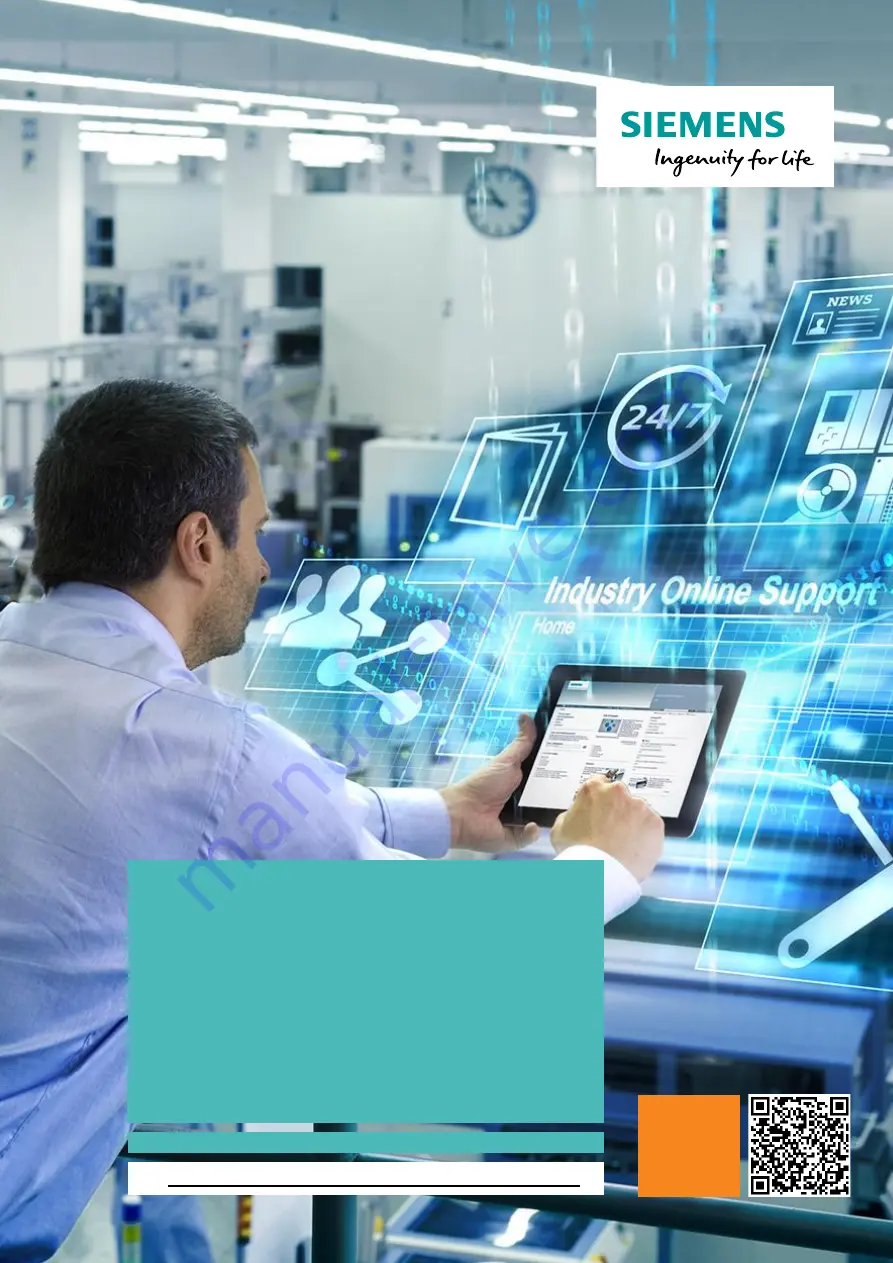
Prevention of pump
blockages by
changing the
direction of rotation
SIMOCODE pro V
https://support.industry.siemens.com/cs/ww/en/view/109478058
Siemens
Industry
Online
Support
Prevention of pump
blockages by
changing the
direction of rotation
SIMOCODE pro V
https://support.industry.siemens.com/cs/ww/en/view/109478058
Siemens
Industry
Online
Support