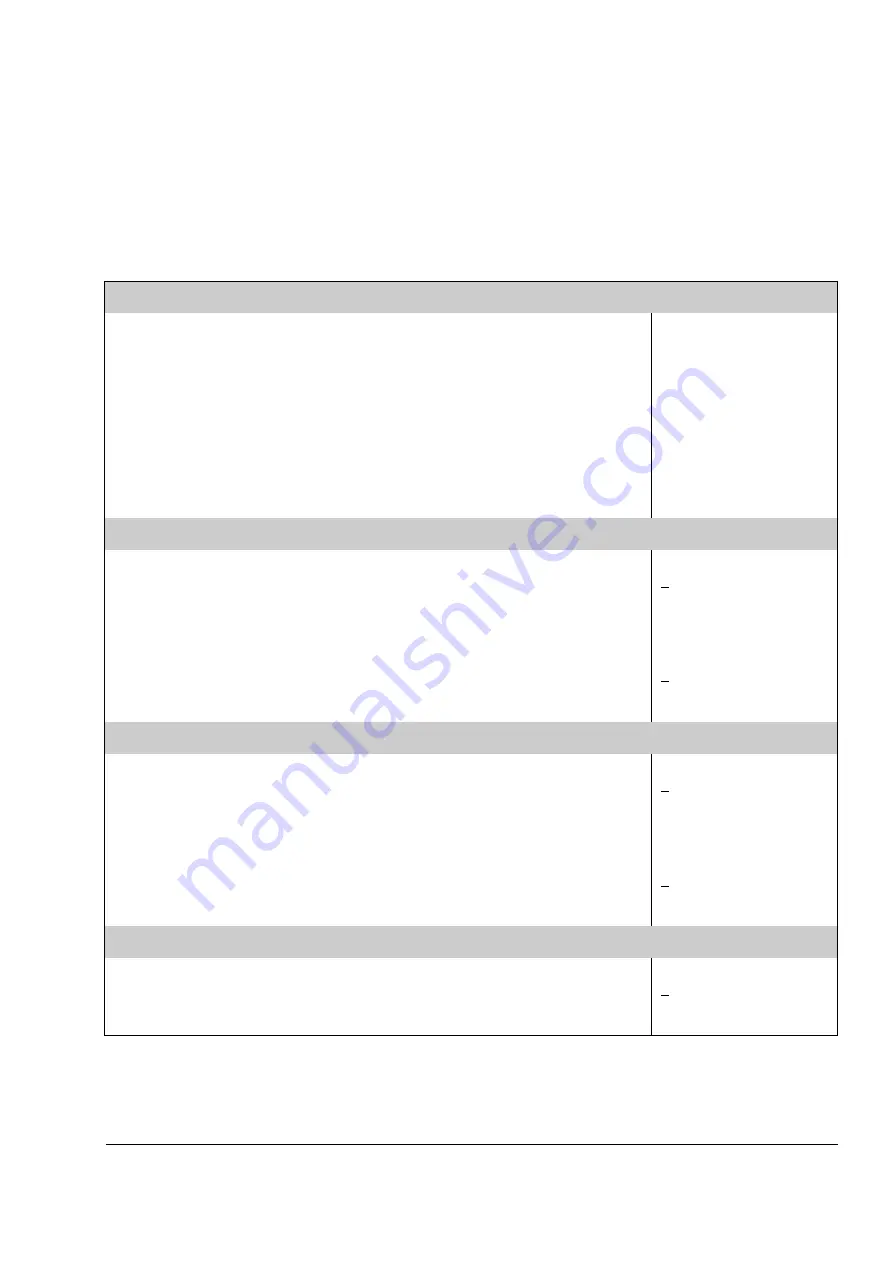
Start-up and control through the I/O interface
23
How to control the drive through the I/O interface
The table below instructs how to operate the drive through the digital and analogue
inputs when:
• the motor start-up is performed, and
• the default (Crane) parameter settings are valid.
PRELIMINARY SETTINGS
Ensure the Crane macro is active.
See parameter
.
The crane is normally operated in both the forward and reverse direction
and therefore the default setting of the parameter
Ensure that the control connections are wired according to the
connection diagram given for the Crane macro.
See chapter
macros, control location
EXT1/EXT2
Ensure that the drive is in external control. Press the
LOC/REM
key to
switch between external and local control.
In External control, there is
no L visible on the first row
of the panel display.
STARTING IN FORWARD DIRECTION AND CONTROLLING THE SPEED OF THE MOTOR
Start in the forward direction by switching the digital input DI1 ON. DI2
should be OFF.
Note:
The default setting for forward direction start digital input is DI1
and reverse direction start digital input is DI2.
1 -> 0.0 rpm I
FREQ 0.00 Hz
CURRENT 0.00 A
POWER 0.00 %
Regulate the speed by adjusting the voltage of the analogue input AI1.
1 -> 500.0 rpm I
FREQ 16.66 Hz
CURRENT 12.66 A
POWER 8.33 %
STARTING IN REVERSE DIRECTION AND CONTROLLING THE SPEED OF THE MOTOR
Start in the reverse direction by switching the digital input DI2 ON. DI1
should be OFF.
Note:
The default setting for reverse direction start digital input is DI2
and forward direction start digital input is DI1.
1 <- 0.0 rpm I
FREQ 0.00 Hz
CURRENT 0.00 A
POWER 0.00 %
Regulate the speed by adjusting the voltage of the analogue input AI1.
1 <- 500.0 rpm I
FREQ 16.66 Hz
CURRENT 12.66 A
POWER 8.33 %
STOPPING THE MOTOR
Switch OFF digital input DI1 if in forward condition, or DI2 if in reverse
condition.
1 -> 500.0 rpm O
FREQ 0.00 Hz
CURRENT 0.00 A
POWER 0.00 %
Summary of Contents for ACS 800 Series
Page 1: ...ACS800 Firmware Manual Crane Control Program N697 ...
Page 4: ......
Page 26: ...Start up and control through the I O interface 26 ...
Page 36: ...Quick start up guide 36 ...
Page 52: ...Control panel 52 ...
Page 105: ...Program features 105 Figure Control diagram for Shaft synchronisation executed in 20 ms ...
Page 128: ...Program features 128 ...
Page 150: ...Application macros control location EXT1 EXT2 150 ...
Page 228: ...Actual signals and parameters 228 ...
Page 299: ...Adaptive Programming examples for crane control 299 ...
Page 305: ...Adaptive Programming examples for crane control 305 ...
Page 318: ...Analogue Extension Module 318 ...
Page 332: ...Additional data actual signals and parameters 332 ...
Page 334: ...DriveWindow 334 ...
Page 335: ...Control block diagrams 335 Control block diagrams ...
Page 336: ...Control block diagrams 336 ...
Page 337: ...Control block diagrams 337 ...
Page 338: ...Control block diagrams 338 ...
Page 340: ...www abb com drives www abb com drivespartners Contact us 3AFE68775230 Rev E EN 2012 09 25 ...