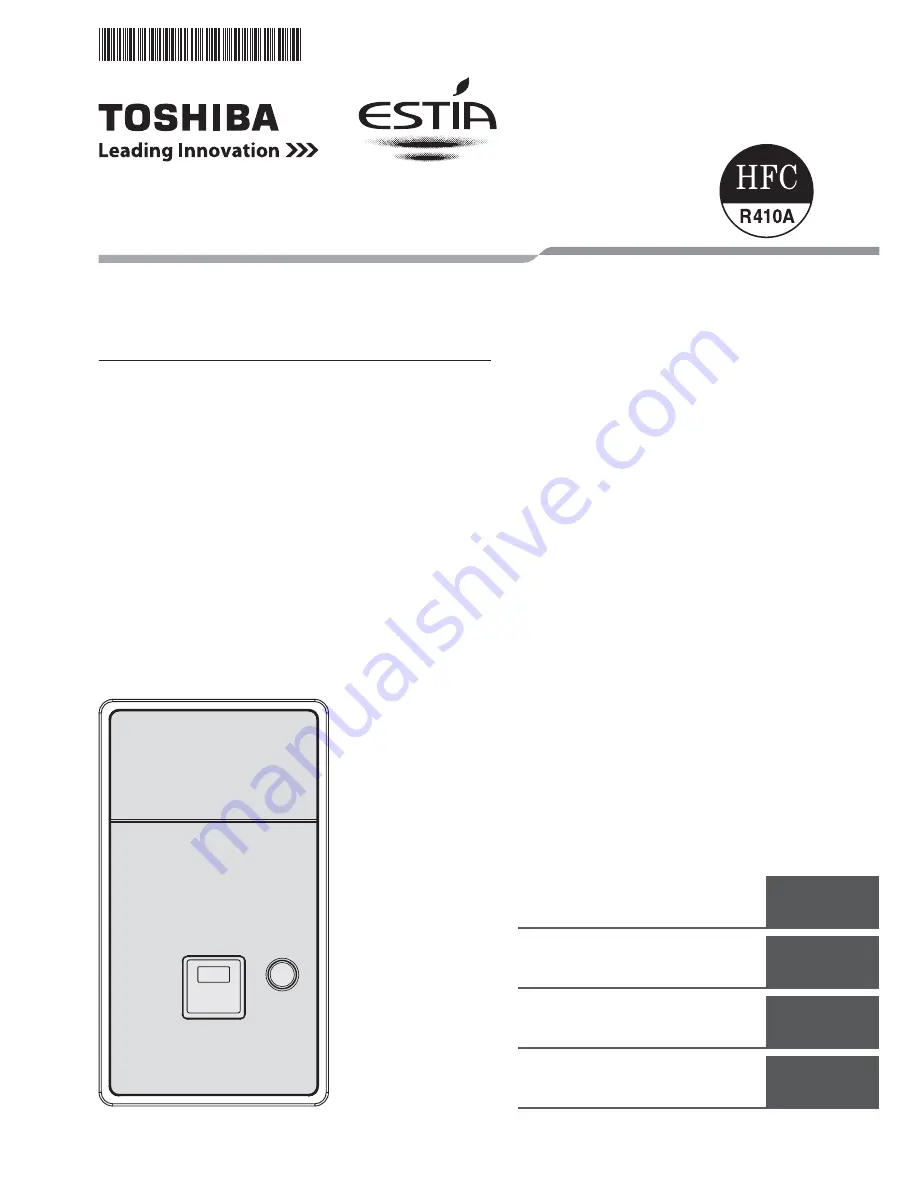
Installation manual
Hydro Unit
(Air to Water Heat Pump)
2
English
AIR TO WATER HEAT PUMP
Hydro Unit
Model name:
HWS-802XWHM3-E
HWS-802XWHT6-E
HWS-1402XWHM3-E
HWS-1402XWHT6-E
HWS-1402XWHT9-E
Manuel d’installation
Unité hydroélectrique
(Pompe à chaleur air/eau)
44
Français
Installations-handbuch
Hydrogerät
(Luft-Wasser-Wärmepumpe)
86
Deutsch
Installationshandbok
Hydroenhet
(Luft-till-vatten-värmepump)
128
Svenska
Installation manual
Summary of Contents for ESTIA HWS-1402XWHM3-E
Page 44: ...EF99804301 3 ...