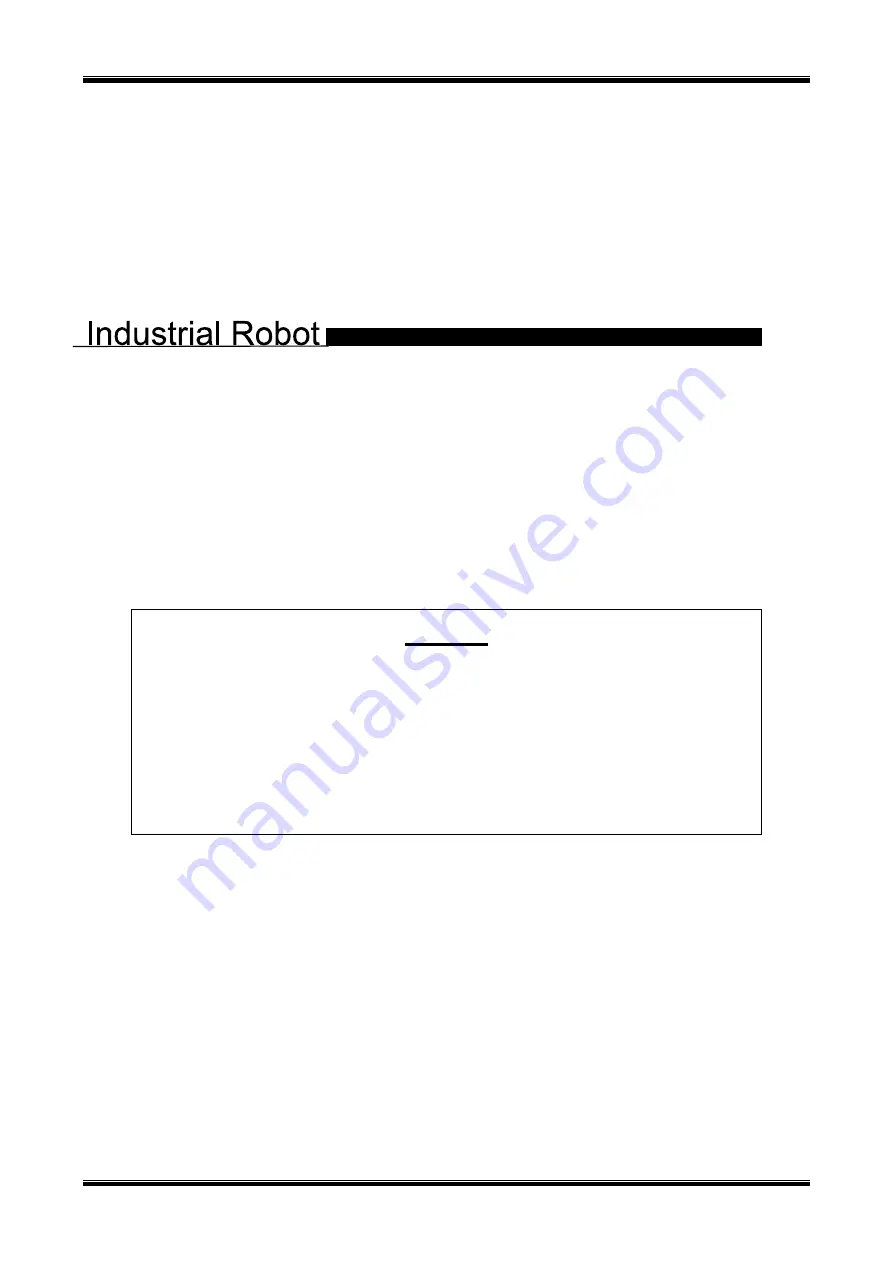
STE 85357-11
THL Series
INSTRUCTION MANUAL
MAINTENANCE MANUAL
Notice
1. Make sure that this instruction manual is delivered to the final
user of this product.
2. Before using this product, read through and completely
understand this manual.
3. After reading through this manual, keep it nearby for future
reference.
July, 2012
TOSHIBA MACHINE CO., LTD.
NUMAZU, JAPAN
Robot controller TSL3000
Robot controller TSL3000E
Robot controller TS3000
Robot controller TS3000E