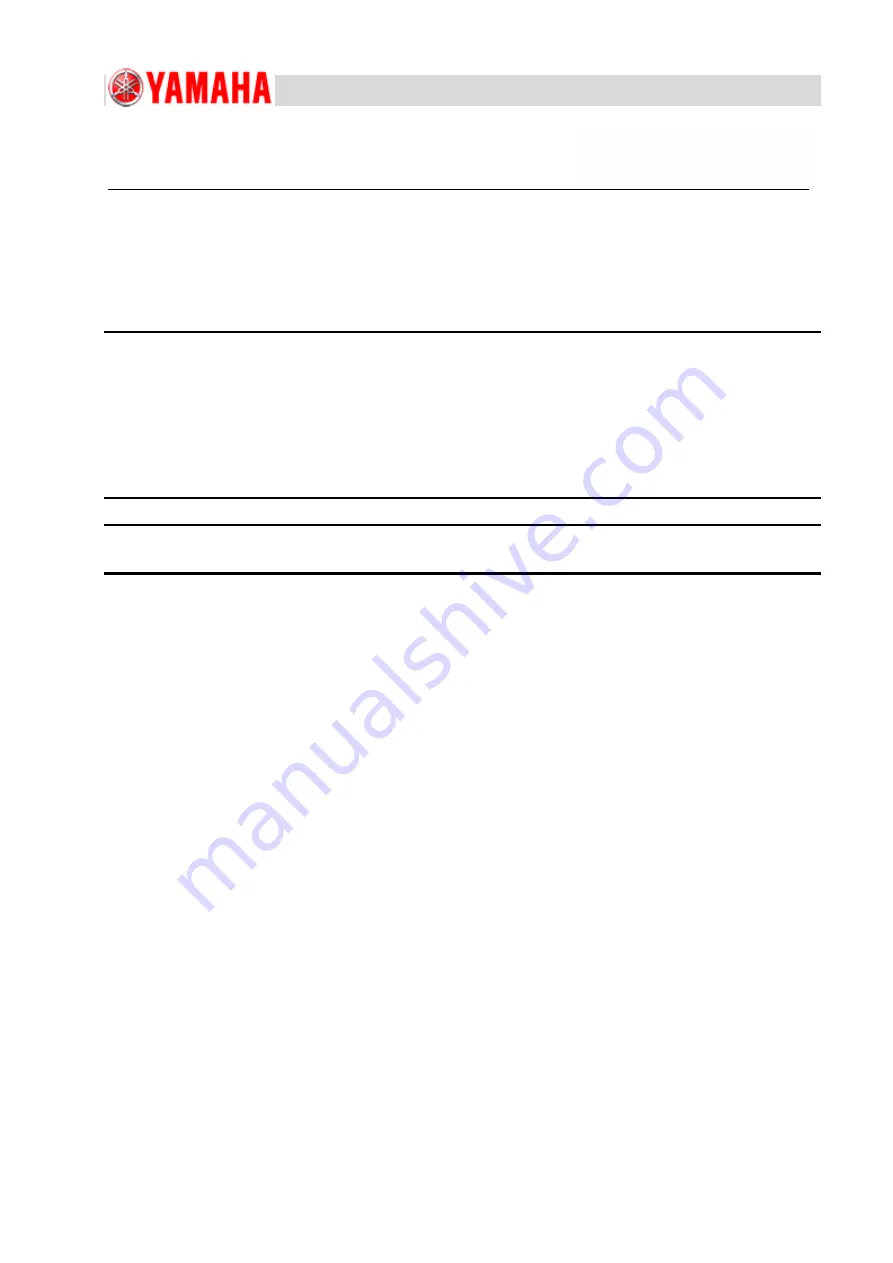
For Service Engineers
Service Information
1/120
SI1906002J-002 : YSP10 installation and adjustment procedures
MACHINE TYPE
:
YSP10
CLASSIFICATION :
Installation and Adjustment
REFERENCE
:
SI1004008E: General procedures for
carrying in and installing a machine
YSP10 installation and adjustment procedures
General description
This document describes how to carry in, install, and adjust YSP10.
About this document:
•
This document is intended for service engineers.
•
YAMAHA is not responsible for any problems caused by the misuse of the document.
•
This document contains the method to edit the system data that affects the customer’s machine
condition.
•
Make sure to thoroughly understand the contents of the document, and perform the adjustments on
your own responsibility.
About the safety:
Strictly follow the safety precautions in the “Safety” section in the “Operation Manual”.
Disclaimers:
This document contains the preliminary information subject to change in the future.
The information contained in this document represents the current view of YAMAHA on the issues discussed as of
the date of issuance. As YAMAHA must respond to changing market conditions, it should not be interpreted to be a
commitment on the part of YAMAHA, and YAMAHA cannot guarantee the accuracy of any information presented
after the date of issuance.
This document is provided for information purposes only, and it is provided without any warranties, either express or
implied.
It is the responsibility of the user to comply with all applicable copyright laws. Without limiting the rights under
copyright, no part of this document may be reproduced, stored in or introduced into a retrieval system, or transmitted
in any form or by any means (electronic, mechanical, photocopying, recording, or otherwise), or for any purpose,
without the written permission of YAMAHA.
However, this shall not be construed to limit the user’s right granted by Copyright law.
YAMAHA may have patents, patent applications, trademarks, copyrights, or other intellectual property rights
covering subject matter in this document. Except as expressly provided in any written license agreement from
YAMAHA, this document does not give users any license to these patents, trademarks, copyrights, or other
intellectual property.
The names of actual companies and products mentioned in this document may contain the trademarks of their
respective owners.
No: SI1906002E-002
ISSUED DATE: September 18, 2019
REVISED DATE: November 4, 2021