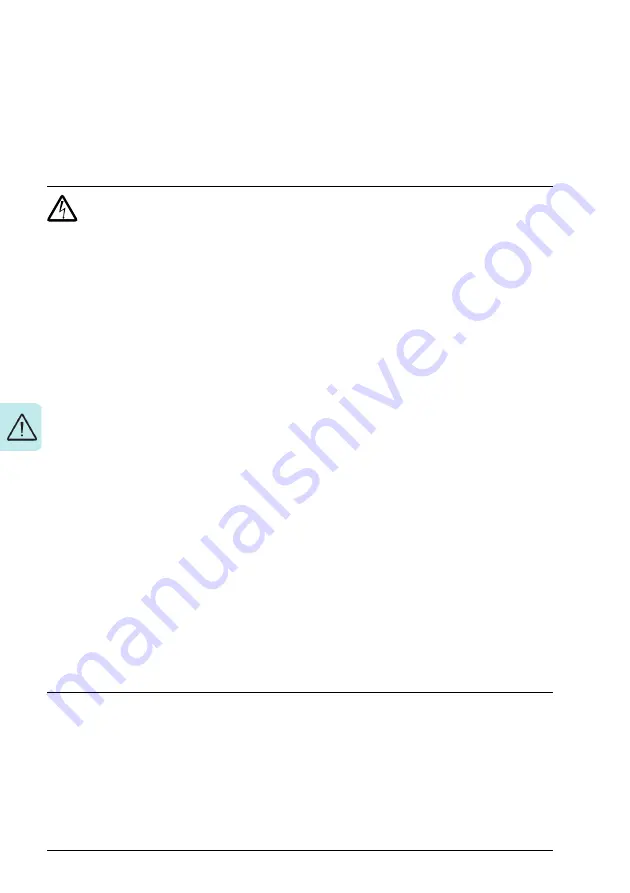
18 Safety instructions
Additional instructions for permanent magnet motor drives
Safety in installation, start-up and maintenance
These are additional warnings concerning permanent magnet motor drives. The other
safety instructions in this chapter are also valid.
WARNING!
Obey these instructions. If you ignore them, injury or death and
damage to the equipment can occur.
• Do not work on a drive when a rotating permanent magnet motor is connected
to it. A rotating permanent magnet motor energizes the drive including its input
power terminals.
Before installation, start-up and maintenance work on the drive:
• Stop the motor.
• Disconnect the motor from the drive with a safety switch or by other means.
• If you cannot disconnect the motor, make sure that the motor cannot rotate during
work. Make sure that no other system, like hydraulic crawling drives, can rotate
the motor directly or through any mechanical connection like felt, nip, rope, etc.
• Measure that the installation is de-energized.
•
Use a multimeter with an impedance of at least 1 Mohm.
•
Make sure that the voltage between the drive output terminals (T1/U, T2/V,
T3/W) and the grounding (PE) busbar is close to 0 V.
•
Make sure that the voltage between the drive input power terminals (L1, L2,
L3) and the grounding (PE) busbar is close to 0 V.
•
Make sure that the voltage between the drive DC terminals (UDC+, UDC-) and
the grounding (PE) terminal is close to 0 V.
• Install temporary grounding to the drive output terminals (T1/U, T2/V, T3/W).
Connect the output terminals together as well as to the PE.
Start-up and operation:
• Make sure that the operator cannot run the motor over the rated speed. Motor
overspeed causes overvoltage that can damage or explode the capacitors in the
intermediate circuit of the drive.
Summary of Contents for ACS380 Series
Page 1: ...ABB MACHINERY DRIVES ACS380 drives Hardware manual...
Page 4: ......
Page 12: ...12 Table of contents...
Page 20: ...20 Safety instructions...
Page 46: ...46 Mechanical installation...
Page 60: ...60 Planning the electrical installation...
Page 86: ...86 Maintenance...
Page 120: ...120 Technical data...
Page 122: ...122 Dimension drawings Frame R0 1 phase 230 V...
Page 123: ...Dimension drawings 123 Frame R0 400 V...
Page 124: ...124 Dimension drawings Frame R1 230 V...
Page 125: ...Dimension drawings 125 Frame R1 3 phase 230 V and 3 phase 400 V...
Page 126: ...126 Dimension drawings Frame R2 230 V...
Page 127: ...Dimension drawings 127 Frame R2 400 V...
Page 128: ...128 Dimension drawings Frame R3 400 V...
Page 129: ...Dimension drawings 129 Frame R4 400 V...
Page 130: ...130 Dimension drawings...
Page 138: ...138 Resistor braking...
Page 169: ...BTAC 02 pulse encoder interface module 169 Dimensions 3AXD50000031154 rev A...