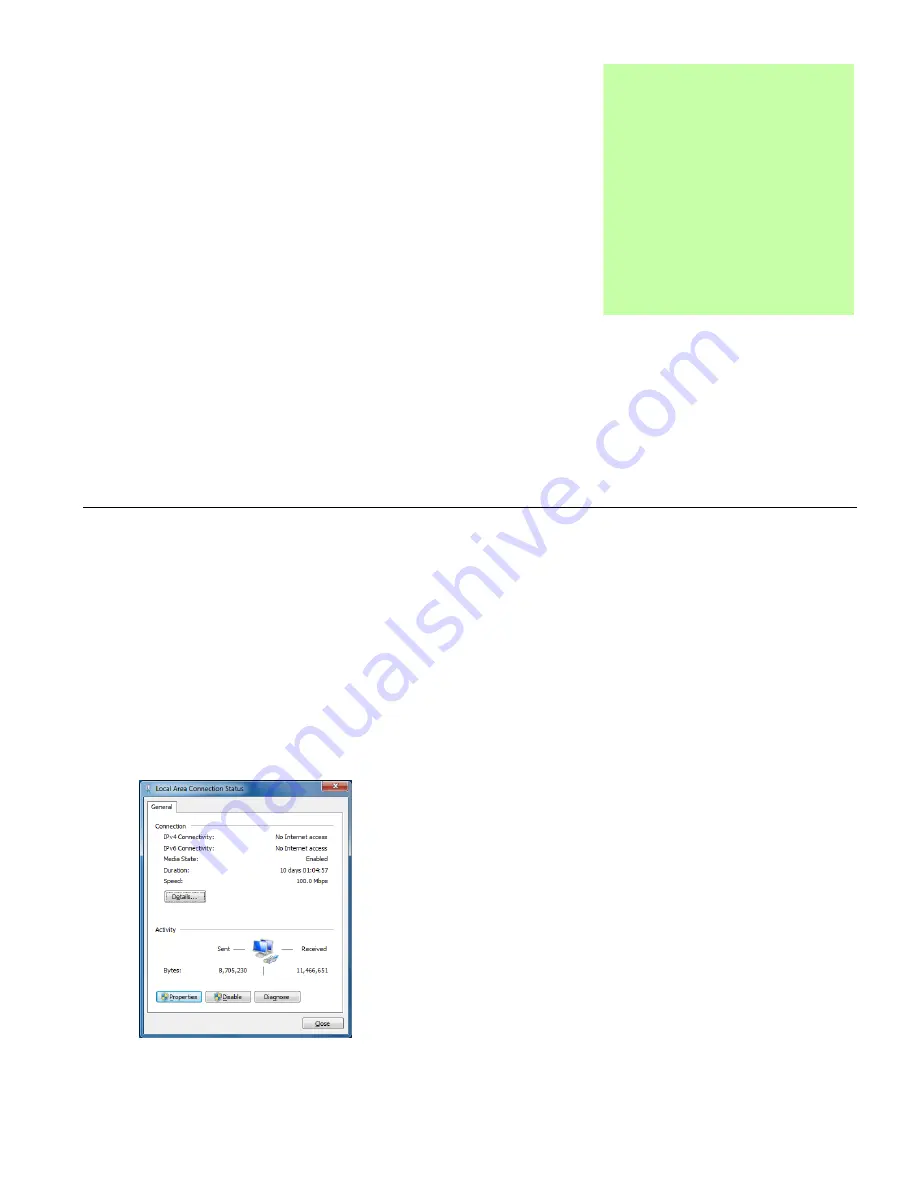
71
TIA portal
Contents of this chapter
This chapter provides the examples for configuring S7-300 and S7-1200 series PLC. You can configure
S7-300, S7-400, S7-1200 and S7-1500 series PLC using TIA portal.
Configuring PC IP address
To configure PC IP address, follow these steps:
Navigate to
Control Panel
→
Network and Sharing Center
→
Local Area Connection
in the PC.
1. In the Local Area Connection Status window, click
Properties
.
Figure 48 LAC
4