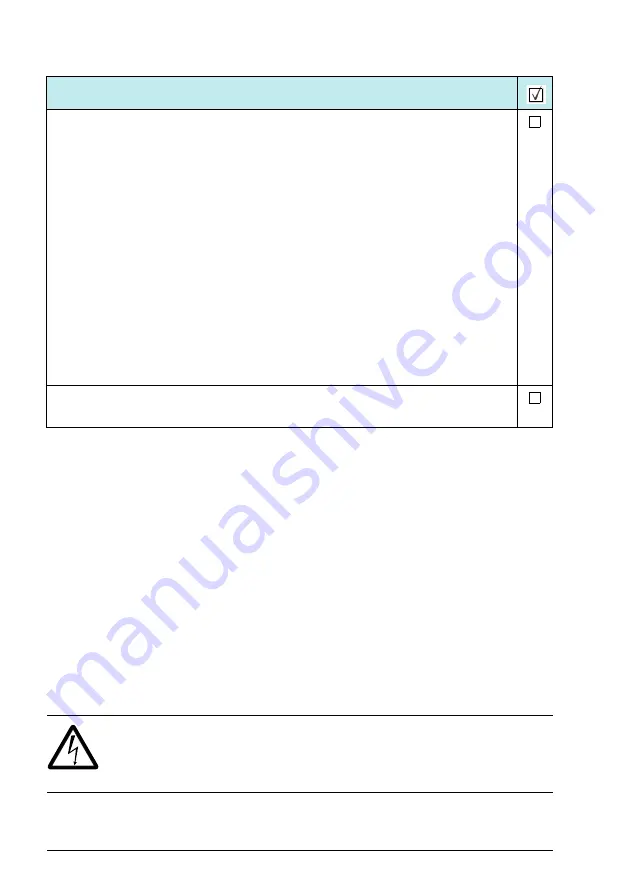
146 Safe torque off function
Use
1. Open the activation switch, or activate the safety functionality that is wired to the
STO connection.
2. The STO inputs of the drive control unit de-energize, and the drive control unit
cuts off the control voltage from the drive IGBTs.
3. The control program generates an indication as defined by parameter
31.22 STO
indication run/stop
.
4. The motor coasts to a stop (if running). The drive will not restart while the
activation switch or safety relay contacts are open.
5. Deactivate the STO by closing the activation switch, or resetting the safety
functionality that is wired to the STO connection.
6. Reset any faults before restarting.
WARNING!
The Safe torque off function does not disconnect the voltage of
the main and auxiliary circuits from the drive. Therefore maintenance work
on electrical parts of the drive or the motor can only be carried out after
isolating the drive from the main supply.
Test the operation of the failure detection of the drive. The motor can be stopped or
running.
• Open the 1st channel of the STO circuit (wire coming to S1). If the motor was
running, it should coast to a stop. The drive generates a
FA81 Safe torque off 1 loss
fault indication (see the firmware manual).
• Give a start command to verify that the STO function blocks the inverter’s
operation. The motor should not start.
• Close the STO circuit.
• Reset any active faults. Restart the drive and check that the motor runs normally.
• Open the 2nd channel of the STO circuit (wire coming to S2). If the motor was
running, it should coast to a stop. The drive generates a
FA82 Safe torque off 2 loss
fault indication (see the firmware manual).
• Give a start command to verify that the STO function blocks the drive’s operation.
The motor should not start.
• Close the STO circuit.
• Reset any active faults. Restart the drive and check that the motor runs normally.
Document and sign the acceptance test report which verifies that the safety function is
safe and accepted for operation.
Action
Summary of Contents for ACS380 Series
Page 1: ...ABB MACHINERY DRIVES ACS380 drives Hardware manual...
Page 4: ......
Page 12: ...12 Table of contents...
Page 20: ...20 Safety instructions...
Page 46: ...46 Mechanical installation...
Page 60: ...60 Planning the electrical installation...
Page 86: ...86 Maintenance...
Page 120: ...120 Technical data...
Page 122: ...122 Dimension drawings Frame R0 1 phase 230 V...
Page 123: ...Dimension drawings 123 Frame R0 400 V...
Page 124: ...124 Dimension drawings Frame R1 230 V...
Page 125: ...Dimension drawings 125 Frame R1 3 phase 230 V and 3 phase 400 V...
Page 126: ...126 Dimension drawings Frame R2 230 V...
Page 127: ...Dimension drawings 127 Frame R2 400 V...
Page 128: ...128 Dimension drawings Frame R3 400 V...
Page 129: ...Dimension drawings 129 Frame R4 400 V...
Page 130: ...130 Dimension drawings...
Page 138: ...138 Resistor braking...
Page 169: ...BTAC 02 pulse encoder interface module 169 Dimensions 3AXD50000031154 rev A...