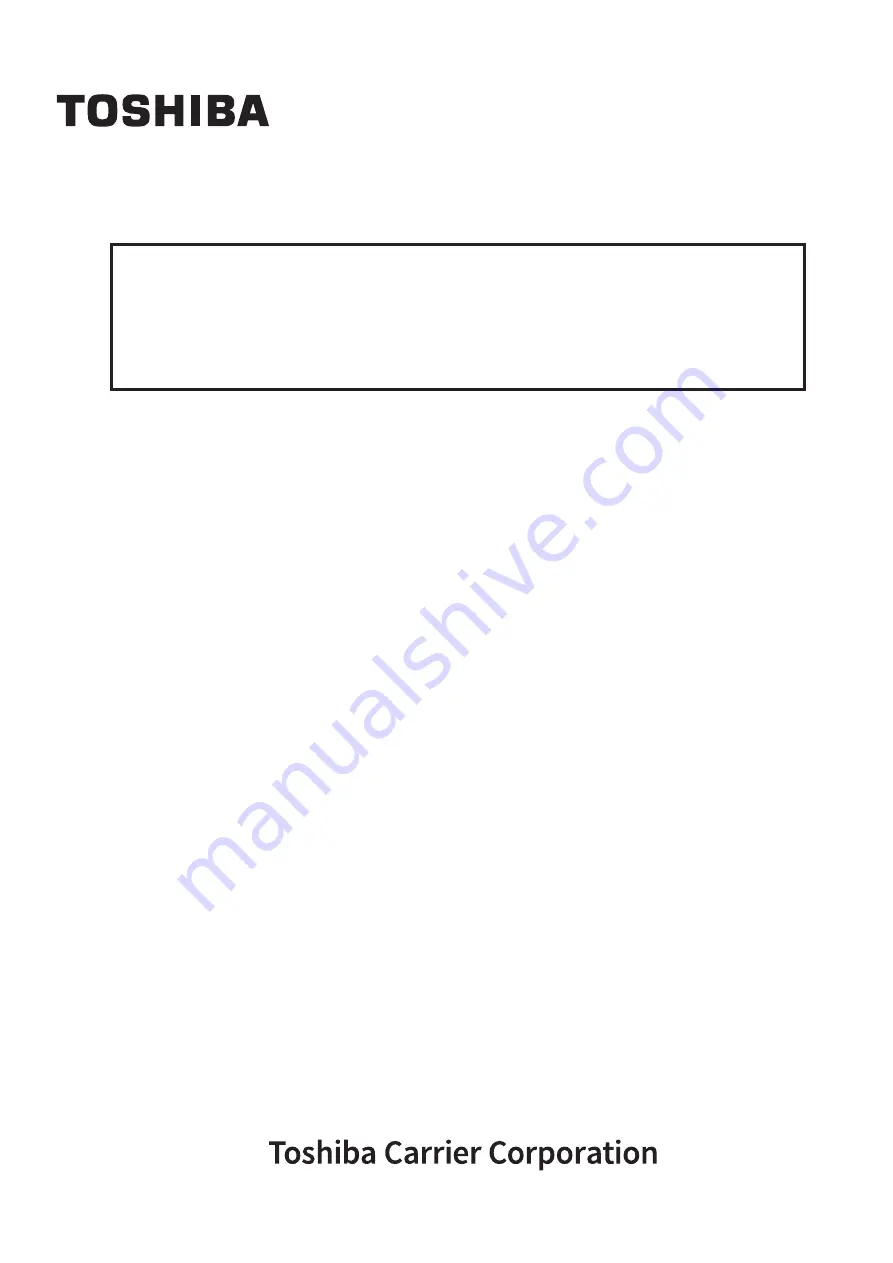
Original instructions
30KQA060-01ISE
Universal Smart
X
Safety Precautions
Original Owner’s Manual
Thank you very much for purchasing this Toshiba heat pump unit.
Please read this instruction manual carefully before using the unit. Be sure to obtain
the “Instruction manual” and “Installation manual” from constructor or dealer.
Request to constructor or dealer; Please clearly explain the contents of this
instruction manual and hand over it.
This unit is not intended for use by person (including children) with reduced
physical, sensory or mental capabilities, or lack of experience and knowledge,
unless they have been given supervision or instruction concerning use of the unit
by a person responsible for their safety.
Fluorocarbon must be recovered in accordance with the local laws and regulations
when the product is repaired or thrown away. Type and volume of refrigerant and
conversion values for CO
2
are listed.
Keep this manual after you finish reading it.
Please read carefully through these instructions that contain important information
which complies with the “Machinery Directive 2006/42/EC”, and ensure that you
understand them.
This unit is only for industrial uses. And this unit is not usable in residential use.
Air-Cooled Chiller
Model Name:
RUAGP Series