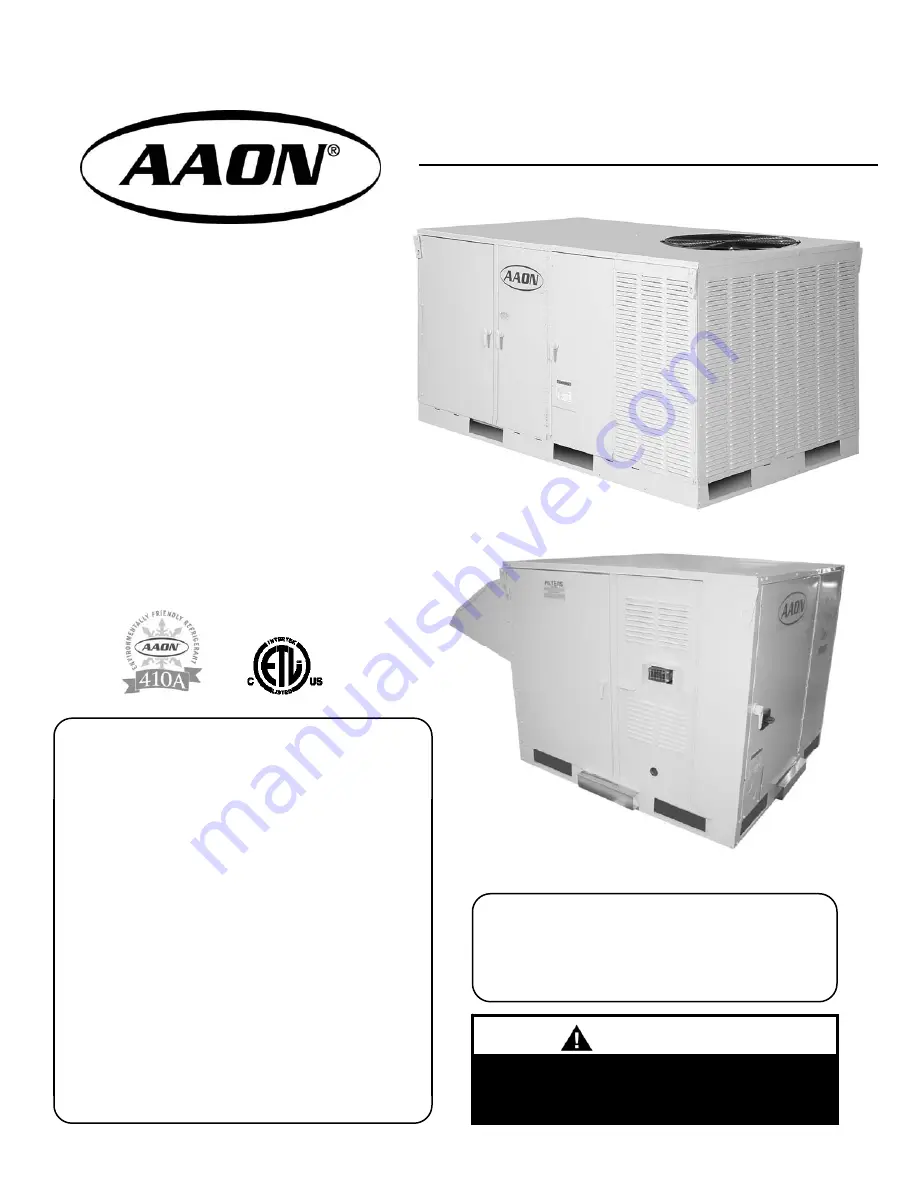
Installation and User Manual
HB
Series
DO NOT STORE OR USE GASOLINE OR OTHER
FLAMMABLE VAPORS AND LIQUIDS IN THE
VICINITY OF THIS OR ANY OTHER APPLIANCE.
FOR YOUR SAFETY
WHAT TO DO IF YOU SMELL GAS
FOR YOUR SAFETY
•
EXTINGUISH ANY OPEN FLAME
•
DO NOT TOUCH ANY ELECTRICAL SWITCH
•
DO NOT TRY TO LIGHT ANY APPLIANCE
•
DO NOT USE ANY PHONE IN YOUR BUILDING
•
IMMEDIATELY CALL YOUR GAS SUPPLIER
FROM A NEIGHBOR’S PHONE. FOLLOW THE
GAS SUPPLIER’S INSTRUCTIONS.
•
IF YOU CANNOT REACH YOUR GAS
SUPPLIER, CALL THE FIRE DEPARTMENT.
If the information in this manual is not followed
exactly, a fire or explosion may result causing
property damage, personal injury, or loss of life.
WARNING
Package Units
& Air Handlers
R-410A Package
Air Handler
•
R-410A DX or Chilled Water Cooling
•
Gas, Electric or Hot Water Heat
•
Bottom or Side Discharge
Summary of Contents for HB Series
Page 18: ...18 Figure 18a External Control Inputs to Control Board ...
Page 20: ...20 Figure 20a Reheated Supply Air Temperature ...
Page 29: ...29 ...
Page 30: ...30 ...