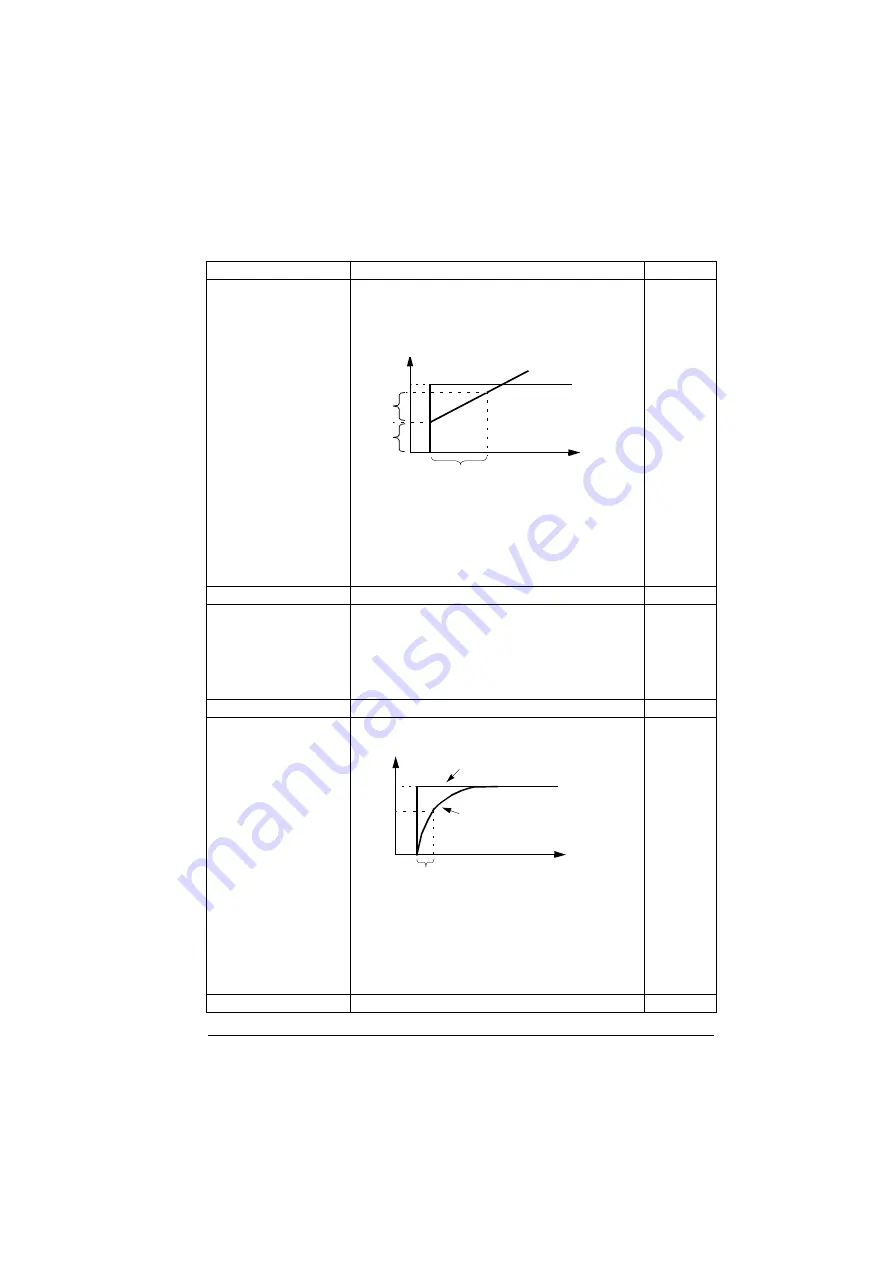
Parameters 221
Defines the integration time for the process PID controller.
This time needs to be set to the same order of magnitude as
the reaction time of the process being controlled, otherwise
instability will result.
Note:
Setting this value to 0 disables the “I” part, turning the
PID controller into a PD controller.
10.0 s
0.0…9999.0 s
Integration time.
1 = 1 s
Defines the derivation time of the process PID controller. The
derivative component at the controller output is calculated on
basis of two consecutive error values (E
K-1
and E
K
) according
to the following formula:
PID DERIV TIME × (E
K
- E
K-1
)/
T
S
, in which
T
S
= 2 ms sample time
E = Error = Process reference - process feedback.
0.000 s
0.000…10.000 s
Derivation time.
1000 = 1 s
Defines the time constant of the 1-pole filter used to smooth
the derivative component of the process PID controller.
0.0 s
0.0…10.0 s
Filter time constant.
10 = 1 s
No.
Name/Value
Description
Def/FbEq16
Ti
O
I
G × I
G × I
I = controller input (error)
O = controller output
G = gain
Ti = integration time
Time
Error/Controller output
63
%
100
T
t
O = I × (1 - e
-t
/T
)
I = filter input (step)
O = filter output
t
= time
T = filter time constant
Unfiltered signal
Filtered signal
Summary of Contents for ACQ580
Page 1: ...ABB drives for water Firmware manual ACQ580 pump control program ...
Page 4: ... 2017 ABB Oy All Rights Reserved 3AXD50000035867 Rev C EN EFFECTIVE 2017 06 21 ...
Page 30: ...26 Start up control with I O and ID run ...
Page 40: ...36 Default configuration ...
Page 304: ...300 Parameters ...
Page 340: ...336 Additional parameter data ...