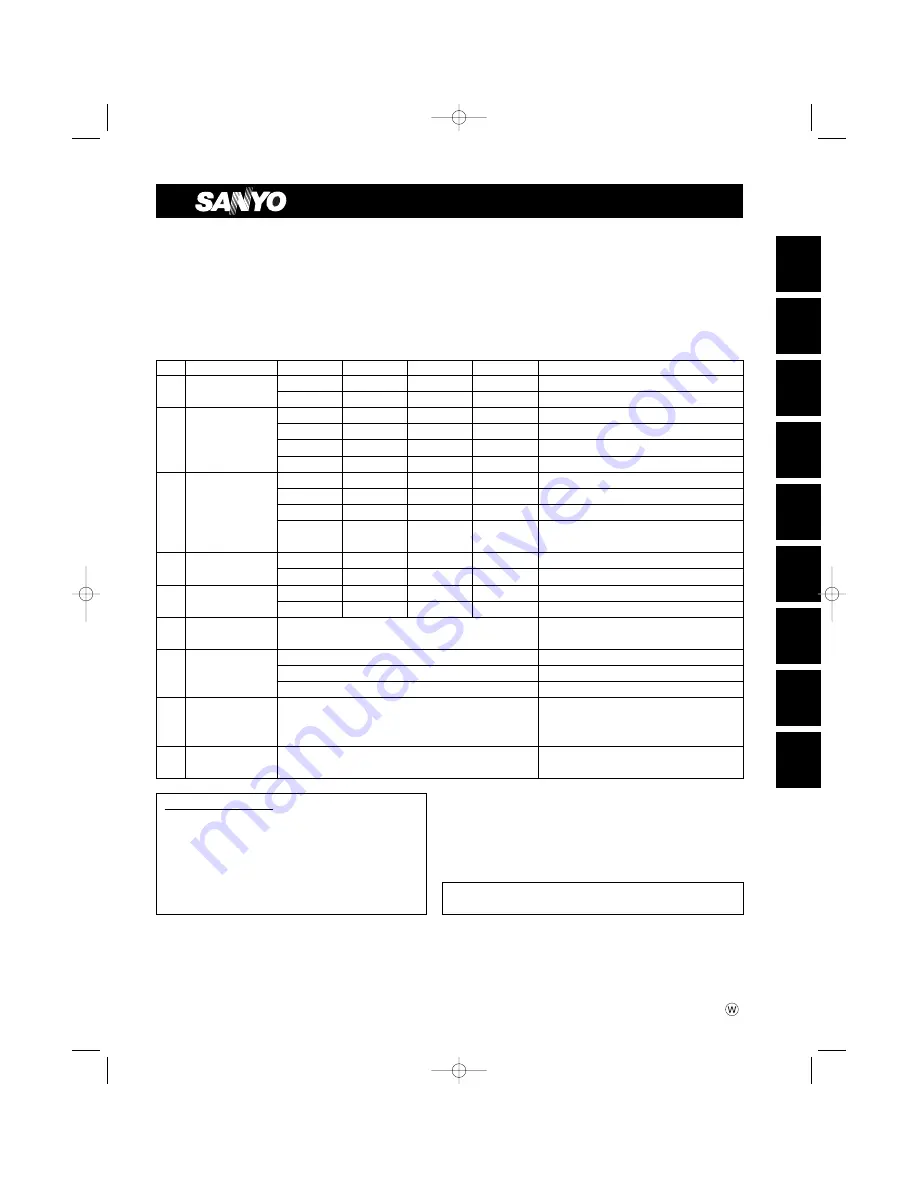
X
K
T
U
C
RC
(WD)
RC
(WL)
TRC
SC
85464359863005 ©SANYO 2007
– Split System Heat Pump Air Conditioner –
INSTALLATION INSTRUCTIONS
Model Combinations
Combine indoor and outdoor units only as listed below.
Indoor Units and Outdoor Units
* When air discharge chamber is installed.
OPERATING LIMITS
Maximum Conditions
Cooling
/ Heating
Outdoor temperature : 109°F DB / 65°F WB
Room temperature
: 71°F WB
/ 80°F DB
Minimum Conditions
Outdoor temperature : 0°F* DB
/ 5°F WB
Room temperature
: 57°F WB
/ 59°F DB
Units should be installed by licensed contractor according to
local code requirements.
Indoor Unit Type
26
30
36
42
Remarks
X
4-Way Air Discharge XH2672R
XH3672R
XH4272R
Optional remote controller
Semi-Concealed
XHW2672R
XHW3672R
XHW4272R
with Wired Remote Controller: RCS-TM80BG
KH2672R
KH3072R
KH3672R
Optional remote controller
K
Wall-Mounted
KHS2672R
KHS3072R
KHS3672R
with Wireless Remote Controller: RCS-SH1UA
KHH2672R
Optional remote controller
KHHS2672R
with Wireless Remote Controller: RCS-SH1UA
TH2672R
TH3672R
TH4272R
Optional remote controller
THW2672R
THW3672R
THW4272R
with Wired Remote Controller: RCS-TM80BG
T
Ceiling-Mounted
THH2672R
THH3672R
Unit with Back-up heater
THHW2672R
THHW3672R
Unit with Back-up heater
with Wired Remote Controller: RCS-TM80BG
U
Concealed-Duct
UH2672R
UH3672R
Optional remote controller
UHW2672R
UHW3672R
with Wired Remote Controller: RCS-TM80BG
C
Outdoor Units
CH2672R
CH3072R
CH3672R
CH4272R
H/P
C2672R
C3072R
C3672R
C4272R
S/C
RC
Wired Remote
RCS-SH80UG (Optional part)
(WD) Controller
RC
Wireless Remote
Built-in type: RCS-SH80UA.WL (Optional part)
for X and T type Indoor units
(WL)
Controller
External type: RCS-BH80UA.WL (Optional part)
for U type Indoor units
Built-in type: RCS-SH80UA (Accessory part / Optional part)
for K type Indoor units
Timer Remote
for X, T and U type Indoor units.
TRC
Controller
RCS-TM80BG* (Accessory part / Optional part)
* Timer Remote Controller comes with
Owner’s Manual and Installation Instructions.
SC
System Controller
SHA-KC64UG (Optional part)
SANYO Commercial Solutions
In Canada
A division of SANYO North America Corporation
SANYO Canada Inc.
Cornerstone Business Park
1-300 Applewood Crescent
1062 Thorndale Avenue
Concord, Ontario
Bensenville, IL 60106, U.S.A.
L4K 5C7, Canada
07-115 SSHP_II 5/7/07 3:59 PM Page a