless you configure the drive for pulse start. See the
firmware manual.
•
When the control location is not set to Local, the stop key on the control panel will not
stop the drive.
Electrical safety in installation, start-up and maintenance
Precautions before electrical work
These warnings are for all personnel that do work on the drive, motor cable or motor.
WARNING!
Obey these
instructions. If you ignore them, injury or death, or
damage to the equipment can occur. If you are not a qualified electrician, do not
do installation or maintenance work. Go through these steps before you begin any
installation or maintenance work.
1. Clearly identify the work location.
2. Disconnect all possible voltage sources.
•
Open the main disconnector of the drive.
•
Open the disconnector of the supply transformer as the main disconnector of the
drive does not remove the voltage from the input busbars of the drive.
•
Make sure that reconnection is not possible. Lock the disconnectors to open
position and attach a warning notice to them.
•
Disconnect any external power sources from the control circuits before you do
work on the control cables.
•
After you disconnect the drive, always wait for 5 minutes to let the intermediate
circuit capacitors discharge before you continue.
3. Protect any other energized parts in the work location against contact.
4. Take special precautions when close to bare conductors.
5. Measure that the installation is de-energized.
•
Use a multimeter with an impedance of at least 1 Mohm.
•
Make sure that the voltage between the drive module input power terminals
(L1/U1, L2/V1, L3/W1) and the grounding (PE) busbar is close to 0 V.
•
Make sure that the voltage between the drive module UDC+ and UDC- terminals
and the grounding (PE) busbar is close to 0 V.
6. Install temporary grounding as required by the local regulations.
7. Ask for a permit to work from the person in control of the electrical installation work.
Summary of Contents for ACS880-04F
Page 1: ...ABB industrial drives Hardware manual ACS880 04F drive modules ...
Page 4: ......
Page 24: ...24 Introduction to the manual ...
Page 46: ...46 Guidelines for planning the mechanical installation ...
Page 102: ...102 Installation checklist ...
Page 106: ...106 Fault tracing ...
Page 135: ...Technical data 135 Declaration of Conformity ...
Page 136: ...136 Technical data ...
Page 140: ...140 Technical data ...
Page 142: ...142 Dimension drawings Standard configuration IP20 UL Open Type ...
Page 143: ...Dimension drawings 143 Drive module with options E208 and H370 IP20 UL Open Type ...
Page 144: ...144 Dimension drawings Drive module with options 0B051 E208 0H371 IP00 UL Open Type ...
Page 145: ...Dimension drawings 145 Drive module with options 0B051 E208 0H371 C217 IP00 UL Open Type ...
Page 146: ...146 Dimension drawings Drive module with options 0B051 0H371 IP00 UL Open Type ...
Page 147: ...Dimension drawings 147 Mounting plate 3AXD50000038119 ...
Page 148: ...148 Dimension drawings 3AXD50000038119 ...
Page 149: ...Dimension drawings 149 External control unit 3axd50000011687 ...
Page 150: ...150 Dimension drawings ...
Page 164: ...164 Safe torque off function ...