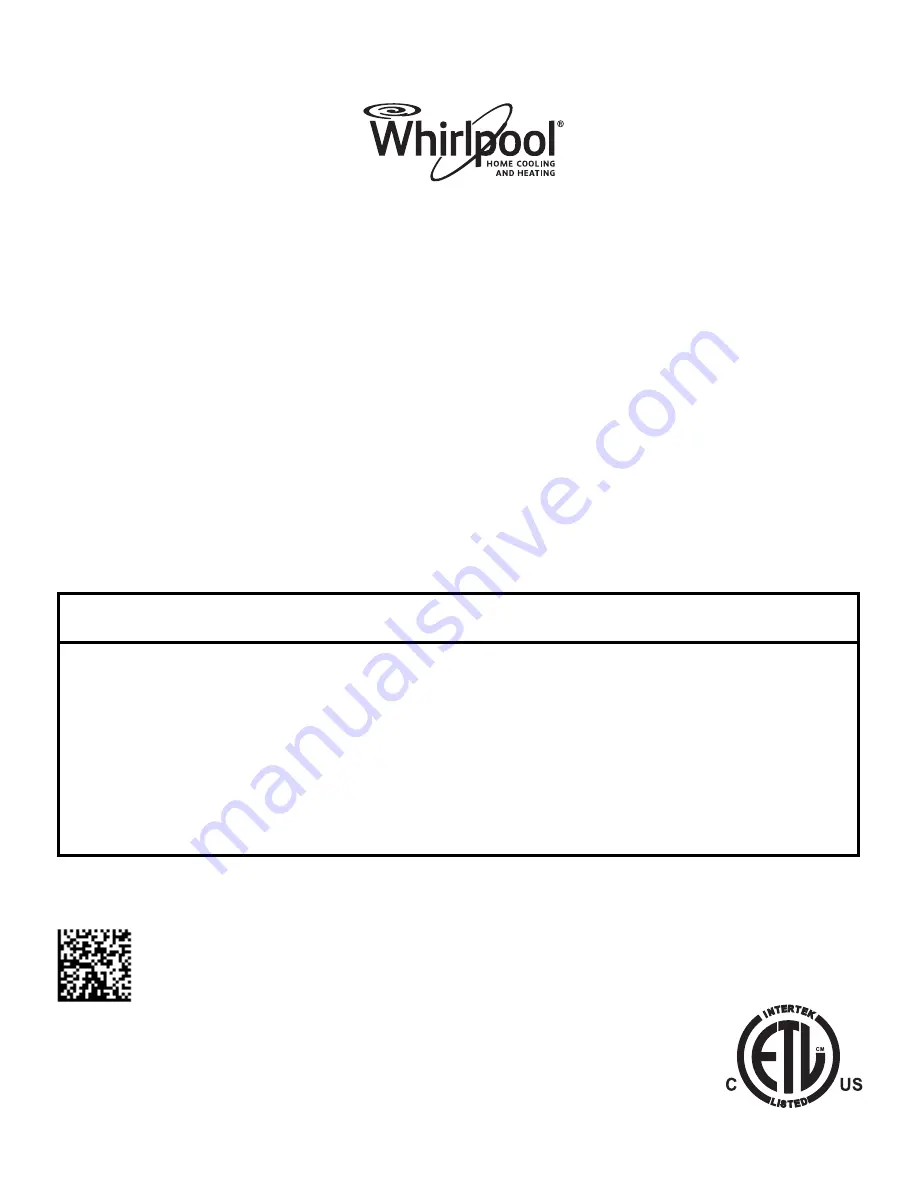
GAS-FIRED WARM AIR FURNACE INSTALLATION INSTRUCTIONS
(Type FSP Category IV Direct or Nondirect Vent Air Furnace)
These furnaces comply with requirements embodied in the
American National Standard/National Standard of Canada ANSI
Z21.47 CSA-2.3 Gas Fired Central Furnaces.
NOTE: Please contact your distributor or our website for
applicable Specification Sheet referred to in this manual.
WPIO-299N
Tradewinds Distributing Company, LLC
14610 Breakers Drive
Jacksonville, Florida 32258
Whirlpool Gold
®
Models
WGFM195, WFD195,
WFD193, WFM195
ATTENTION INSTALLATION PERSONNEL
As a professional installer, you have an obligation to know the product better than the customer. This includes all
safety precautions and related items. Prior to actual installation, thoroughly familiarize yourself with this instruction
manual. Pay special attention to all safety warnings. Often during installation or repair, it is possible to place
yourself in a position which is more hazardous than when the unit is in operations.
Remember, it is your responsibility to install the product safely and to know it well enough to be able to instruct a
customer in its safe use. Safety is a matter of common sense...a matter of thinking before acting. Most dealers have
a list of specific good safety practices...follow them.
The precautions listed in this installation manual are intended as supplemental to existing practices. However, if
there is a direct conflict between existing practices and the content of this manual, the precautions listed here take
precedence.
aceholder
for Bar
Code