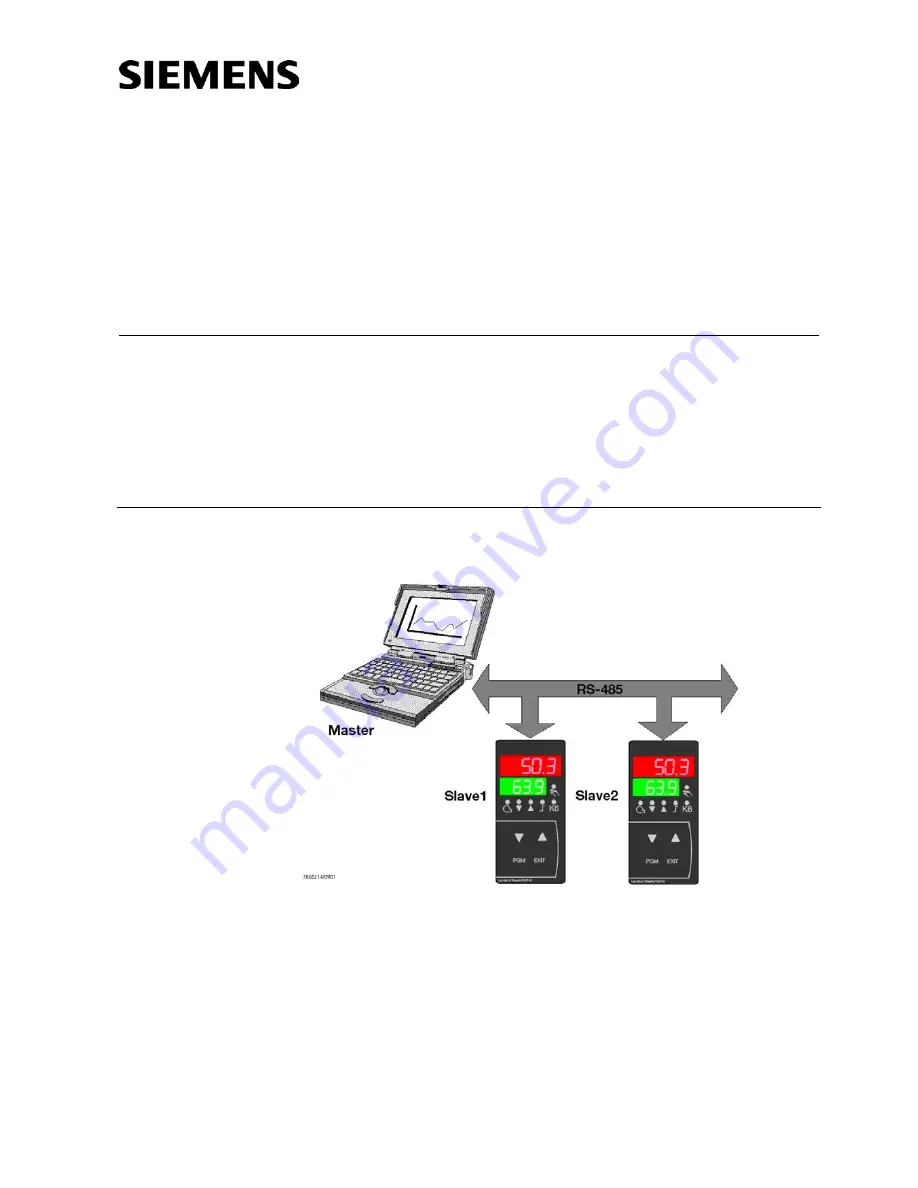
CC1A7865.1en
31.10.2002
Siemens Building Technologies
HVAC Products
7
865.1
Interface RS-485
RWF40...
The RS-485 interface is used for integrating RWF40… controllers into data networks
via MOD bus protocol.
Application examples:
-
Process visualization
-
Plant control
-
Reporting
Master-slave principle
Communication between a PC (master) and a device (slave) via MOD bus is based on
the master-slave principle in the form of data query / instruction – reply.
A master computer controls the exchange of data and can address up to 99 controllers
via device addresses (slaves).