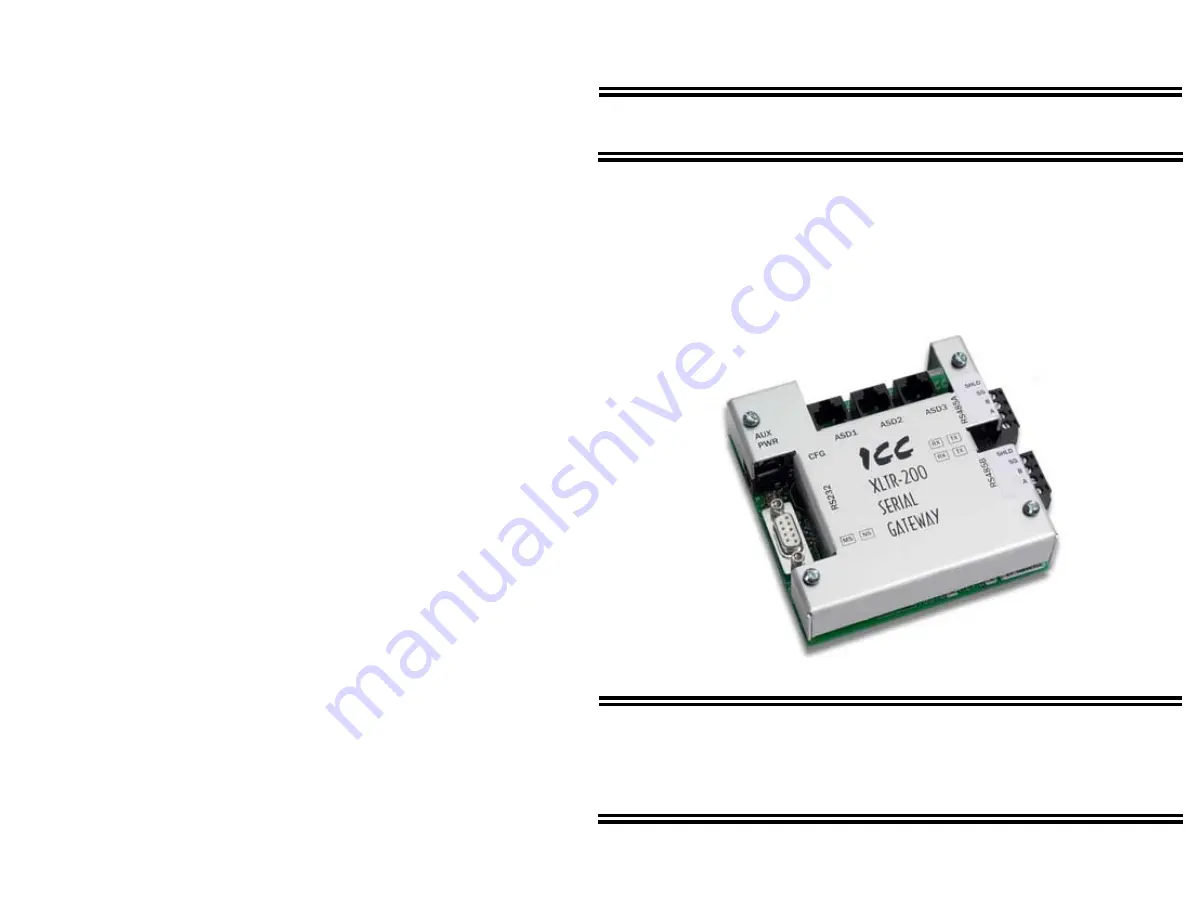
ICC
INDUSTRIAL CONTROL COMMUNICATIONS, INC.
Madison Office
Houston Office
1600 Aspen Commons, Suite 210
12300 Dundee Court, Suite 212
Middleton, WI USA 53562-4720
Cypress, TX USA 77429-8364
Tel: [608] 831-1255 Fax: [608] 831-2045
http://www.iccdesigns.com
Printed in U.S.A
NETWORK GATEWAY SERIES
ICC
INDUSTRIAL CONTROL COMMUNICATIONS, INC.
XLTR-200
SERIAL MULTIPROTOCOL NETWORK GATEWAY
September 2006
ICC #10604-1.101-000
Summary of Contents for XLTR-200
Page 98: ...97 15 Notes ...