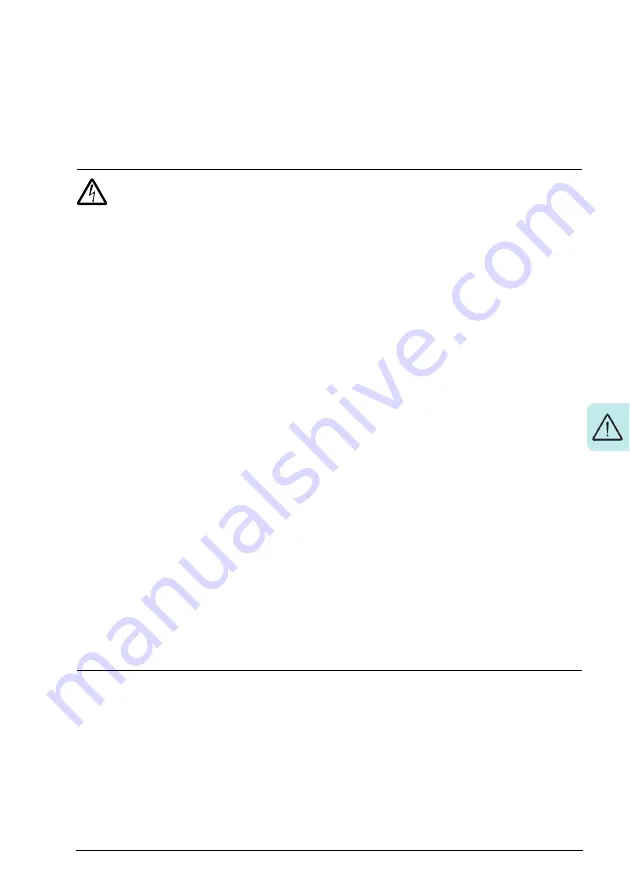
Safety instructions 15
Electrical safety in installation, start-up and maintenance
Precautions before electrical work
These warnings are for all personnel who do work on the drive, motor cable or motor.
WARNING!
Obey these instructions. If you ignore them, injury or death, or
damage to the equipment can occur. If you are not a qualified electrician, do
not do electrical installation or maintenance work. Do these steps before you begin
any installation or maintenance work.
1. Clearly identify the work location.
2. Disconnect all possible voltage sources.
•
Open the main disconnector at the power supply of the drive.
•
Make sure that reconnection is not possible. Lock the disconnector to open
position and attach a warning notice to it.
•
Disconnect any external power sources from the control circuits before you do
work on the control cables.
•
After you disconnect the drive, always wait for 5 minutes to let the
intermediate circuit capacitors discharge before you continue.
3. Protect any other energized parts in the work location against contact.
4. Take special precautions when close to bare conductors.
5. Measure that the installation is de-energized.
•
Use a multimeter with an impedance of at least 1 Mohm.
•
Make sure that the voltage between the drive input power terminals (L1, L2,
L3) and the grounding terminal (PE) is close to 0 V.
•
Make sure that the voltage between the drive DC terminals (UDC+ and UDC-)
and the grounding terminal (PE) is close to 0 V.
6. Install temporary grounding as required by the local regulations.
7. Ask for a permit to work from the person in control of the electrical installation
work.
Summary of Contents for ACS380 Series
Page 1: ...ABB MACHINERY DRIVES ACS380 drives Hardware manual...
Page 4: ......
Page 12: ...12 Table of contents...
Page 20: ...20 Safety instructions...
Page 46: ...46 Mechanical installation...
Page 60: ...60 Planning the electrical installation...
Page 86: ...86 Maintenance...
Page 120: ...120 Technical data...
Page 122: ...122 Dimension drawings Frame R0 1 phase 230 V...
Page 123: ...Dimension drawings 123 Frame R0 400 V...
Page 124: ...124 Dimension drawings Frame R1 230 V...
Page 125: ...Dimension drawings 125 Frame R1 3 phase 230 V and 3 phase 400 V...
Page 126: ...126 Dimension drawings Frame R2 230 V...
Page 127: ...Dimension drawings 127 Frame R2 400 V...
Page 128: ...128 Dimension drawings Frame R3 400 V...
Page 129: ...Dimension drawings 129 Frame R4 400 V...
Page 130: ...130 Dimension drawings...
Page 138: ...138 Resistor braking...
Page 169: ...BTAC 02 pulse encoder interface module 169 Dimensions 3AXD50000031154 rev A...