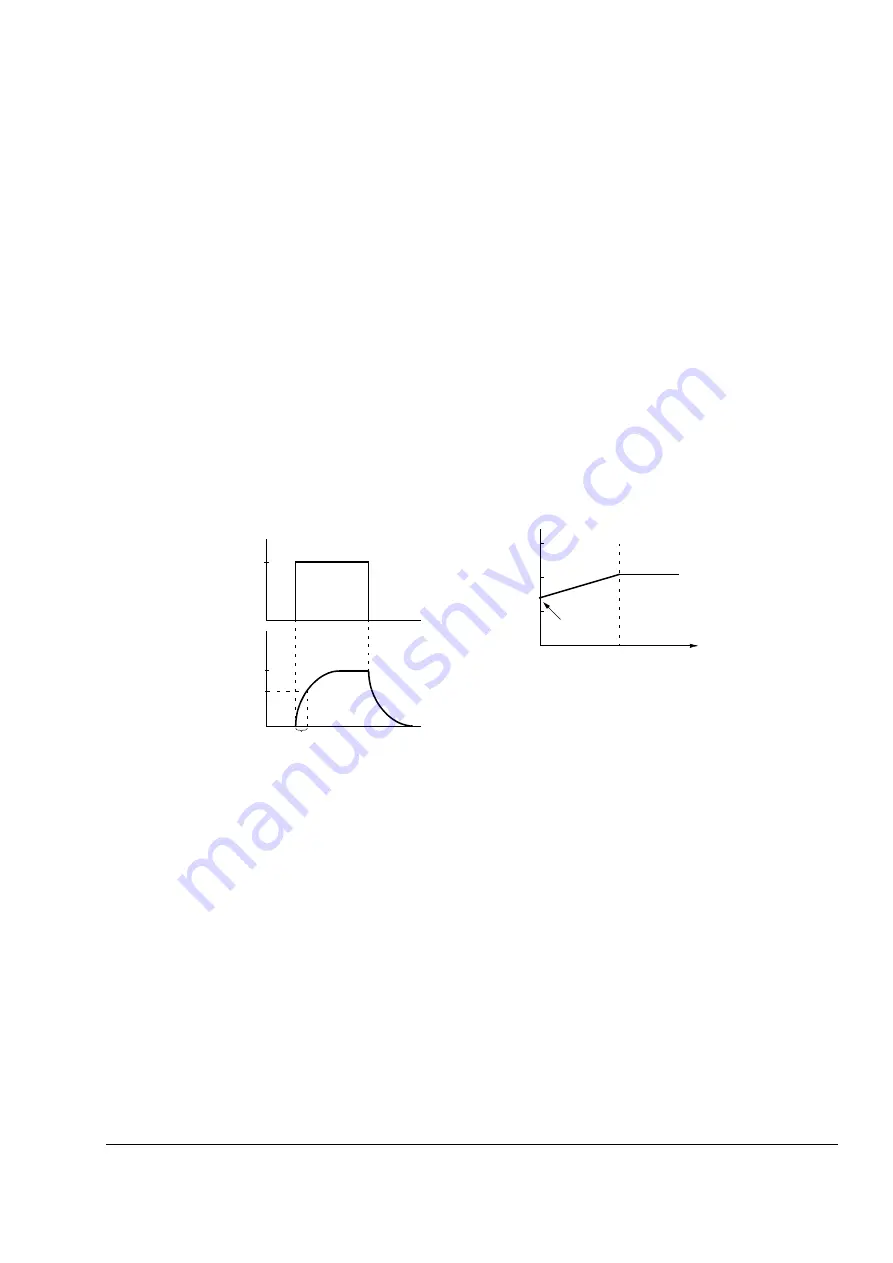
Program features
75
Motor thermal protection
The motor can be protected against overheating by activating the Motor thermal
protection function and by selecting one of the Motor thermal protection modes
available.
The Motor thermal protection modes are based either on a motor temperature
thermal model or on an overtemperature indication from a motor thermistor.
Motor temperature thermal model
The drive calculates the temperature of the motor on the basis of the following
assumptions:
1) The motor is at the estimated temperature (value of
MOTOR TEMP EST
saved at power switch off) when power is applied to the drive. When power is
applied for the first time, the motor is at the ambient temperature (30 °C).
2) Motor temperature is calculated using either the user-adjustable or automatically
calculated motor thermal time and motor load curve (see the figures below). The
load curve should be adjusted in case the ambient temperature exceeds 30 °C.
Use of the motor thermistor
It is possible to detect motor overtemperature by connecting a motor thermistor
(PTC) between the +24 V DC voltage supply offered by the drive and digital input
DI6. In normal motor operation temperature, the thermistor resistance should be less
than 1.5 kohm (current 5 mA). The drive stops the motor and gives a fault indication
if the thermistor resistance exceeds 4 kohm
.
The installation must meet the
regulations for protecting against contact.
Settings
Parameters
.
Note:
It is also possible to use the motor temperature measurement function. See
Motor temperature measurement through the standard I/O interface
on
Motor temperature measurement through an analogue I/O extension
on
Motor
100%
Temp.
63%
Motor thermal time
t
t
100%
50
100
150
Zero speed load
Motor load curve
Break point
Motor
Speed
Load
Current
(%)
Rise
Summary of Contents for ACS 800 Series
Page 1: ...ACS800 Firmware Manual Crane Control Program N697 ...
Page 4: ......
Page 26: ...Start up and control through the I O interface 26 ...
Page 36: ...Quick start up guide 36 ...
Page 52: ...Control panel 52 ...
Page 105: ...Program features 105 Figure Control diagram for Shaft synchronisation executed in 20 ms ...
Page 128: ...Program features 128 ...
Page 150: ...Application macros control location EXT1 EXT2 150 ...
Page 228: ...Actual signals and parameters 228 ...
Page 299: ...Adaptive Programming examples for crane control 299 ...
Page 305: ...Adaptive Programming examples for crane control 305 ...
Page 318: ...Analogue Extension Module 318 ...
Page 332: ...Additional data actual signals and parameters 332 ...
Page 334: ...DriveWindow 334 ...
Page 335: ...Control block diagrams 335 Control block diagrams ...
Page 336: ...Control block diagrams 336 ...
Page 337: ...Control block diagrams 337 ...
Page 338: ...Control block diagrams 338 ...
Page 340: ...www abb com drives www abb com drivespartners Contact us 3AFE68775230 Rev E EN 2012 09 25 ...