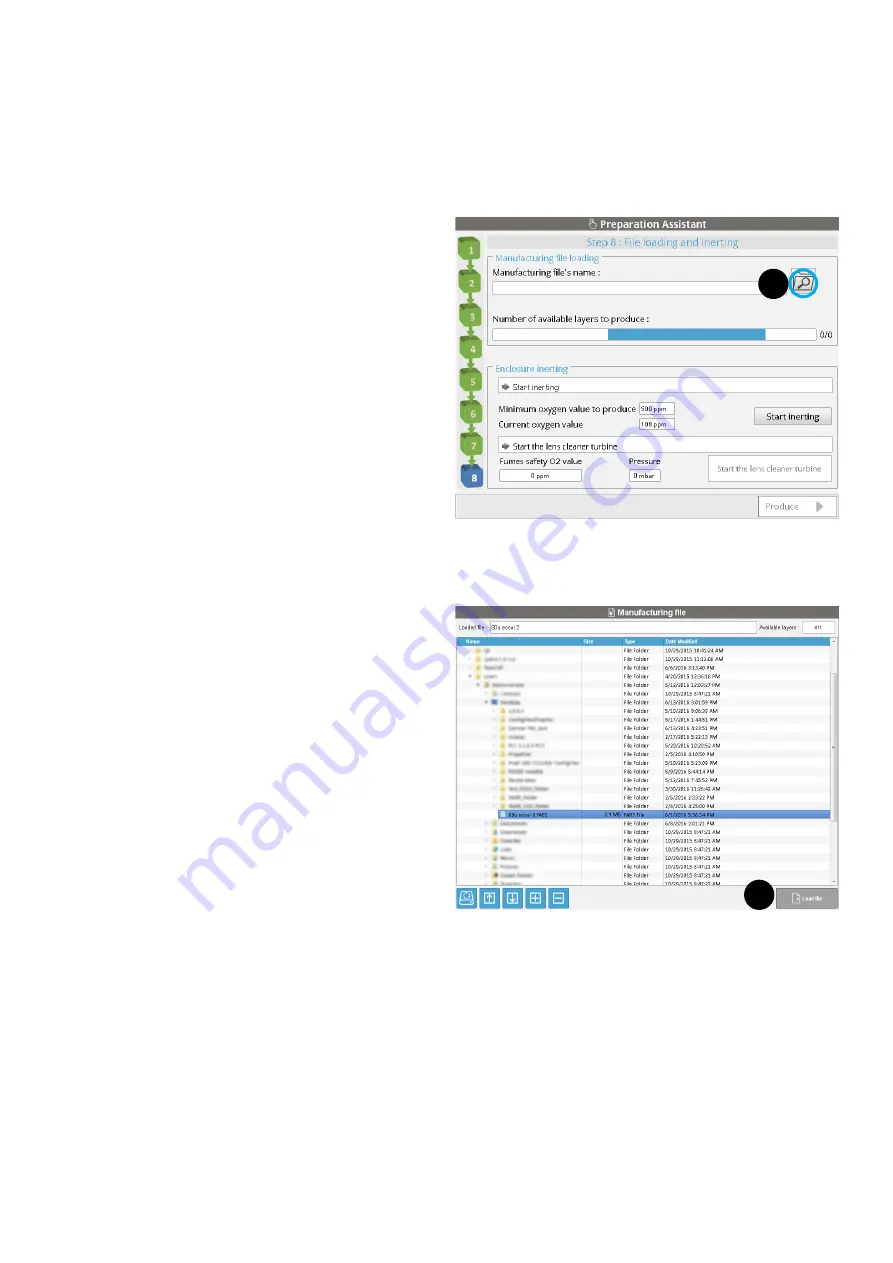
41
3D SYSTEMS, INC
.
Step 8 : Loading of the manufacturing file and inerting
This step consists of :
•
Selecting the manufacturing file (*.FAB3 format) created with
ProX DMP Manufacturing
, standalone software,
•
Inerting the manufacturing chamber and process filter.
Manufacturing file selection
1. Click on the folder icon to launch the file browser (1).
2. Select the manufacturing file and click on
Load file
(2).
The
Preparation Assistant
will then return to the previous page. The inerting phase should then be initiated.
2
1