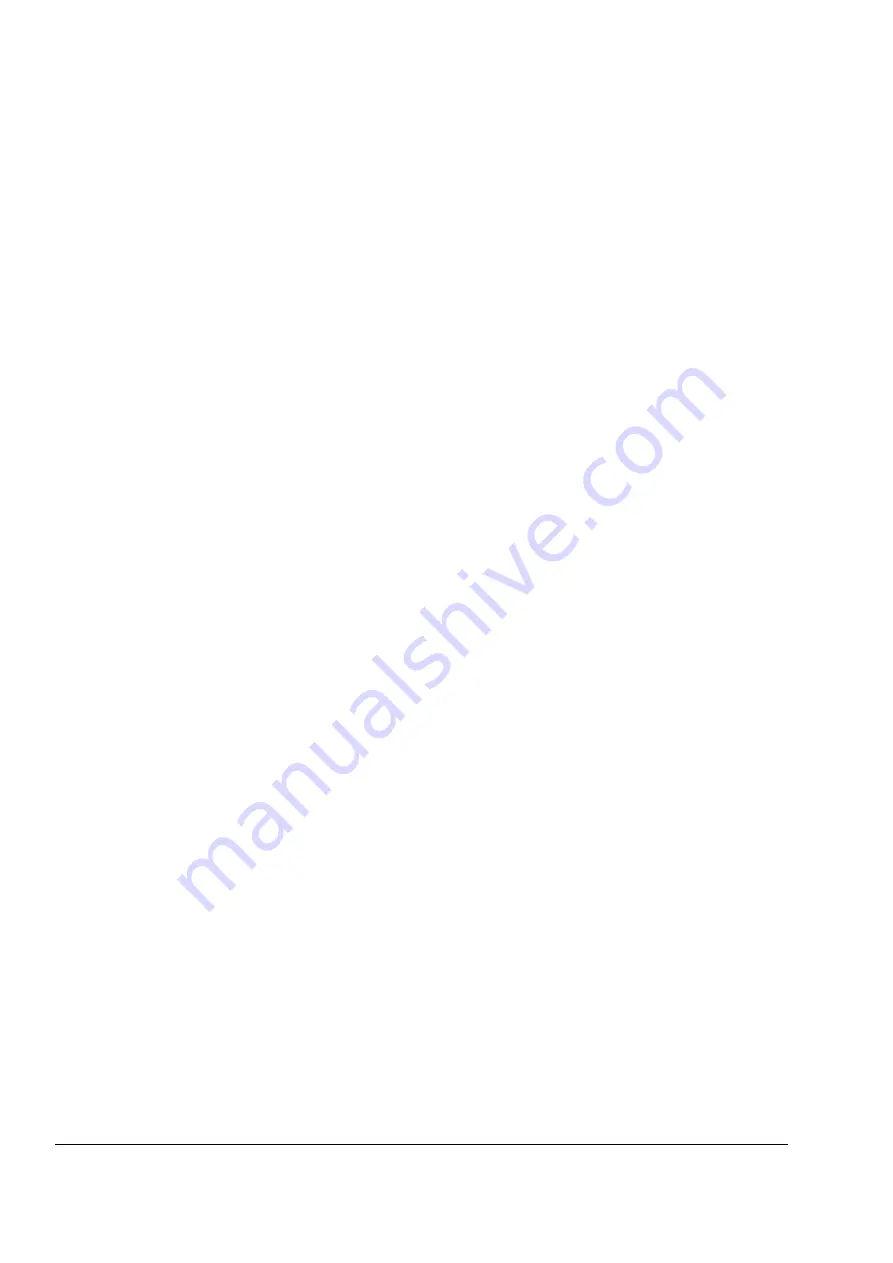
Program features
98
Speed reference scaling between the Master and the Follower
When a Master/Follower and Synchro control application is used, the Follower
usually needs to have a speed buffer for correcting the position error between the
Master and the Follower. The Follower speed buffer needs to have +5 or +10%
higher speed limit settings than the Master.
Example:
The Follower’s speed buffer is 200 rpm more than the Master’s.
Master using AI1/Joystick in EXT2
Follower using COMM REF in EXT2
Master minimum and maximum limit speed =
1700 rpm
Follower minimum and maximum limit speed =
1700 rpm
Master sends out -20000 & +20000 on
COMM REF
Follower receives -20000 & +20000 on
COMM REF
Master parameter
SCALE AI1 = 88%
(1500 rpm/1700 rpm = 88%)
Master using 88% of limit speed 1700 rpm as
maximum reference
Follower receives 1500 rpm and has a speed
buffer of 200 rpm
Summary of Contents for ACS 800 Series
Page 1: ...ACS800 Firmware Manual Crane Control Program N697 ...
Page 4: ......
Page 26: ...Start up and control through the I O interface 26 ...
Page 36: ...Quick start up guide 36 ...
Page 52: ...Control panel 52 ...
Page 105: ...Program features 105 Figure Control diagram for Shaft synchronisation executed in 20 ms ...
Page 128: ...Program features 128 ...
Page 150: ...Application macros control location EXT1 EXT2 150 ...
Page 228: ...Actual signals and parameters 228 ...
Page 299: ...Adaptive Programming examples for crane control 299 ...
Page 305: ...Adaptive Programming examples for crane control 305 ...
Page 318: ...Analogue Extension Module 318 ...
Page 332: ...Additional data actual signals and parameters 332 ...
Page 334: ...DriveWindow 334 ...
Page 335: ...Control block diagrams 335 Control block diagrams ...
Page 336: ...Control block diagrams 336 ...
Page 337: ...Control block diagrams 337 ...
Page 338: ...Control block diagrams 338 ...
Page 340: ...www abb com drives www abb com drivespartners Contact us 3AFE68775230 Rev E EN 2012 09 25 ...