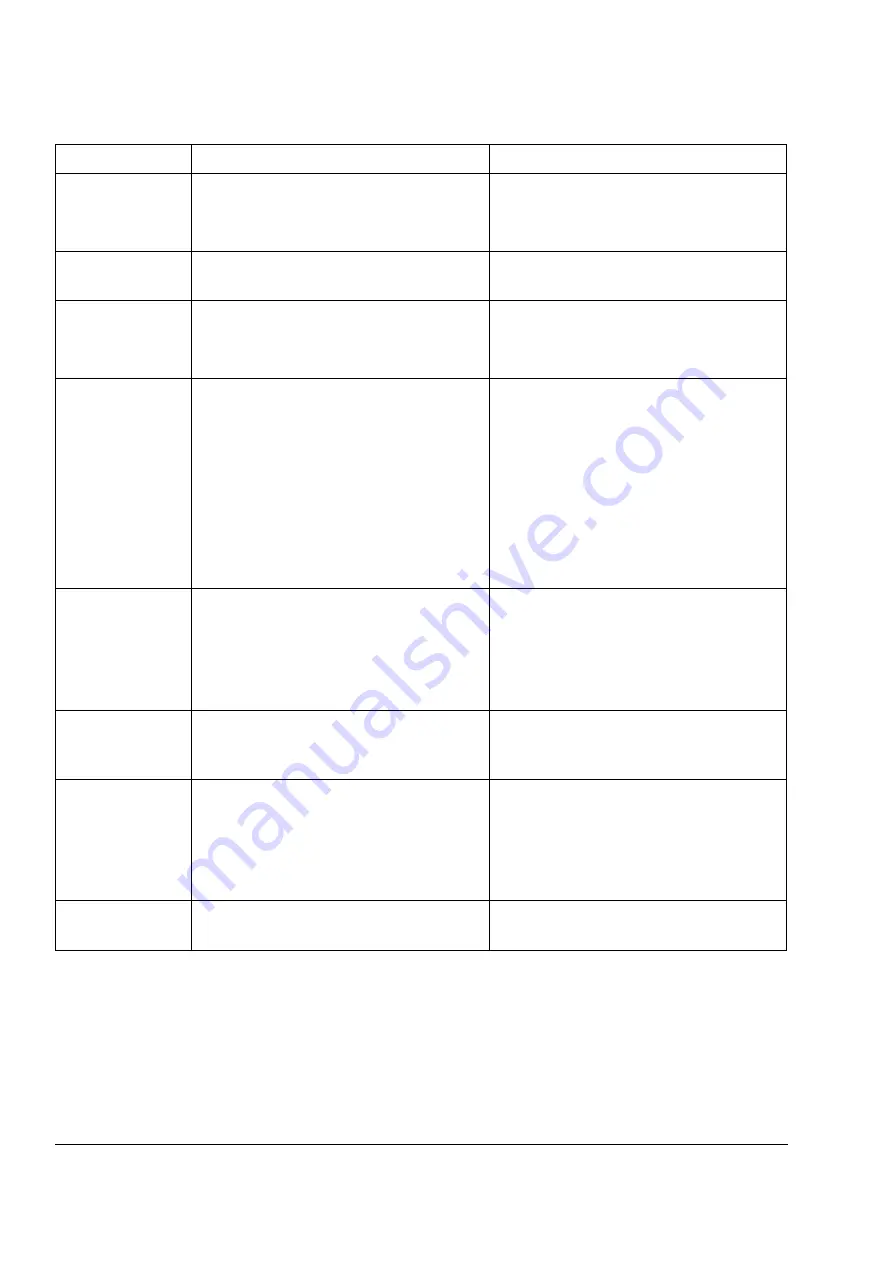
Fault tracing
286
START HIGH
(FFB3)
The Start command is active when the drive is
powered ON. The Start command remains ON
after a fault or fast stop has occurred and a
reset is done.
Start command should be made OFF and then
can be made ON for a start sequence.
START INTERL
(FF8D)
No Start Interlock signal received.
Check the circuit connected to the Start
Interlock input on the RMIO board.
SYNCRO SPEED
(FF87)
3.18 AW 5 bit 1
Value of motor nominal speed set to parameter
is not correct: Value is too near
synchronous speed of motor. Tolerance is
0.1%. This warning is active only in DTC mode.
Check nominal speed from motor rating plate
and set parameter
exactly accordingly.
TEMP DIF xx y
(4380)
4.01 FAULTED INT
INFO
Excessive temperature difference between
several parallel connected inverter modules.
xx (1...12) refers to inverter module number
and y refers to phase (U, V, W).
Alarm is indicated when temperature difference
is 15°C. Fault is indicated when temperature
difference is 20°C.
Excessive temperature can be caused, for
example, by unequal current sharing between
parallel-connected inverters.
Check cooling fan.
Replace fan.
Check air filters.
THERMISTOR
(4311)
3.08 AW 1 bit 2
(programmable
Fault Function
…
Motor temperature is excessive. Motor thermal
protection mode selection is THERMISTOR.
Check motor ratings and load.
Check start-up data.
Check thermistor connections to digital input
DI6.
T MEAS ALM
(FF91)
3.08 AW 1 bit 6
Motor temperature measurement is out of
acceptable range.
Check connections of motor temperature
measurement circuit. See chapter
for circuit diagram.
UNDERLOAD
(FF6A)
3.09 AW 2 bit 1
(programmable
Fault Function
Motor load is too low due to, For example,
release mechanism in driven equipment.
Check for problem in driven equipment.
Check Fault Function parameters.
ZERO POS WARN
(FFFB)
Start command with incorrect Zero position
input.
Check for Zero position DI.
WARNING
CAUSE
WHAT TO DO
Summary of Contents for ACS 800 Series
Page 1: ...ACS800 Firmware Manual Crane Control Program N697 ...
Page 4: ......
Page 26: ...Start up and control through the I O interface 26 ...
Page 36: ...Quick start up guide 36 ...
Page 52: ...Control panel 52 ...
Page 105: ...Program features 105 Figure Control diagram for Shaft synchronisation executed in 20 ms ...
Page 128: ...Program features 128 ...
Page 150: ...Application macros control location EXT1 EXT2 150 ...
Page 228: ...Actual signals and parameters 228 ...
Page 299: ...Adaptive Programming examples for crane control 299 ...
Page 305: ...Adaptive Programming examples for crane control 305 ...
Page 318: ...Analogue Extension Module 318 ...
Page 332: ...Additional data actual signals and parameters 332 ...
Page 334: ...DriveWindow 334 ...
Page 335: ...Control block diagrams 335 Control block diagrams ...
Page 336: ...Control block diagrams 336 ...
Page 337: ...Control block diagrams 337 ...
Page 338: ...Control block diagrams 338 ...
Page 340: ...www abb com drives www abb com drivespartners Contact us 3AFE68775230 Rev E EN 2012 09 25 ...