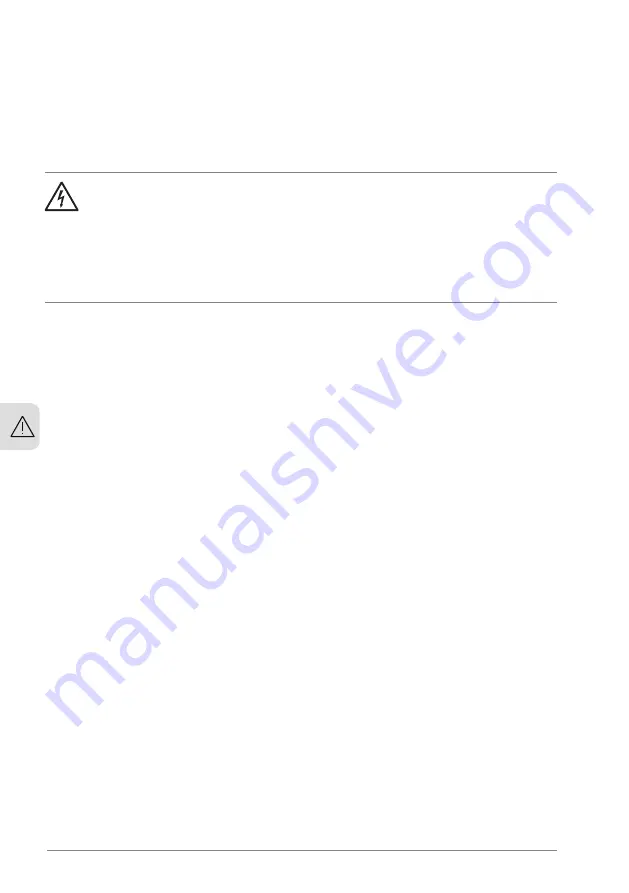
Electrical safety in installation, start-up and maintenance
■
Electrical safety precautions
These electrical safety precautions are for all personnel who do work on the drive,
motor cable or motor.
WARNING!
Obey these instructions. If you ignore them, injury or death, or damage to
the equipment can occur.
If you are not a qualified electrical professional, do not do installation or
maintenance work.
Do these steps before you begin any installation or maintenance work.
1.
Clearly identify the work location and equipment.
2.
Disconnect all possible voltage sources. Make sure that re-connection is not
possible. Lock out and tag out.
•
Open the main disconnecting device of the drive.
•
If you have a permanent magnet motor connected to the drive, disconnect
the motor from the drive with a safety switch or by other means.
•
Disconnect all dangerous external voltages from the control circuits.
•
After you disconnect power from the drive, always wait 5 minutes to let
the intermediate circuit capacitors discharge before you continue.
3.
Protect any other energized parts in the work location against contact.
4. Take special precautions when close to bare conductors.
5. Measure that the installation is de-energized. Use a quality voltage tester.
Before and after measuring the installation, verify the operation of the
voltage tester on a known voltage source.
•
•
Make sure that the voltage between the drive input power terminals (L1,
L2, L3) and the grounding (PE) busbar is zero.
•
Make sure that the voltage between the drive output terminals (T1/U, T2/V,
T3/W) and the grounding (PE) busbar is zero.
Important! Repeat the measurement also with the DC voltage setting of
the tester. Measure between each phase and ground. There is a risk of
dangerous DC voltage charging due to leakage capacitances of the motor
circuit. This voltage can remain charged for a long time after the drive
power-off. The measurement discharges the voltage.
•
Make sure that the voltage between the drive DC terminals (UDC+ and
UDC-) and the grounding (PE) terminal is zero.
Note: If cables are not connected to the drive DC terminals, measuring the
voltage from the DC terminal screws can give incorrect results.
20 Safety instructions
3
Summary of Contents for ACH580-31
Page 1: ... ABB INDUSTRIAL DRIVES ACH580 31 drives Hardware manual ...
Page 2: ......
Page 4: ......
Page 16: ...16 ...
Page 30: ...30 ...
Page 39: ...Operation principle 39 ...
Page 56: ...56 ...
Page 90: ...90 ...
Page 112: ...R3 1 7 N m 112 Electrical installation IEC ...
Page 113: ...R6 1 7 N m Electrical installation IEC 113 ...
Page 114: ...R8 1 7 N m 114 Electrical installation IEC ...
Page 130: ...R3 Max 250 mA 130 Electrical installation North America NEC ...
Page 131: ...R6 Electrical installation North America NEC 131 ...
Page 150: ...150 ...
Page 152: ...152 ...
Page 166: ... Fan arrow must point up 166 Maintenance ...
Page 212: ...212 ...
Page 214: ...R3 IP21 UL Type 1 3AXD50000028643 214 Dimension drawings ...
Page 215: ...R3 Option B056 IP55 UL Type 12 3AXD50000045321 Dimension drawings 215 ...
Page 216: ...R6 IP21 UL Type 1 3AXD50000037446 216 Dimension drawings ...
Page 217: ...R6 Option B056 IP55 UL Type 12 3AXD50000045351 Dimension drawings 217 ...
Page 218: ...R8 IP21 UL Type 1 3AXD50000147052 218 Dimension drawings ...
Page 219: ...R8 Option B056 IP55 UL Type 12 3AXD50000147052 Dimension drawings 219 ...
Page 220: ...220 ...
Page 242: ...242 ...
Page 250: ...250 ...
Page 254: ...254 ...
Page 262: ...262 ...
Page 268: ...268 ...
Page 275: ...CMOD 01 multifunction extension module external 24 V AC DC and digital I O 275 ...
Page 276: ...276 ...
Page 282: ...282 CMOD 02 multifunction extension module external 24 V AC DC and isolated PTC interface ...