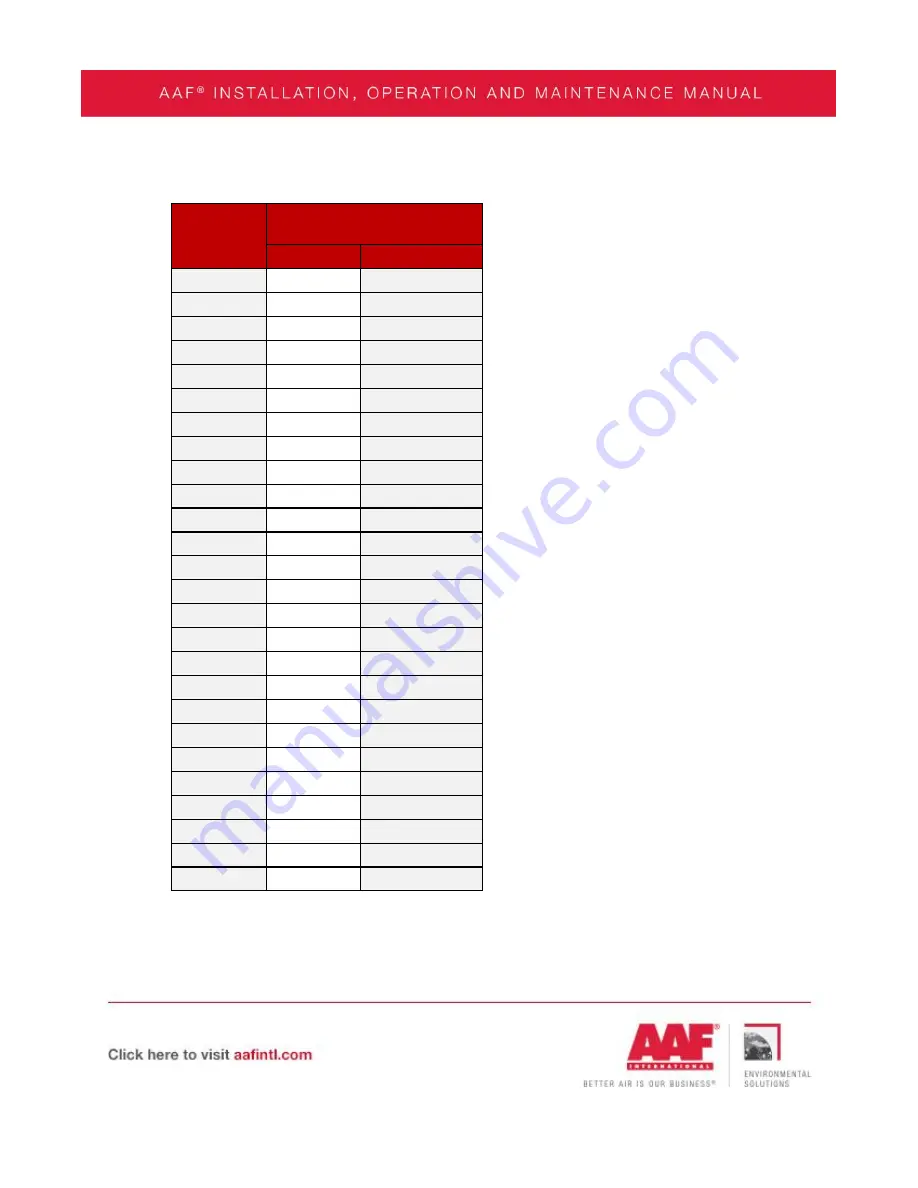
10
GDED-IOM-215-A
3.2
Weights
Model
Approx. Shipping
Weight
Note: The table is for guidance only.
The collector delivered may vary,
according to a number of factors
such as addition of accessories,
greater stiffening for NFPA models,
or where the unit is specially built
for applications where the system
pressure is greater than the
standard 20” w.g. design pressure is
anticipated.
lb.
kg
2RC4
1662
754
2RC8
1763
800
2RC16
2565
1164
2RC24
4328
2072
3RC6
1999
907
3RC12
2103
954
3RC24
3123
1417
3RC36
4205
1908
3RC48
5587
2535
3RC60
7328
3325
4RC16
2352
1067
4RC32
3683
1671
4RC48
4966
2253
4RC64
6564
2978
4RC80
8648
3924
4RC96
10,246
4649
4RC112
11,529
5231
5RC20
2721
1234
5RC40
5690
2581
5RC60
8480
3846
5RC80
11,334
5141
5RC100
14,170
6427
5RC120
17,024
7722
5RC140
19,813
8987
5RC160
22,668
10,282
5RC180
25,388
11,516
Summary of Contents for OptiFlo RC Series
Page 1: ...GDED IOM 215 A OptiFlo RC...